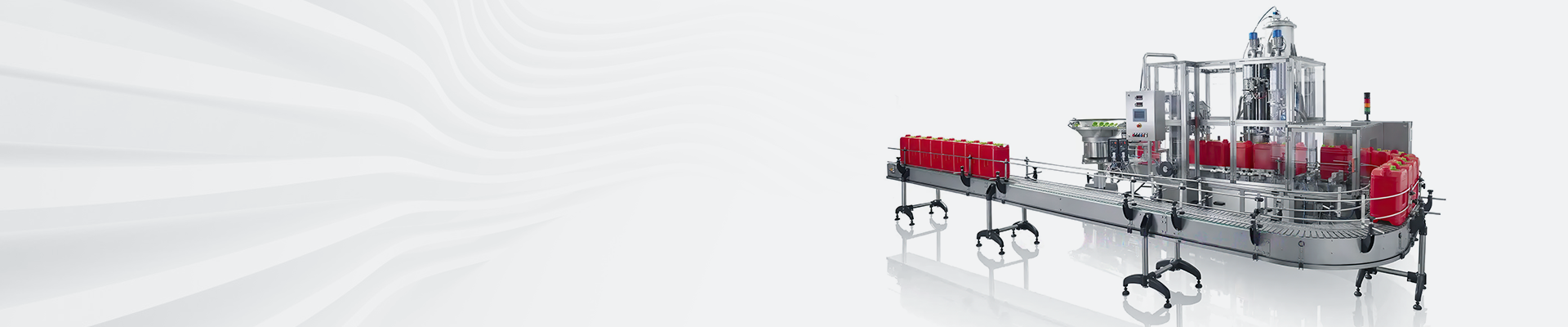
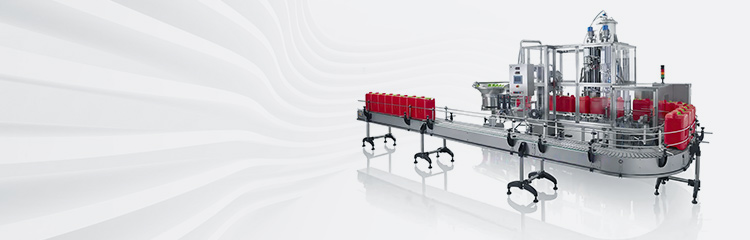

Summary:The continuous batching system compares this actual measurement value with the preset flow value, and at the same time controls the speed of the screw feeder to adjust the feed amount.When the material weight in the hopper reaches the minimum set value, the feeding valve will be automatically opened for periodic feeding operations.
In order to ensure efficient operation of the plant and to guarantee the quality of the product, the production process had to be optimized and highly automated, so the customer decided to replace the old system with a Siemens SIWAREXFTC system.
In the bread production process, in order to achieve continuous production of high-quality food, the customer requires high-precision continuous dosing and control of flour and various additives. The loss-in-weight dosing system feeds the flour at a preset flow rate into a dosing container, which also acts as a scale, mixes the material from the different loss-in-weight feeders and controls the flow rate of each loss-in-weight feeder between 1 and 4 T/H according to the preset weight value, ensuring the correct dosage weight ratio of each material. The loss-in-weight feeder can store approximately 200kg of material and is refilled every 3 to 12 minutes from the raw material silo above.
As part of the upgrade program of the weighing and dosage system, the old weighing instruments were replaced by SIWAREX weighing modules, which, thanks to the use of the new technology, make it possible to; improve the accuracy of the batch dosage metering, independent of external factors (e.g. mechanical vibrations, etc.); apply the metrological control of the flour metering to different types and densities; obtain and display the level and the weight value of the material separately; and be easily integrated into the Easy to integrate into SIMATICS 7 systems, allowing the perfect combination of weighing and control;
It was decided to use SIWAREXFTC weighing modules, which fully satisfy the requirements of metrological accuracy, with high-speed real-time weighing data processing and a variety of effective filtering capabilities. In addition, users have already experienced the unrivaled effect of the SIWAREXFTC's ability to operate remotely, by simply sitting in the control room and operating and setting up the various scales on site.
Loss-in-weight feeding systems (e.g. dosing containers containing a weighing device) read the weight value at regular intervals, and the difference between the two weights is used to calculate the reduction per unit of time (i.e. the instantaneous flow rate). The FTC weighing controller compares this actual measurement with the preset flow rate value, and at the same time controls the rotational speed of the auger feeder to regulate the feed rate. When the weight of the material in the hopper of the loss-in-weight scale reaches the minimum set value, it automatically opens the charging valve to carry out a cyclic charging operation. In order to ensure the correctness of the weighing results, e.g. to avoid the influence of mechanical vibrations, it is possible to select an appropriate filter for the filtering of the weighing signal during its measurement.
In order to realize this function, SIEAREXFTC can set the filtering parameters for the level and the weighing value separately. The modification of the weigh feeder was synchronized with the SIMATICS 5 to SIMATICS 7 system upgrade, so that the advanced SIWAREX weighing and dosage system could be well integrated into the SIMATIC control system.
Integration in SIMATIC allows direct recipe management and setting of preset values; dosing parameters can be easily set remotely for different materials; simple remote adjustment of dosing parameters is possible through the use of automatic acquisition of characteristic curves.
Easy to install and to read the weighs and set up the dosage system through various communication methods, for example through a modem or an Ethernet communication module for simple integration into the dosage system.
The weighing data is fed directly to the PLC system through the PLC backplane, which saves the communication between the weighing equipment and the PLC system, thus reducing costs, and at the same time realizing high speed weighing control.