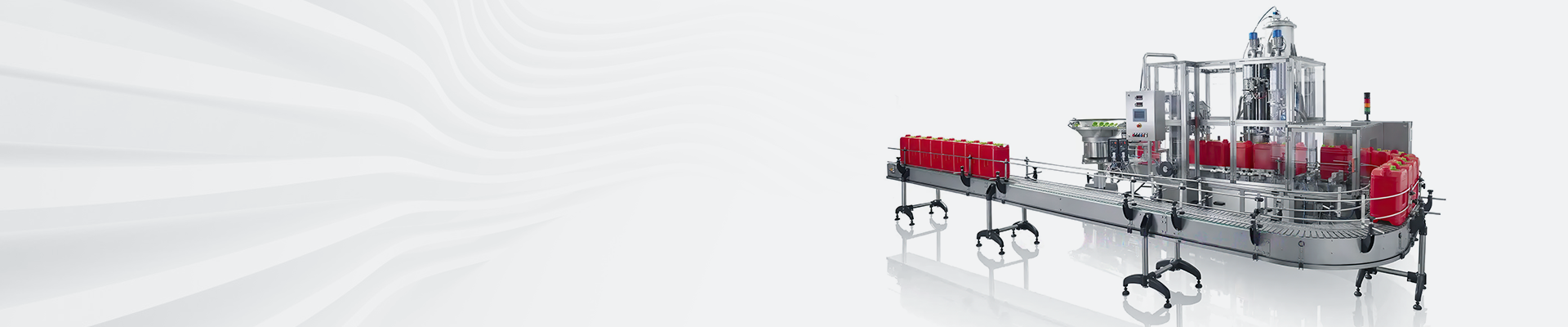
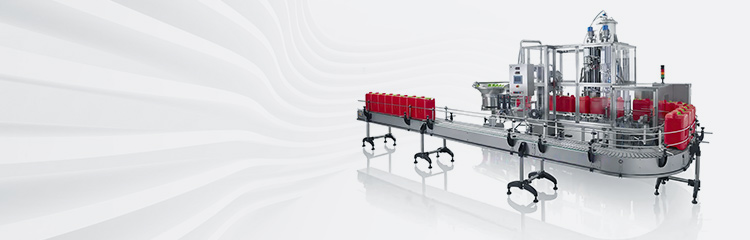

Summary:The batching system uses RFID radio frequency identification, and the mobile weighing device allows automatic addition of pigments to ensure smooth production.Data is transmitted via wireless technology, allowing production processes to be optimized.
It would not be feasible to use old control systems in existing soap production facilities. A comparative, detailed analysis and comparison of three machine control systems based on the Windows operating system led to the decision to use SimaticPCS7 from Siemens, including SimaticBatch, in order to safeguard the automation of our production process. What was needed was a comprehensive overall ingredient without the use of interface technology in order to avoid the risk of potential failures associated with interface technology. Decentralized configurations of peripherals and SimaticET200M as well as integration within the dosage, SiwarexFTA are very important.
The dosage station also utilizes SiwarexFTA electronic weighing equipment from Siemens, which increases the availability of the production equipment. The PCS7 control system paved the way for the company to use the Siemens Siwarex system. Coupling circuits connected with serial ports improves the reliability of the production equipment. Whereas in the past the control system was plagued with "interface" problems (errors in troubleshooting, errors in work logging), by incorporating it directly into the machine's main control system, the production operator can be accurately informed at all times about the status of the operation. In addition, not only the external measuring value detection and discrimination device, but also the on-site reading display device is omitted. The electronic modules are simpler to operate and use, cheaper to purchase and maintain, more time-saving, and safer and more reliable. We have not experienced any failures in two years.
The FTA weighing module offers a wide range of weighing functions and can be easily integrated into SimaticS7 and SimaticPCS7 systems. The technical renovation of the two batchers, which had been in use for 16 years, lasted two years. Installers laid a total of 25 km of cable and reconnected 2,500 input and output terminals. 3.5 km of fiberglass was passed through the two dosage lines, five Fiberopti-loops were constructed for the ProfibusDP fieldbus system, 120 electrical control cabinets were retrofitted, and 10 control cabinets were completely renewed. In the course of this technical modification of the control system, 30 existing weighing devices were dismantled and the new SiwarexFTA weighing devices were introduced. The company rates its overall uniform standardization extremely highly. These weighing modules work very reliably and are well serviced, with a ten-year parts supply guarantee from the time of production and use. If I get into trouble, I get help in the shortest possible time, which is not the case with every supplier, and that is precisely the point. Today, there are 46 Siwarex weighing and dosage systems, 11 SiwarexM and 35 of the latest SiwarexFTA modules in M's three soap dosage lines.
During the daily work of automated dosage, modifications to the dosage data are commonplace. At this point, a carefully selected topological network structure not only has a positive effect and significance in terms of safety performance only. Compared to ProfibusDP fieldbus systems with copper conductors, Fiberoptic cables with their ring network structure are much safer and more reliable. When one conductor is disconnected somewhere, the instrumentation in the fieldbus is able to continue working because they are connected in both directions. With copper cables, on the other hand, when one cable is disconnected, all the fieldbus instrumentation can't work (in severe cases, the entire dosing line has to stop working). "If at this point the paste-like raw material for the soap cools down and solidifies in the reactor, there is only one way to solve the problem - digging it out little by little like a coal miner. In the event of an unexpected malfunction, our losses would be very heavy.
The ring structure fieldbus system also allows the entire weighing control system to be separated while working and accessing new peripherals. Following this approach, the company added zinc oxide weighing devices not long ago to automate the weighing process (originally, this white powder required for soap production had to be weighed manually, at 10 kg per barrel).
Another innovation in the company's soap mixer is two mobile weighing devices. Originally, the so-called PlasticBeads device was used to mix different pigments into the soap to give it a rich color. The pigments were mixed with oil and controlled by a simple liquid weighing method. When people from the point of view of protecting the environment began to soap dosage production line for technological transformation, responsible for automation of the technicians also came up with new ways to solve the problem of pigment dosing and weighing, the key is to solve the pigment see oil after the "peeling effect" of the problem. The solution used in the American plant could not be used in the German plant because the mixers were not lined up one by one and did not have a uniform height. In addition, our workshop is on two floors, and the increase is double. That would have been too costly for us to build." The ideal solution: two mobile dosing units that can be carried up and down by an elevator. The design of the two mobile dosing units is also unique: they are transported without power cables and compressed air lines. There are only power sockets and quick sockets for compressed air on both dosing units. The data transmission is wireless and relies on industrial WirelessLAN technology. An RFID system supplied by Siemens ensures that the operator always knows what color pigment is in the weighing unit. The mobile weighing unit allows us to weigh the pigments flexibly and keeps production running smoothly.
The weighing module, which is easily integrated into the Simatic PCS7 process dosage, has a weighing accuracy of ±1 to 2 g per 100 g. Accurate dosage control also directly contributes to the reduction of raw material consumption in the soap factory. Saving raw materials is very important to us. If the quantitative control is not accurate, it will waste money, in addition, it will make the color change, increasing the cost of color mixing. Accurate dosing is the key to product quality.
Before starting the technical modification of the existing soap feeder, the biggest challenge was to complete the modification in a short period of time. The timeframe for the technical modification of the control system was only 6 weeks, after which the dosing line was required to be up and running again, and was required to run at a much higher level of efficiency. Siemens' SimaticPCS7 and the new, integrated Siwarex dosage system greatly reduced the workload of the company's engineers and technicians in retrofitting the process equipment control system in less than six weeks. We were able to complete the job ahead of schedule and secure the projected costs. The pace of production on the new system is also much faster than before the retrofit. The higher degree of automation of the equipment increases the reliability of the production process and reduces the labor intensity of the operators." The German soap production plant was so satisfied with their technical modification that it has moved their colleagues in the US and in Denmark to this technical solution.