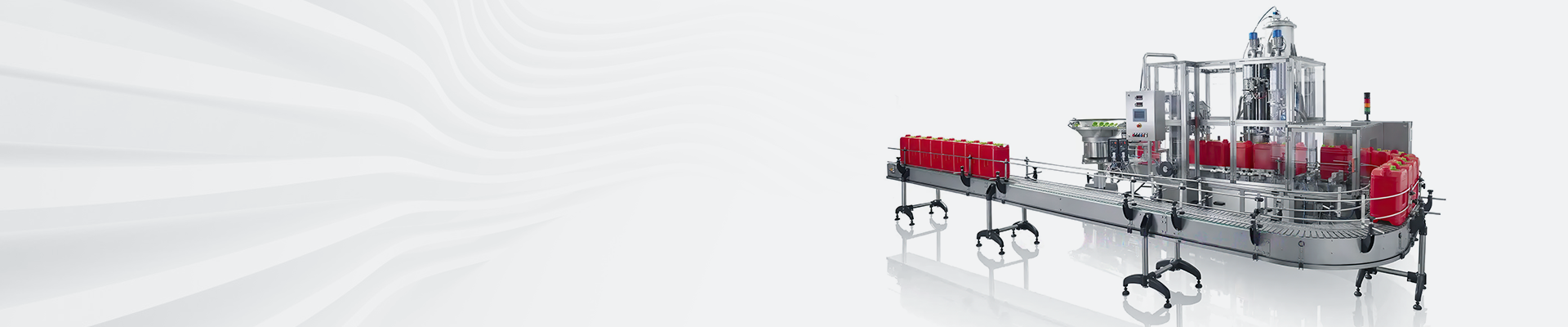
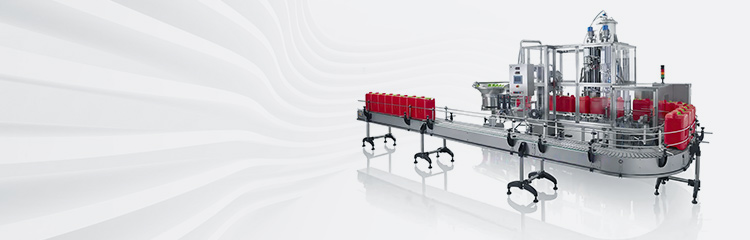

Summary:The automatic batching system will pass through the materials on the belt and detect the weight through the weighing sensor under the weighing scale frame to determine the weight of the materials on the belt.The speed signal and the weight signal are sent to the belt feeder controller to generate and display the cumulative amount/instantaneous flow rate.
In the process of coke production process, four kinds of coals, namely, gas coal, fat coal, coking coal and lean coal, need to be dosed into a mixture of coals according to a certain ratio, and then sent to the coke oven for high-temperature coking. The accuracy of proportioning and the reliability of batching will directly affect the quality of coke products. Therefore, to improve the quality of coke carbon by improving the reliability, stability and accuracy of batching has very important social and economic benefits.
The metering and feeding system of coking is of great significance to the quality of coke and the production operation of coke oven. In order to make the proportion of coal more accurate, it is feasible and ideal solution to realize stable and reliable automatic coal dosing.
B. Composition and main functions of batching
The automatic batching system is mainly composed of weighing module, feeder, data acquisition and batching control system, electrical control system and upper computer, software and network.
Composition of batching structure
Weighing feeder will pass through the materials on the belt, through the weighing scale frame under the weighing sensor to detect the weight, in order to determine the weight of the materials on the belt; installed in the tail drum or rotating equipment on the digital speed sensor, continuous measurement of the feeding speed, the speed sensor pulse output is proportional to the speed of the belt; speed signals together with the weight signal is sent to the belt feeder controller, to produce and display the cumulative amount / instantaneous The speed signal, together with the weight signal, is fed to the belt feeder controller, which generates and displays a cumulative/instantaneous flow rate. The feeder controller compares the flow rate with the set flow rate, and the output signal from the controller controls the frequency converter to adjust the speed, realizing the requirement of quantitative feeding.
The core part of the weighing feeder is the belt scale. The main components of the belt scale are the scale frame, the accumulator and the speed sensor; and the structural characteristics and accuracy of the weighing feeder system are usually determined by the design structure of the belt scale. The weighing and batching system generally requires the batching scale to have 0.5% accuracy; the system control accuracy reaches 1%, and the main functions:
(1) Detecting the flow rate and cumulative amount of each scale in real time;
(2) Reliably control each scale to operate at a constant flow rate according to the given value;
(3) Optimized calculation and delivery of ratio and total batching quantity;
(4) Dynamic simulation screen display of on-site process flow, proportioning, bar graph, historical curve graph, etc;
(5) Setting and rewriting of on-site process, operation and process parameters;
(6) Various kinds of fault limits, alarm prompts and logging, automatic bin change processing;
(7) System proportioning accuracy evaluation;
(8) Database, printout function.
Third, Siemens fully integrated weighing program design
Generally speaking, the controller of weighing feeder used for batching is divided into three modes: stand-alone controller, unit controller and PLC-type controller. Stand-alone controller is generally used and belt scales with control functions of the accumulator or the use of microcontroller technology-based controller to achieve the advantages of flexible configuration, one-to-one correspondence with the use of weighing and feeding machine, a device failure does not affect the work of other equipment, belongs to the distributed control; the disadvantage is that it can be achieved to limit the functionality of the system often need to be equipped with other control systems in order to achieve a more complex control functions. The disadvantage is that the functions can be realized are limited, often need to be equipped with other control systems to realize more complex control functions. Unit controller is based on the PC bus industrial computer, the advantage is powerful, intuitive and convenient operation, belongs to the centralized control; the disadvantage is that the system reliability is not high, the current use of this approach is not a lot of manufacturers.
PLC type controller is to PLC this kind of control equipment commonly used in industrial production as hardware, through the software configuration to realize the function of dosage. Its advantages are: flexible configuration, communication methods, cost-effective, especially suitable for multiple weighing and feeding machines together to form a larger system; disadvantages are: many companies use PLC I/O input function to directly accept analog signals from the weighing module, not only poor accuracy, but also anti-jamming ability is very weak, in some units also appeared in the system as a whole out of control of the serious accidents. Siemens launched and SiemensSimatic system is fully compatible with the SiwarexFTC solution, can be very good to make up for the shortcomings of this program.