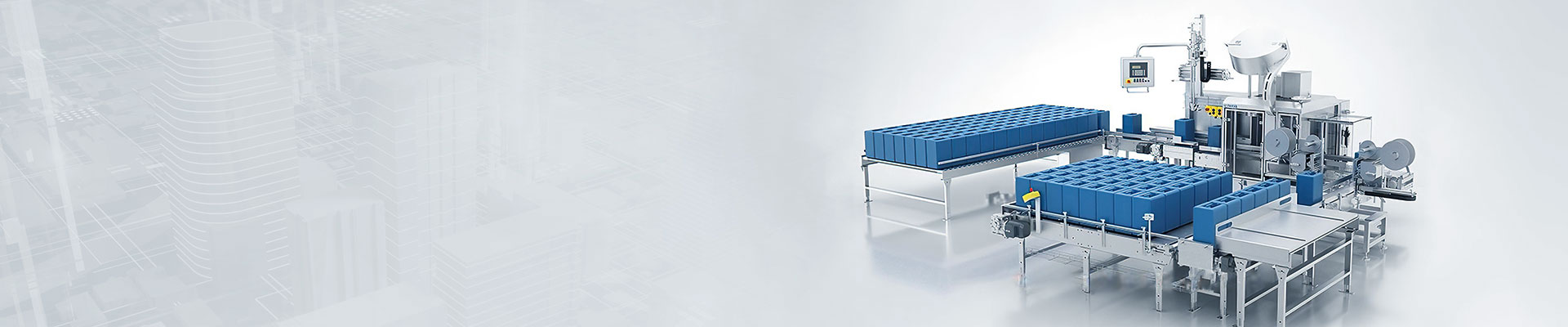
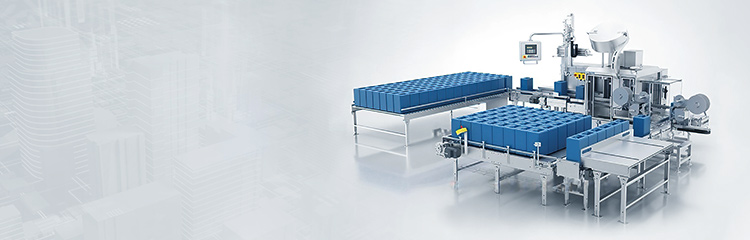
The automatic batching system is connected through the communication bus to form a network, decentralized control, centralized operation and centralized management, which is easy to achieve centralized command, scheduling and management of the whole plant, automatic detection and control of the entire production process, and automatic control of the start and stop of some electrical equipment. Each site workstation completes the collection and control of various analog signals (pressure, temperature, flow, valve opening, etc.) and various switching signals (motor, position and material level, etc.), and completes signal processing, sequence control, control algorithm, PID adjustment and fault diagnosis in the site station.

The automatic feeding system adopts Siemens S7-400 PLC as the lower computer, PLC communicates with two EM200 sub-stations and Siemens MM440 frequency converter to collect and process the field data and simple control, and PLC communicates with the upper computer with CP443 Ethernet module to exchange the system operation data. Configuration software uses configuration software to design the following configuration interfaces: home cover, login interface, equipment operation interface, dosage setting interface, recipe interface, real-time data interface, report interface, system diagnostic interface and so on. In the upper computer, the monitoring system mainly accomplishes the following tasks: display, processing and setting of various powder weighing on site; recording, saving and querying of on-site data, and alarming of important data; simulation of production site; setting of batching formula and simulation of screw conveyor. The system mainly completes the data acquisition and control of iron powder weighing, batching and feeding, and realizes the monitoring of material weighing, batching and feeding.
Batching monitoring interface design
1、login interface using the login function "LogOn ()", easy to call the login dialog box, the operator and management personnel user name and password set in the development system.
2、dosage operation interface is feeding 5 screw conveyor and dosage scale image screen, can realize automatic, manual operation and maintenance options. In automatic mode, the feeding and dosing actions are controlled automatically. In manual operation, the operator manually controls the start/stop operation of the equipment with chain function. The maintenance state is for maintenance use, the system does not control the equipment, all control behavior is completed by the field operation, there is no chain function.
3、dosage setting interface displays real-time material level and material type of each reactor, and the weighing terminal displays current real-time discharging speed and set discharging speed. The interface of setting system PID control parameters, and can be changed to manually control the frequency converter to control the amount of material discharged by each batching scale. There is each batching scale overload or lack of material alarm display, convenient for operators to adjust the material parameters in a timely manner to ensure stable operation of the system.
4、Recipe interface using the recipe function, there is no limit to the number of recipe storage. Selection of the warehouse function, select the feeding reactor and material type and input the total amount of dosage, the system automatically calculates the amount of dosage according to the selection and the formula, the calculation results are displayed in the dosage setting interface and stored, and the data are finally provided to the report.
5、real-time data interface through the rectangle color change to display the feeding screw conveyor, unloading reactor, dosage scale, inverter, soft starter and all other equipment real-time operation and fault conditions, easy to operate.
6、The report interface provides daily and monthly reports. Using the report system provided by the configuration software, it can be used as easy and convenient as using Excel and is powerful enough to support all the functions of Excel. Support for reading the software history database data, support for inserting charts, security settings, with operating privileges of the personnel can change the report data, and can be output as an Excel table file, completely free from the operator to manually calculate and fill out the report.
7、system diagnosis is the EM200 sub-station and frequency converter communication test, while there is an alarm window to query the historical alarm data. The overload and lack of material on the dosage scale, the overload of screw conveyor, the operation failure of the frequency converter, and the operation failure of the soft starter can all be recorded for query.