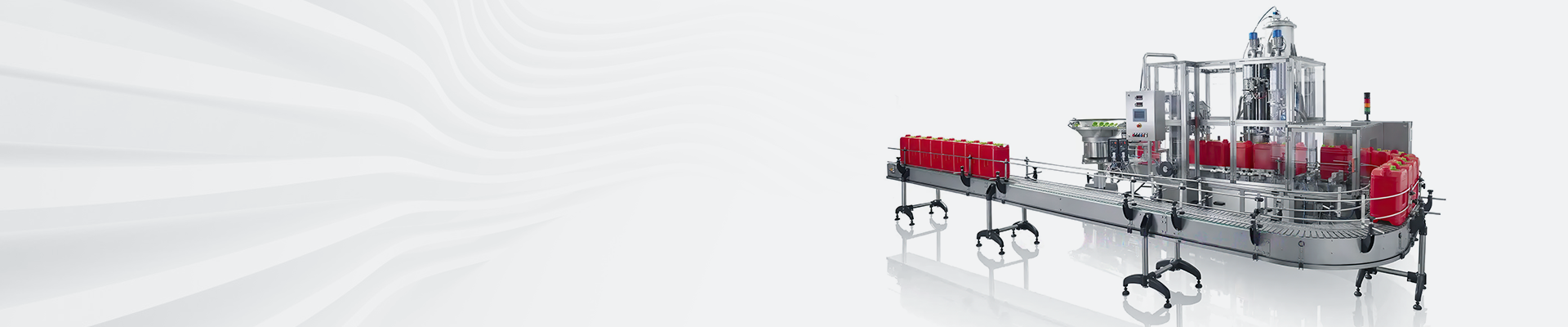
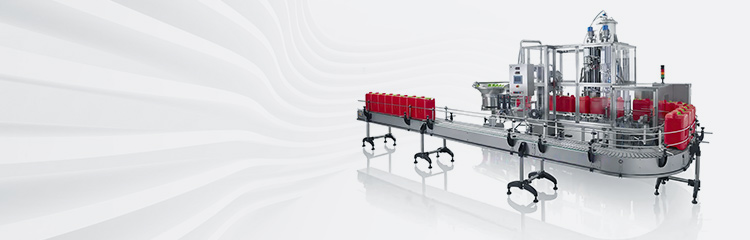

Summary:The reactor batching system realizes fully automatic control of the glue making and using processes. From glue requirements, formula parameters, preparation to transportation, the whole process is controlled by PCC, without the need for dedicated personnel.
The main process of batching
The main process of glue batching production line consists of reactor weighing (including three reactors of starch, lye and resin), transit reactor (including three reactors of borax, lye and resin and their common weighing device), one main reactor and its weighing device, and four finished product reactors and their measuring device.
This glue batching equipment is equipped with automatic alkali mixer (using carbon steel kettle body), stirring device, lye storage tank and two lye pumps, lye transfer kettle and piping are made of stainless steel. After flake alkali is converted into liquid alkali, it is stored in the lye storage tank. The liquid level of the lye transfer reactor can be automatically controlled by PCC, when it is lower than the set low limit, the lye pump will be automatically started to replenish from the lye storage tank.
The starch storage reactor is carbon steel reactor body, equipped with screw conveyor, vibrating feeder, and fitted with high and low material level weighing module. The main reactor is equipped with steam heating device and automatic temperature control dosage system, equipped with temperature detecting element, secondary temperature meter and steam cut-off valve, and adopts PCC to control the temperature.
Each glue point storage reactor is equipped with liquid level detection and stirring device. The glue weight of each glue storage reactor can be displayed and monitored in real time on the touch screen in the glue making room.
Weighing and batching process overview
First of all, from the storage reactor of borax, resin and lye to the transfer reactor: the above three transfer reactors are fixed on a frame supported by three weighing modules, sharing a set of weighing device. Both resin and lye are liquid at room temperature, and the transit storage reactors are equipped with the highest and lowest level floats. The first time only add resin, when its liquid level reaches the position of the high float to stop adding, at this time the weight shown on the weighing instrument of the transit reactor is the weight of the resin, which is also its maximum value. The second time also only add lye, when the liquid level reaches the high float position, stop charging, at this time the weight displayed on the meter minus the weight of the resin added for the first time, that is, the weight of the lye. Save this calculated value as the current weight of lye. Although borax is a solid, it is also dosed and measured in the same way. In the starch savings reactor, there are high and low level weighing modules and vibrators. When the high level is reached, no more starch can be added to the storage reactor, and the low level signal prompts for dosing. The function of the vibrator is to vibrate the starch loose, vibration, to prevent starch bridging. When it is lower than the lowest material position, the vibrator will be automatically activated to vibrate down the starch attached to the kettle wall.
Borax, resin and lye are added to the main reactor during glue production. These three ingredients, are added individually. If the lye is currently being added, the weight of the transit reactor will become smaller, and this difference is the weight of the lye injected into the main reactor. The current lye weight in the transit reactor is the original weight minus the weight of the lye injected into the main reactor. Save this value as the current lye weight.
The other two materials are also added to the main reactor in the same way. The flow of the glue making process is as follows:
Process flow of glue batching and preparation production line
Each cardboard production line actually requires only one type of glue, and different cardboard production lines have different formulas. At present, the glue dosage system is equipped with 4 kettles (with steam heating device), each kettle has a different formula of glue, these 4 kettles are located next to different cardboard production lines, connected with the main reactor through the pipeline, and the heated glue is sucked to the corresponding kettle by an air pump from the main reactor.
The dosage is equipped with automatic correction function of the formula, when the dosage is added, the deviation in the dosage process can be monitored through the screen, and the dosage ratio can be automatically corrected according to the ratio of the formula, in order to ensure the accuracy of the formula; it can be connected with the customer's raw tube dosage system, and the amount of glue can be determined automatically according to the order to be produced by parameter setting, so as to minimize the wastage of the glue; after the first time of inputting the formula, when customers need to adjust the formula, there is no need to adjust the formula again, so that it will not be necessary. After the initial input of the formula, when the customer needs to adjust the formula, there is no need to calculate the change of the material, just directly input the result of the change of the glue, the program can automatically modify the formula; there is an automatic blowing function, when each reactor glue delivery is completed automatically blowing glue to avoid clogging of the hose.
Composition of feeding system
The feeding system is composed of B&R2003 series PCC as the core, combined with the weighing instrument PANTHER. The PCC is equipped with a BP704 (4-slot backplane), the CPU is installed in the left end of the backplane, and a double-width module CP476 with 24VDC power supply is selected, which has RS232 and CAN interfaces each with a status indicator, as well as four screw-in module slots, which need to be expanded by inserting the screw-in modules into the slots and fixing them with the fastening screws. The screw-in modules can be analog or digital modules or communication expansion modules.
One of the slots is equipped with IF321, which is equipped with an RS485/RS422 interface for data communication with 1#, 2# and 3# instrumentation stations, and the other slot is equipped with AI774 (4-channel analog input module), which is used to collect the level (corresponding to the weight) of the gel level from the 4 finished reactors. In addition, the PCC is equipped with 2 DM465 (16-input and 16-transistor output digital mixing module) and 1 DM435 (8-input and 8-transistor output digital mixing module). For the operation and monitoring of the dosage system, a PowerPanel 4PP320.1505-31 color TFT 15" touch screen (24VDC, 1 Ethernet10/100M, 1 RS232 and 2 USB interfaces) is used as the human-machine interface (HMI).
Composition of the glue making machine
Two sets of weighing instruments (model T600, max. weighing selection 5-10000kg, graduation value 0.005-10) are selected for the weighing and feeding machine, one set for the main reactor and one set for the transit reactor. Each set of weighing instrument consists of 3 weighing modules and a secondary instrument with logic control function (including weighing module for bridge power supply). They are characterized by high precision, good reliability, professional material handling ability and friendly man-machine interface, which play a very important role in improving production efficiency. Adopting advanced bus technology, it can conveniently use Profibus, RS232, RS485 and MODBUS-Plus and other field buses to realize high-speed data communication with relevant PLC (PCC) systems, constituting strong real-time, good reliability and flexible configuration, which can conveniently satisfy the needs of all kinds of users for weighing and dosing.
Working principle and main functions of dosage
The feeding system is equipped with two working modes, manual and automatic, which can be preset before production and can be switched with each other according to the needs in the production process. When each reactor glue delivery is finished, it will be automatically blown. The highly automated design of the dosing system can realize the full automatic control of the glue making and glue using process, from the demand of glue, formula parameters, preparation until delivery are controlled by PCC in the whole process, without the need of personal operation.
The feeder has the main functions of multi-recipe storage, automatic recipe selection, parameter setting, multiple cost reports, automatic weighing and injection and dosing control, automatic glue delivery control and so on.
It is equipped with automatic formula correction function. When adding materials, you can monitor the deviation in the process of adding materials through the operation screen, and automatically correct the subsequent adding proportion by changing the proportion of the formula to ensure the accuracy of the formula.
The mixer can also realize data communication with the customer's production management. Through data exchange, the amount of glue to be made is automatically determined according to the order of paper products to be produced in order to minimize glue waste. After the initial input of the formula, if the customer really needs to adjust the formula, there is no need to recalculate the change of materials, just directly input the result of the glue change, the program can automatically go to modify the formula.
External USB storage, complete record of several important process parameters of the historical data.
Working Principle of Automatic Weighing and Batching
The automatic weighing and dosing unit is the core part of the glue making control, which determines the quality of glue preparation and production efficiency. The dosage machine adopts two sets of electronic weighing devices, secondary instrumentation and PCC to realize the control of all materials weighing injection and dosage, in order to control the whole dosage process more accurately, and to ensure that the glue formula is accurately executed.
Considering that the data communication between the CPU of PCC and each instrumentation station adopts RS485 serial communication mode with quite low rate, if PCC undertakes the digital filtering of the weighing value, it has to collect data from each PANTHER weighing terminal several times continuously in each scanning cycle of the program and needs to spend a long time, which may affect the accuracy of the digital filtering of the weighing value and directly affect the weighing result. This may affect the accuracy of the digital filtering of the weighing values and directly affect the weighing results. For this reason, the PANTHER weighing terminals have been assigned the task of digital filtering of the weighing values in the design of the dosage system, and the patented TraxDSPTM digital filtering technology is perfectly suited for this task, as the PCC only needs to collect the digitally filtered weight data from the PANTHER terminals during each scanning cycle via the RS485 bus network and process it subsequently.
The borax, resin and lye transit reactors are small in size and, due to the weighing process, are fixed on a table supported by three weighing modules and share a common set of weighing instruments. Their inlet and outlet pipes are all connected by metal hoses to avoid additional stress.