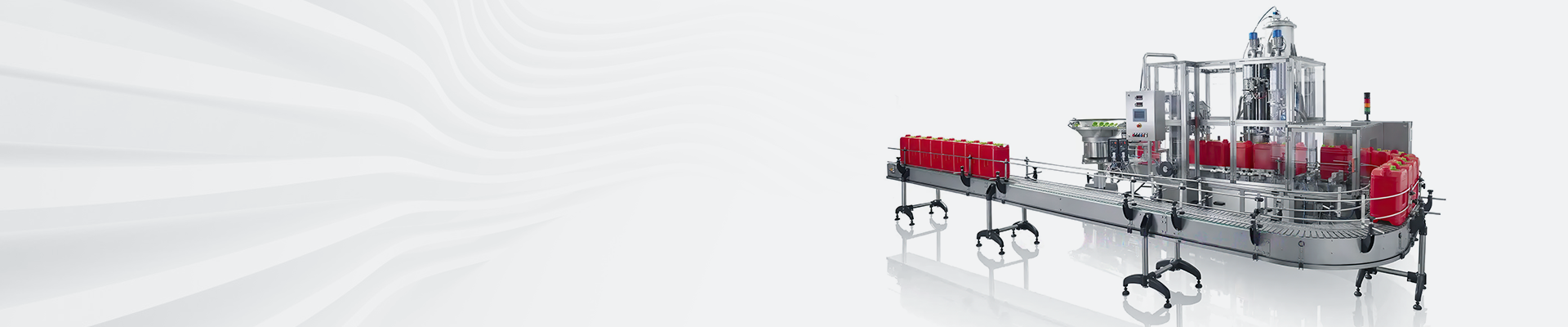
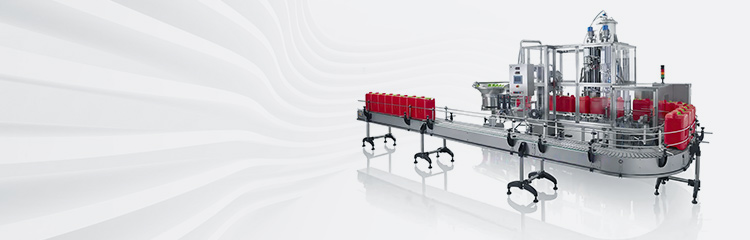

Summary:The DCS automatic batching system is a computer composed of a host control computer unit, Mitsubishi Q00CPU and a weighing instrument.Complete the start/stop of working status control and chain control of faults in each link.
The traditional magnetic powder production line adopts relay control system, low degree of automation, poor reliability, maintenance difficulty, can not meet the user needs. In this paper, the use of SANRONG PLC and MOVICON configuration software to form a control system, so that the entire production line to achieve automatic control and terminal monitoring and protection, to improve the production accuracy of the key processes, reduce the labor intensity of workers to improve production efficiency.
2 Production line process introduction
Magnetic powder production needs to be selected according to different grades of components, and then sequentially dispersed sand milling and mixing, burning and screening processes to get the final product particles. One of the most critical parts of the process is the dosing process and tender burning process.
In order to realize the feeding, and the size of feeding according to the production requirements of continuously adjustable, take the quantitative feeding device. The dosing process is as follows: press the dosing start button on the PC, the system first detects that the material level of each raw material bin is not low, selects the iron oxide bin or spare bin, and then waits for the request dosing signal from the disperser, otherwise, it does not start the dosing scale. When the starting condition of the dosage scale is satisfied, the system weighs the weight of big water, manganese oxide, zinc oxide, iron oxide and small water according to the pre-set weight of the PC, and the weight can be changed arbitrarily on the F800 dosage meter).
Burning process on the pre-burning reaction of the temperature, pressure and atmosphere required to take the temperature, pressure control device and can realize automatic adjustment, so that more suitable for high-performance ferrite wet pre-burning.
3 control system introduction
Magnetic powder automatic dosage system adopts three wither CCLINK field bus control, in the central control room with the main control cabinet of each process section and the central operating desk, in the central operating desk is equipped with two PCs and a variety of reaction site temperature, pressure and weight of the instrumentation, which is a PC as the monitoring of the entire powder line, the site is equipped with four cameras to monitor the operation of the production equipment, and the other PC as the powder line. The other PC is used as the upper computer of the dosing control system, adopting MOVICON monitoring software to monitor the operation status of each production equipment in the powder line, including manual, automatic, stop, emergency stop and other states. In each process section, there is a small on-site control box, with simple operation buttons and indicators on the panel of the box, and CCLINK I/O modules inside, which are connected to the on-site control of solenoid valves, position switches, level meters, buttons, etc. The central control room PLC is connected to the on-site control of the powder production line. The central control room PLC and each field CCLINK module to form a CCLINK field bus control.
4PLC system
4.1 Hardware configuration
Mitsubishi Q series PLC is a modular PLC system to meet the requirements of large and medium-sized systems, in order to adapt to a variety of automation control tasks, the module can be freely expanded. The batching machine using the CPU for the Mitsubishi Q06H. In order to meet the analysis of statistical production line detection and control of the functional requirements of the object, the entire system requires an Ethernet module QJ71E71-100, four CCLINK remote communication module QJ61BT11N, four analog input and output module Q68ADI, seven input module QX40, nine output module QY10 and 19 CCLINK field input and output modules. Figure 2 shows the hardware configuration.
4.2 Program Design
The main task of PLC system is to complete the manual and automatic logic control of production line equipment. LAD ladder modular programming, program readability. According to the process requirements set up 9 program blocks: batching program block, dispersion 1 program block, pre-burning program block, dispersion 2 program block, mixing 1 program block, mixing 2 program block, red spray program block, finished product program block and data transmission program block. Batching process is the core process of the whole production line, the following briefly introduces the application of PLC system in the batching process:
1) After pressing the batching start button on the PC, the system firstly detects that the material level of each raw material bin is not low, and selects the selective pass of the iron oxide bin and the standby bin on the screen, and then waits for the requesting batching signal from the disperser, and does not start the batching scale if one of the conditions is not satisfied. As in Figure 3:
2) When the start-up conditions of the dosage scale are satisfied, the system weighs the proportional weights of large water addition, oxidation, zinc oxide, iron oxide, and small water addition, which are set according to the process flow. (The proportioning weight can be changed arbitrarily on the F800 dosage meter).
3) The working process of weighing is as follows: start the dosage meter, set the meter to 0. Weigh the big water first, the big water valve opens, and closes automatically when it reaches the set value. Then scale manganese oxide, the instrument output coarse feeding SP1 and fine feeding SP2 two signals, so that the spiral and vibrating hopper running at the same time, in addition to the spiral feeder compressed air arch breakers also began to work, spiral feeder through the frequency converter for high-speed feeding (Y1BD) when weighing to the fine feeding, the end of the coarse feeding signals, spiral feeder through the frequency converter to low-speed operation (Y1BE), while vibrating the hopper to stop, when the scale to the fine feeding, the signal end of the coarse feeding, spiral feeder through the frequency converter to low-speed operation (Y1BE), at the same time vibrating hopper Stop, when the screw feeder runs until the weight is the same as the set value, the meter outputs the signal of the end of iron oxide weighing, in the process of coarse charging, the discharge scale mixes at high speed, and when waiting for fine charging, the batching scale mixes at low speed. After a delay of 5 seconds, set the meter to 0 again.
4) Weigh zinc oxide and iron oxide in turn. Then start high-speed mixing for 15 minutes (time can be set through the MOVICON screen), open the discharge valve after mixing is completed, discharge time is 2 minutes (Figure 5) and then begin to add water, weighing is completed after the start of small mixing, stirring time to open the discharge valve, discharge time for zinc oxide, iron oxide weighing. Weighing is completed after the start of high-speed stirring for 15 minutes, stirring is completed to open the discharge valve, discharge time is 4 minutes. After all the weighing is finished, a weighing completion signal is output. It marks the end of a weighing, and at the same time, it will start the high-speed dispersing program block when the weighing count is 1 and the count is 2.
5 Monitoring System
5.1 Monitoring Software
MOVICON is a new generation of automation monitoring software, developed by the famous Italian automation software supplier PROGEA. The company has been developing automation monitoring software based on Microsoft Windows platform since 1990, and the software is known for its simplicity, stability and reliability. According to the process requirements of the production line control system design ten man-machine function screen, directly on-site equipment operation status for real-time monitoring and alarms, setup, management process parameters.
5.2 Industrial Control Machine
As MOVICON is based on Microsoft?Windows platform development of hospitality monitoring software, so the industrial control machine using an ordinary PC, the installation of the program using the Windows2000 system. MOVICON will check the user's authorization to run, the authorization of the hardware for the USB dongle.
5.3 Establish communication between MOVICON and PLC
1) PLC communication settings
Use PLC programming software GX-DEVELOPER to set PLC network parameters:
IP address setting in operationalsetting (operationalsetting);
Port settings in the open settings, port 2000, 2001 for the hexadecimal, and in the MOVICON communication settings need to fill in the decimal value, 2000, 2001 corresponds to the decimal 8192, 8193.
2) MOVICON Setting
First add the communication driver: Mitsubishi-MelsecQTCP, and then open the driver's property window, in its statements property group, press the "Add" button to increase the definition of the station, usually a station definition corresponds to a PLC, you can define a number of station definitions of multiple PLCs.
5.4 Creating MOVICON Variables
1) Click the ellipsis to the right of the dynamic attribute item in the Variable Attribute Window to open the Variable Browser. Select the communication driver in the Variable Browser window, double-click the defined Melsec-QTCP in the Communication window to open the Task Properties window, and select the station AA defined above and the PLC to be associated.
2) Fill in the Dynamic Properties item directly in the Variable Properties window.
5.5 Creating Monitor Screen
MOVICON development system provides rich graphic objects and animation connection types, such as command language connection, analog value output connection, attribute change connection, blinking, rotating connection and so on. Through the animation connection of graphic objects in the screen and the command language program, it realizes the synchronous dynamic change of the screen monitoring system and the production site data.
5.6 Setting up MOVICON software to run automatically after starting the industrial computer system
MOVICON software installation generated by the MOVICON.exe running system shortcut copied to the "system to start a program a start", so that the industrial control machine will automatically run MOVICON once the start. can be transmitted to the monitoring system in real time and production process control.
Conclusion
Once the feeding system is used, it reduces the key process difficulties in the production process and improves the working efficiency, product capacity and qualification rate, which fundamentally improves the automation of the magnetic powder production line, which has been used by the user for 3 years with good results.