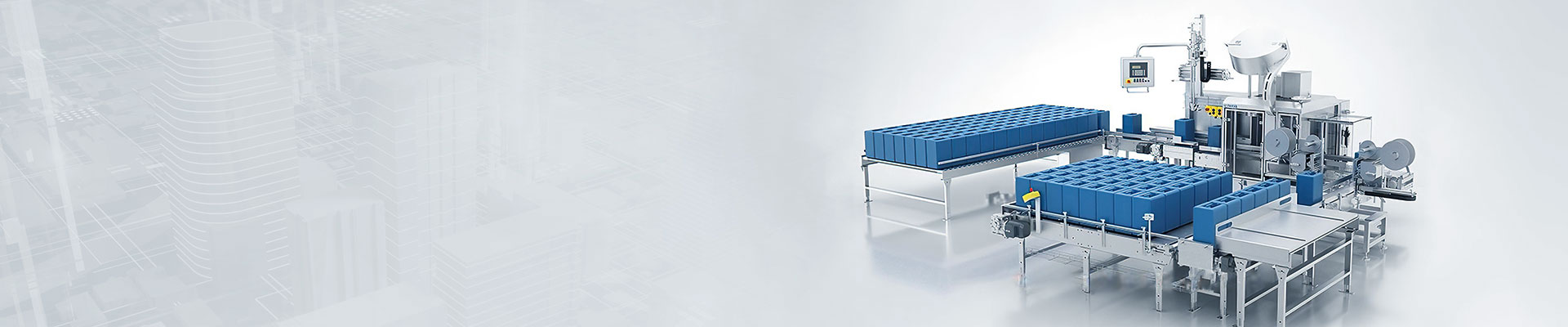
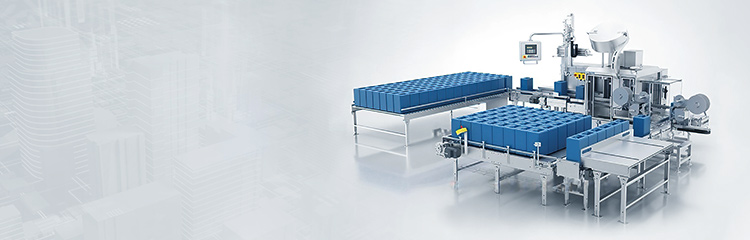
The batching system consists of hardware and software. The hardware part mainly consists of a mixing tank, a mixing tank cover, a stirrer, a load-bearing weighing module, a weighing instrument, a transmission device, a shaft seal device and the like, and a programmable controller, an upper industrial control computer weighing system and the like; The software part mainly includes the control algorithm of programmable controller and the monitoring program of upper industrial computer.

Automatic Batching system mainly uses the energy of airflow to convey liquid+powder materials along the direction of airflow in a closed pipe, which is a specific application of fluidization technology. Pneumatic conveying device is simple in structure and convenient in operation, it can be used for horizontal, vertical or inclined direction conveying, and in the process of conveying, it can also be used for physical operation such as heating, cooling, drying, airflow classification or some chemical operation. Compared with mechanical conveying, pneumatic conveying system consumes more energy, the particles are easy to break, and the equipment is easy to be abraded. More water content, adhesion or easy to generate static electricity in high-speed movement of the material, not suitable for pneumatic conveying. Pneumatic conveying is mainly characterized by large conveying capacity, long conveying distance, high conveying speed; can be loaded in one place, and then unloaded in many places. The dosing system can solve the various problems of measuring and mixing.
Feeding system in order to ensure the accuracy of the dosage, requires the use of frequency converter / screw feeding method. This can make use of the function of the analog quantity in the multi-material dosage weighing instrument to drive the frequency converter directly, which can improve the accuracy of dosage. At the same time, in order to save cost, two spiral machine share a frequency converter, rely on the PLC command intermediate relay to select through different contactors to drive different motors, first in the weighing instrument to enter the recipe, start the dosage, the PLC detects the scale is in the zero range, start to start the first material fast dosage, the frequency converter to high-speed operation, to the amount of fast dosage, the frequency converter to a low-speed operation, to the slow dosage, the frequency converter stops running, the instrument for slow dosage, the frequency converter is running. After the inverter stops running, the meter carries out the over-difference detection, after the detection is finished, the time is delayed, and then it starts to batch the second kind of material, after the batching of the second kind of material is finished, if there is over-difference, the over-difference alarm will be output, then the meter outputs the signal of unloading, and waits for the unloading of the material. If there is any fault in the process of dosage, the dosage can be aborted at any time.
The automatic Dosage system adopts HMI+PLC system, which integrates multiple sensors and actuators into a powerful weighing and dosage control system, and it can be applied to various chemical operation units which require precise control and measurement of quantitative dosage. The automatic control system is PLC+HMI fully automatic control, the signal collected by the load cell is transmitted to PLC by the weighing transmitter, and after the PLC program operation, the dosage is controlled automatically and the relevant parameters are displayed on the HMI interface.
The batching equipment is centrally installed on a steel base, and the whole set includes Weighing system, insulation system, feeding system and automatic control system. The weighing system consists of weighing module, weighing bracket, level adjuster and accessories. The heat preservation system consists of storage tank, mixer, liquid level meter, solenoid valve and pipeline. The dosing system consists of dosing pump, safety valve, back pressure valve, pulse damper, pressure gauge, ball valve, pipeline mixer, pipeline and accessories. Pneumatic ball valve is used for dosage, and after weighing, the material is discharged by controlling the pneumatic ball valve. The control unit is equipped with PLC to realize the control requirements. The dosage storage tank is installed with high and low level switches to detect and control the high and low level of the tank respectively. When the high level is reached, the inlet motorized ball valve 1 shuts down the inlet action, and when the low level is reached, a warning is issued and heating is stopped. The lower barrel storage tank uses a low liquid level switch and weighing module for automatic control of the liquid level, when the metering module detects the lower limit of the set value, it automatically opens the middle motorized ball valve 2, and discharges the pre-heated medium from the upper barrel to the lower barrel; when the weighing module detects the upper limit of the set value, it closes the motorized ball valve 2; in addition, the lower barrel is also equipped with a low liquid level float switch, when the lower barrel of the liquid is transported to the end of the low liquid level, the system When the liquid in the lower drum has been conveyed to the low level, the system turns off the heating, stops the metering pump and issues an alarm.