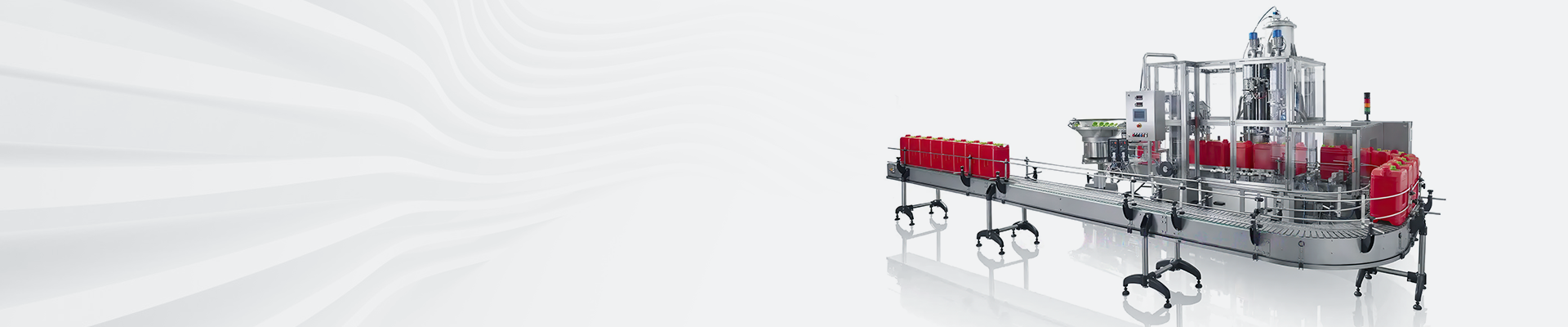
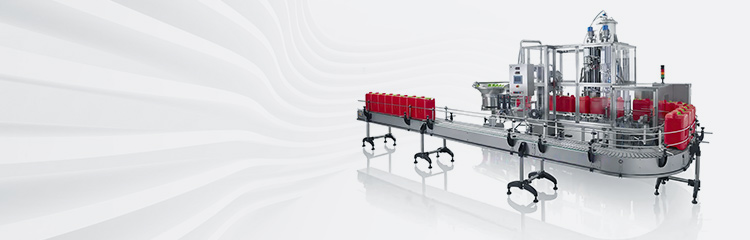

Summary:Automatic dosage system through the weighing instrument and motor current through the field weighing instrument remote transmission to the central control room centralized display, inverter regulation equipped with automatic switching switch, and the main control computer communication.
Automatic dosage system is a very important process in the production process of fine chemical enterprises in an electronic scale, dosage system consists of two sub-systems before and after the dosage. Before the dosage system in the general control of the microcomputer dosage system under the control of hydrocarbons, aromatic hydrocarbons, fatty acids and their esters, phenols, amines and other liquid solvents in the dosage reaction pot after stirring to form lubricating oil. After aging and temporary storage, the lubricant is pumped by high pressure pump into the reaction kettle, and the lubricant is formed after stirring by dosage. The former dosage system mainly accomplishes the weighing and proportioning of the main material and various ingredients. After the dosage system will be formed by the former system of lubricating oil through the conveyor mixing tank, and the pump solvent, non-ionic and other solvents mixed with the liquid by the transmission of the finished product mixing tank. After the dosage system realizes the measurement of the flow of the conveyed material.
Lubricant production automatic blending and blending system using Siemens PLC and configuration software, through the sensor to complete the temperature, flow and liquid level data acquisition and processing. The industrial control machine is equipped with special communication card and friendly human-machine interface, powerful configuration king software, remote communication and real-time monitoring of the whole system. The centralized control system is formed by connecting the PLC and the industrial control machine through Profibus-DP network. Anti-interference ability and practicality of the automatic control system.
The automatic batching system adopts DCS centralized control mode, and selects Siemens S7300 PLC to form the data acquisition and control system, which is modularized design and economical and practical. The human-machine interface monitoring software adopts "Configuration King", which is the leading configuration software in the field of industrial control in China and has the advantages of good openness, easy maintenance and secondary development. All process control data and equipment operation status can be centrally managed, recorded in real time, and printed and consulted at any time.
The automatic batching system is composed of computer, weighing module cabinet and peripheral equipment. The automatic dosage monitoring system consists of two computers as the human-machine interface of the whole system. One of them is the master station, which completes all the system parameters setting, process monitoring and data recording; the other one is the slave station, which takes the master station as the support, and is in charge of the data setting and process monitoring of the batching system after the master station. The master station communicates directly with Siemens S7300 PLC, the front batching scale automatic control weighing instrument and the rear batching scale. The front dosage control system adopts sealed junction box, which is dust-proof and moisture-proof and ensures reliable signal transmission. The former dosage scale adopts special industrial process controller, which communicates with the central control room through RS485 bus, and can be independently controlled or realized PLC on-line control.
The batching system is also equipped with monitoring system, which has the functions of human-computer interaction, communication, display and storage, printing, etc. It also has data and graphic display, status monitoring, data input, information storage and other function screens related to operation. It can realize real-time process data monitoring, simulation display of process flow, real-time data record access, operator authority setting, process parameter setting, setting alarms for running process events and switching between manual and automatic control.
In the monitoring system, the on-site control weighing instrument displays real-time flow, load, totalized value, temperature, etc. The temperature is indicated by the on-site temperature weighing instrument. Temperature indication is through the on-site temperature weighing instrument, pressure indication is through the on-site pressure display weighing instrument and the current of the motor is transmitted to the centralized display in the control room through the on-site weighing instrument. The frequency converter is equipped with automatic switching switch and communicates with the main control computer. Automatic weighing control unit is mainly for weighing and batching instrument, PLC as auxiliary control system, computer human-machine interface display proportioning parameters (formula) and monitoring and recording of real-time data. In automatic control mode, click the automatic dosage "start" button in the front process screen, or the front control cabinet "start" button, the weighing control instrument will open the material valve according to the set formula. If the system detects that a dosage valve is not closed, an alarm occurs and the system enters the pause state. Each weighing valve is equipped with an advance quantity, when the control instrument detects that the weighing weight reaches the set value, the electronic scale will subtract the advance quantity, and the control weighing instrument will close the feeding valve. The advance amount can be corrected manually or automatically, so that the controlling weighing instrument can control the dosage scale to reach the set target value every time the dosage accuracy.