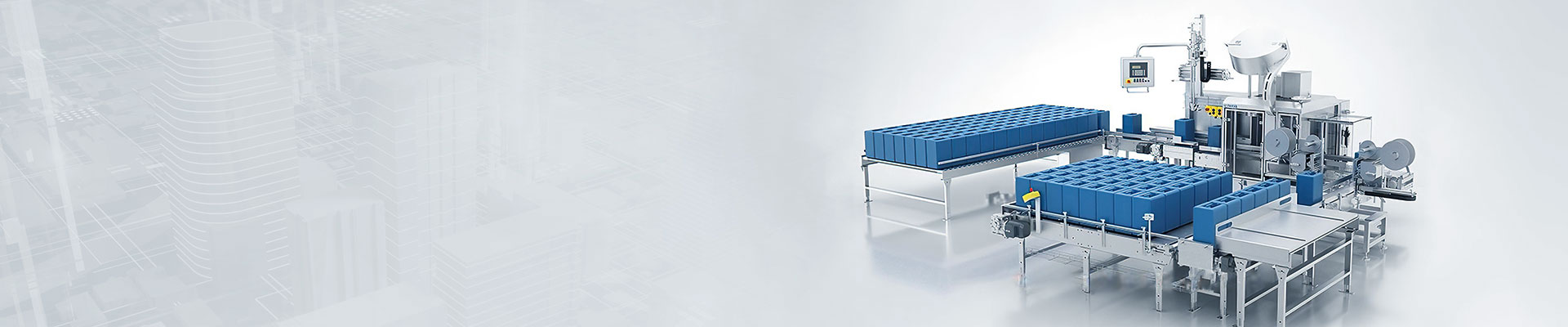
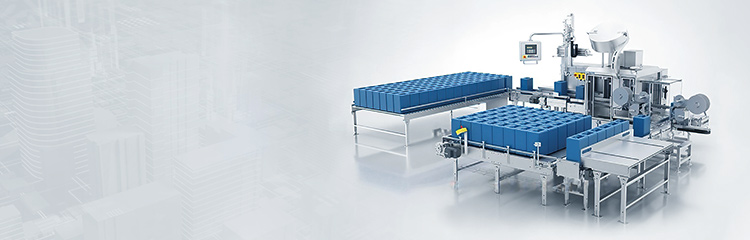
The automatic feeding system adopts DCS control system, the pneumatic, stopping and running of the whole system are controlled and monitored in the control room; the whole equipment is equipped with fault detection system, if the equipment in the rear section fails, the equipment in the front section stops by itself and displays the location of the fault point and the reason, and shows the system running status with alarm light; the control mode adopts three-level control mode: upper machine position → PLC → dosage instrument. The control interface is simple and clear, with animation displaying the dosage process and dosage data, which is clear and eye-catching; the personnel in the control room contact with the field personnel through the walkie-talkie.

Automatic loading system specializing in chemical, energy battery, pharmaceutical and other special industries. These industries process production, dust inevitably dispersed into the air, and the special nature of the chemical plant, a lot of dust is flammable and explosive. When the dust in the air diffuse to a certain solubility is very easy to explode, very dangerous. Therefore, these production plants must require production equipment with explosion-proof performance. Production of automatic feeding system suction machine, the use of control systems completely using pneumatic logic components to complete the way, high-quality explosion-proof control box, so as to achieve national explosion-proof requirements. Ensure the safety of production personnel, corporate assets are not damaged.
Weighing and loading system adopts DCS control system, the whole system pneumatic, stopping and running are controlled and monitored in the control room; the whole equipment is equipped with fault detection system, if the equipment in the rear section fails, the equipment in the front section stops by itself and displays the location of the fault point and the reason, and shows the system operation status with alarm light; the control mode adopts three-level control mode: upper machine position → PLC → dosage instrument. The control interface is simple and clear, with animation displaying the dosage process and dosage data, which is clear and eye-catching; the personnel in the control room contact with the field personnel through the walkie-talkie.
The whole automatic Dosage system uses nitrogen as the power source and protective gas air as the power source, nitrogen is only used as the protective gas conveying process to reduce the solubility of oxygen in the gas-object mixture. The dosage system adopts the principle of negative pressure suction, and the whole process of sealed pipeline conveying, to prevent dust leakage. With electrostatic protection device, and other multiple safety measures, we use only rest assured that peace of mind.
Through the compressed air can control and run the whole system; weighing instrument automatic control, in 0 ~ 30 seconds to set the suction and discharge time at will, simple and convenient operation; small size, light weight, easy and fast installation; no vibration, low noise and dust-free operation, cleaning and changing the material is fast and convenient; do not need to warm up, standby, low maintenance costs; no need for electricity and other energy sources, no heat generated by the operation of the equipment, safe and explosion-proof and so on. Many advantages.