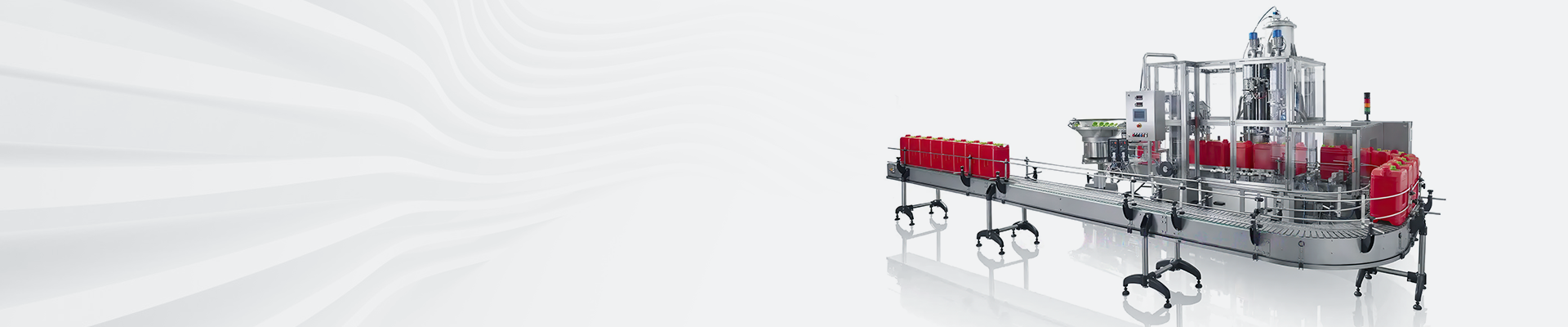
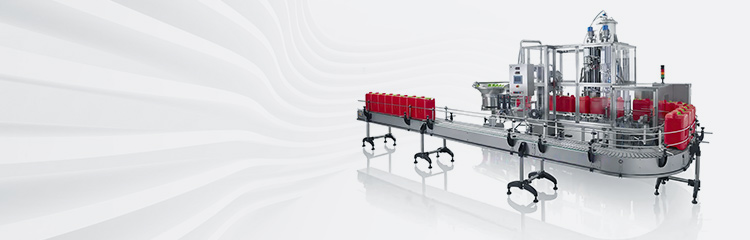

Summary:Due to the mechanical characteristics, the residual material phenomenon at the end of the converter bulk material vibration process, from time to time affect the accuracy of the bulk material weighing system, for this phenomenon to take the automatic adaptive control technology, and achieved good results.
0 Preface
In the converter production, the accurate weighing of bulk material is of decisive significance for the end temperature and molten steel composition. In the automatic control system of converter discharging, based on the characteristics of electromechanical equipment, the vibrating motor is controlled by frequency conversion, and the frequency conversion is set to high speed when the vibrating material is started, and then it is changed to low-speed operation when 95% of the discharging volume is reached. However, because the electric vibrating screen for discharging material has obvious hysteresis effect when discharging material, weighing adaptive control technology is adopted in 120t converter system of steel area.
1 Problem analysis
In the weighing process of bulk material, if the start and stop of the batching equipment is controlled according to the actual readings of the weighing equipment, it will inevitably lead to excessive underfeeding. The general solution is to turn off the electric vibrating screen in advance, so that the amount of material is basically close to the set value. There are different solutions to determine the amount of advance, you can use the experimental method, the data of many repeated discharging statistical processing, in order to obtain the optimal amount of advance. However, this method requires the collection of a large amount of data, a large number of experiments, and there are seven or eight kinds of converter auxiliary materials. Experiment one by one, the workload is very huge. Adaptive control technology on the converter discharging system is a good solution to this problem.
2 key technology principle
In the first discharging, when the weighing instrument display value and the set value difference, stop vibration material, delay 5 seconds, the collection of weighing instrument final readings, calculate the final discharging amount and set the difference between the amount of discharging to determine the value of the positive and negative, if the value is positive, the discharging amount of insufficient, too large an amount of lead time, the next time the next discharging, the amount of lead time should be reduced; if the value is negative, it means that the amount of lead time is too small, the next time the discharging, the amount of lead time should be increased. Increase the amount of advance.
At this point, with the increase in the number of times the material, the amount of advance will continue to increase, and ultimately produce two kinds of results: one is to make the value just within the error range; the second is to make the value of the number of positive numbers, the calculation, and the value of 0 is positive when the formula is the same.
3 transformation implementation
Using the opportunity of fixed repair, the 3 "120t converter of Yinshan steel area for bulk material discharging system transformation, comprehensive analysis of the operation of the system after the transformation, in the 1", 2 "converter fixed repair period, the bulk material batching machine to carry out the corresponding transformation.
3.1 Screw scale composition
Certain powdery materials should not be weighed by batching scales, and screw scales can be used. Due to the limitation of its structural characteristics, the weighing accuracy is lower than that of the scale.
(1) Calculation, display, control and adjustment device. The role is the same as the dosage scale, but the object of speed regulation is to feed the motor.
2) Scale body. The scale body consists of screw feeding cylinder, driving motor and pivot point. Pivot point position should be in the center of the feed port, in the absence of material spiral cylinder and drive motor in the pivot point on both sides of the weight is basically equal, when transporting materials, materials from the inlet to the outlet run, the pressure on the sensor gradually increased. The whole scale is the structure of cantilever scale.
3) Soft connection. Used to connect the scale and feeding equipment, both to prevent material leakage, but also to make the scale and feeding equipment between the connection does not affect the weighing. Commonly used materials for chemical fiber, rubber, etc..
(4) load cell. The felt gravity is converted into an electrical signal output, with the same role of the sensor in the dosage scale. As the spiral scale is heavier, the sensor range is not too large, so we should pay attention to the weight balance of the spiral feeding cylinder and drive motor, if necessary, add counterweight to adjust. Weighing is the same as the scale, but there is no speed measurement signal. That the speed is constant, determined by the power supply frequency.
3.2PID control
1) The relationship between the speed control device and the deviation. Batching given value and real-time flow rate is equal to achieve the best dynamic equilibrium; batching given value is greater than the real-time flow rate, speed control device speed increase, flow rate increase; batching given value is less than the real-time flow rate, speed control device speed decrease, flow rate decrease. In order to reduce the frequency change of frequency converter, set 1 dead zone, i.e. -2‰<T<2‰, the frequency converter does not change, the motor speed is unchanged, at this time, it is believed that the best dynamic feeding balance state.
2) Communication. The communication method adopted by Zhanggang is field bus Modbus, the main control center exchanges data with the instrument in real time through PLC, and the parameters of the system can be set and monitored through the upper computer, which is convenient to operate and reliable to control, and the whole system realizes a high degree of automation, and forms a closed-loop control system that is both relatively independent and interconnected. Adopting bus transmission, it has long distance and strong anti-interference ability.
(3) When the material passes through the load cell, it generates a voltage signal which is proportional to the load, and this signal is processed by the digital display instrument and compared with the given value of the dosage, and the output value of the frequency converter is changed through mediation and calculation, and the speed of the motor of the disk feeder is controlled, so as to control the amount of material under the disk. Batching scale control of the basic mathematical model is very complex, commonly used classical incremental control model, Zhang Gang used intelligent algorithms. Therefore, it will not produce oscillation overshoot, and the adjustment speed is very fast.
(4) Automatic control processing. Observe the historical curve of the dosage scale flow on the upper computer, analyze the fluctuation of the flow in the time period, if the curve change is small, it means that the dosage is better; on the contrary, it means that the dosage fluctuates greatly. Gradually reduce the value of the PID adjustment coefficient and observe the historical curve until the curve change is small. If the change of the regulation coefficient does not work, such as in winter, should be used in the bin next to the fire measures. If there is not enough material, you should check whether the opening of the material mouth or the material door is too small, and whether the material bin itself is timely under the material.
(5) PID control regulation and dosing relationship. In order to make the opening or running without big fluctuation, the following measures are taken: opening process, when manually switching to automatic operation, in the manual conversion time, the PID current constant output, feeding stability. After the manual time, the instrument enters into automatic control of feeding, so that the flow rate of several materials and the cumulative amount of the stage are kept within the set range. According to the size of the set value, calculate the size of the manual PID output current, according to different kinds of materials to determine the size of the manual duration, the principle does not exceed 10 s.
3.3 Switching between old and new systems
As the above parameter settings are only experimental data, it is uncertain whether they can be adapted to normal production. In order to avoid weighing errors in the production process, affecting the quality of steel, so retain the original weighing system program, and set up with the new program switching button, in the event of an accident can be switched back to the original program, to ensure the normal production. After observation, the new feeding system has been able to stabilize the feeding error within 5kg, which basically meets the process requirements. After that, the bulk material feeding system of 1" and 2 converter was modified with adaptive technology.
4 Conclusion
The adaptive control technology in the 120t converter bulk material weighing control system after the application of continuous tracking observation shows that the system runs stably, the error and weighing error is basically matched. The advantages of this automatic dosing system are.
1) Once the system is stabilized, it will no longer need to be adjusted. If the material particle size and viscosity changes, the system can be automatically adapted to adjust, reducing the huge workload caused by repeated debugging.
2)After the system is used, the waste caused by excessive material is reduced, and the cost of raw materials is lowered.
3)The feeding amount of bulk material is more accurate, which makes the composition of molten steel more in line with the process requirements and improves the quality of molten steel.