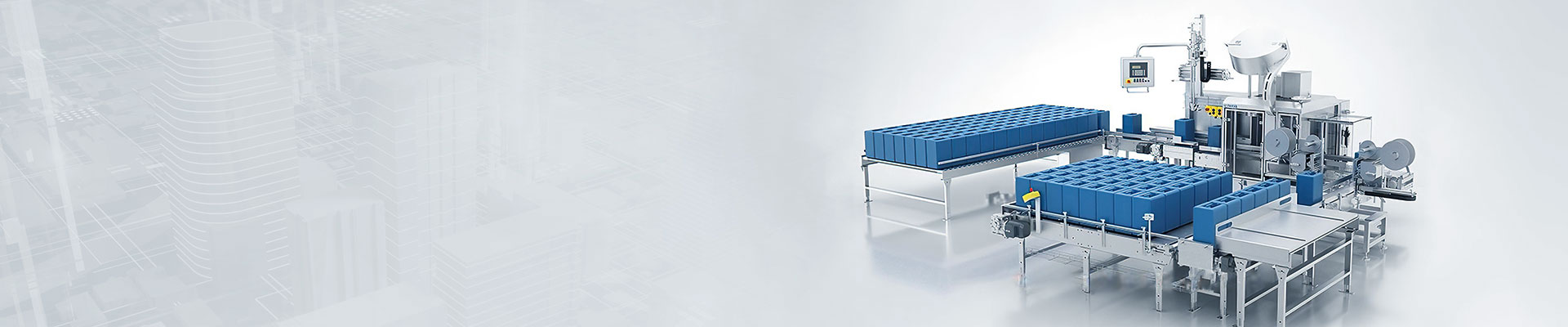
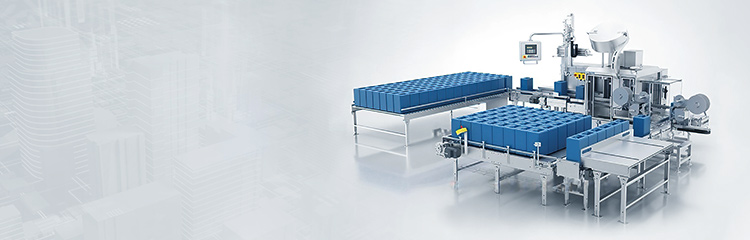
Bulk scales install the weighing module under the hopper, usually with 3-4 load cells. The weight of the material is converted into an electrical signal by the sensor and amplified by the amplifier in the measuring circuit for display, recording and data processing. The new electronic bulk material scale can weigh gross weight, tare weight and net weight, with automatic zeroing and weighing data processing function. It mainly consists of weighing hopper, bracket, pneumatic valve, high-precision load cell, junction box, signal cable and intelligent weight indicator.

Automatic bulk weigher to ensure the control system precision and speed, the use of direct-fall feeding, double screw feeding or double vibration feeding and so on. After the quantitative start, the big and small Feeders work at the same time, stop the big feeding when the material weight reaches the big feeding setting value, and continue to keep the small feeding, and close the small feeding when the material weight reaches the final setting value. It is mainly composed of hopper scale, weighing module, weighing controller, etc. It can complete the accurate measurement of materials and send the control signals required by the control system: over and under quantity signals, preset advance signal, advance signal, target value signal, 4~20mA analog signal and standard RS232/485 signal.
The control system of bulk material weigher adopts double weighing and quantitative control realized by relay, the feeding motor feeds the preparation hopper, and the material enters into the hopper weigher from the preparation hopper, at this time, the weight of the material in the hopper weigher is collected by the sensor through A/D conversion by the weighing instrument, and the weighing instrument collects the data continuously and calculates the current speed of the hopper weigher feeder according to the time difference of the collection. The pre-set value is then compared with the weight of the material in the current hopper and the time needed to continue feeding is calculated. As the weighing instrument constantly collects data and makes judgment to calculate the new feeding speed and the time needed to feed, coupled with the preparation hopper feeding into the hopper weighing the size of the feeding port is controlled by the weighing instrument, so it can ensure the accuracy of measurement.
The feed motor feeds the hopper, and the material enters the hopper scale from the hopper, then the weight of the material in the hopper scale is collected by the load cell through A/D conversion by the weighing instrument, which continuously collects the data and calculates the current feeding speed of the hopper scale according to the time difference of the collected data. The pre-set value is then compared with the weight of the material in the current hopper and the time needed to continue feeding is calculated. As the weighing instrument constantly collects data and makes judgment to calculate the new feeding speed and the time needed to feed, coupled with the preparation of hopper feeding into the hopper weighing the size of the feeding port is controlled by the weighing instrument, so it can ensure the accuracy of measurement. One of the weighing instrument is to control the size of the feeding port of the hopper: at first the feeding port is the largest (big cast), when the weight of the material in the hopper weighing is close to 70%~80% of the set value (specifically set by the software part of the weighing instrument), the feeding port shrinks partly (medium cast), close to 80%~95% (specifically set by the software part of the weighing instrument), the feeding port shrinks to the smallest feeding port (small cast), finally when the hopper feeds into the hopper weighing is controlled by the weighing instrument, so it can guarantee the accuracy of the measurement. Finally, when the weight of the material in the hopper plus the weight of the falling material in the air reaches the set value, the feeding port of the hopper will be closed and the weighing will be finished. Hopper weighing unloading into the container bag can be sealed. Since the hopper weigher can not feed the material while unloading into the container bag, the preparation hopper needs to wait for the hopper weigher to finish unloading every time it feeds to the pre-set value of the hopper weigher before it can feed the material again.