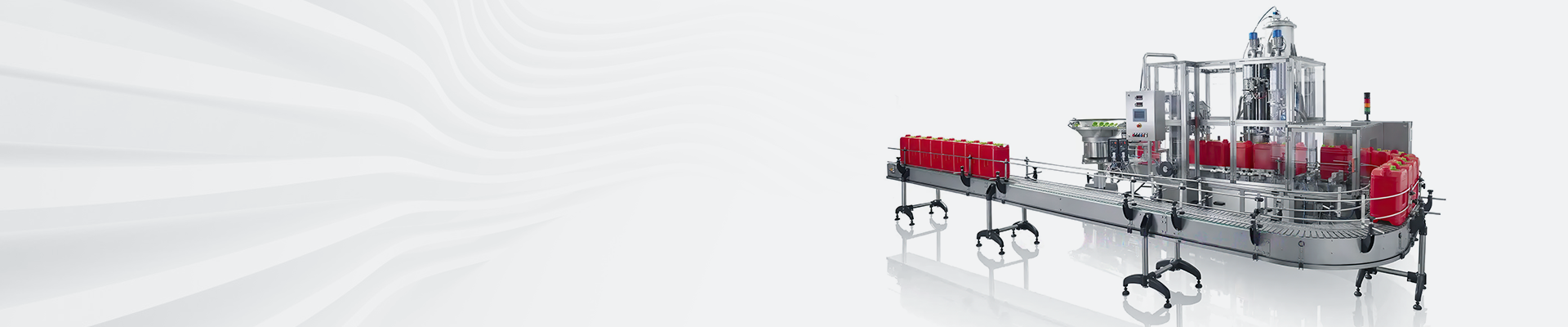
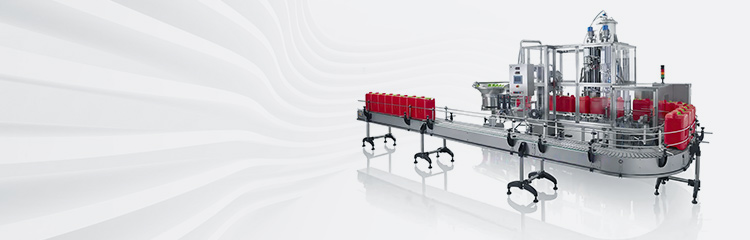

Summary:The reactor batching system completes the transportation, measurement, loading and unloading of paint materials. The weighing site consists of reactors, weighing devices, automatic valves, operation boxes and other equipment; it is mainly controlled by a PLC controller, a computer and a weighing instrument. room console.
Paint factory paint production, every day need to put a lot of paint materials, etc., paint material loading and unloading, storage, transportation, the process of metering difficulties, management difficulties and other issues. For Guangdong China Resources Coatings freight paint loading and unloading production, transportation, measurement of the site conditions, the use of PLC technology designed to transform the dosage of weighing and metering control based on the metering kettle dosage of paint to carry out the transformation. The weighing and dosing system by the reactor coloring tank (reaction tank), servo conveyor, discharge gate, manipulator and conveyor control system, constituting the weighing and metering conveyor system, to complete the paint material transport, measurement, loading and unloading work. To solve the control of paint measurement, conveying at the same time, the upper computer software system and the company's financial system networking, real-time update of the network database, to facilitate the work of the financial staff, and to save manpower and material resources, to achieve paperless office management.
I. Application site overview
Reactor dosage system under the transportation servo conveying, pipeline will be transported to the site of the stack of goods.
Second, loading and unloading reaction kettle weighing automatic metering system composition and working principle
1、Batching composition
The reaction kettle measurement weighing and batching system consists of weighing module, weighing instrument, frequency converter, PLC system, etc. The measurement shares a set of control weighing and batching system, and the data is divided into two categories of weighing site equipment and main control room equipment. Among them, the weighing site consists of kettle weighing device, automatic valve, operation box and other equipment; PLC controller, industrial control computer and weighing instrumentation consists of the console of the main control room.
PLC is a digital operation system, designed for application in industrial environment. The programmable memory is used to store the instructions for performing logical operations, sequence control, timing, counting and arithmetic operations within it, and to control various types of machinery or production processes through digital and analog inputs and outputs.
PLC system's basic components: PLC basic components include the central processing unit (CPU), memory, input/output interfaces (I/O, including input interfaces).
(I / O, including input interfaces, output interfaces, external device interfaces, expansion interfaces, etc.), external device programmers and power modules, PLC internal components of the unit through the power bus, control bus, address bus and data bus connection, the external according to the actual control object configuration of the corresponding equipment and control devices constitute a PLC control system.
2、Batching principle and workflow
The workflow of automatic measuring and weighing is as follows:
First of all, the dosage is in the waiting state, at this time the discharge valve is closed, the vibrator stops, the indicator light is off. Software operators first fill in the computer interface supply unit, material name, transport cargo number and other feeding information, and will control the dosage in the starting state, start the system.
Grab or suction cup to grab the material, in the kettle is above the lower material. The material enters into the reactor through the filtering sieve, and when the material enters into the reactor completely, the weighing value of the weighing instrument is stabilized and the indicator light dazzles, notifying the operator of the grapple. The work is running, stop feeding operation. At the same time, the weighing instrument will weigh and detect the quality of the material in the reactor and accumulate it into the total amount of material.
When the above weighing process is completed, open the discharge valve to the first gear, and the material will fall through the discharge valve to the transportation pipeline, and the material will be transported away by the transportation pipeline. When the material is close to being discharged, the discharging valve will be opened completely and the vibrator will be activated to ensure that the material is completely discharged.
After completely discharging the material, the valve is closed, the vibrator stops, the indication and so on go out, return to the waiting state, at this time and allow the grapple operator to put the material to the reactor.
In the whole process, the computer software monitors the current weighing value and cumulative amount of each color mixing kettle. When the whole batch of goods transportation is completed, the computer statistics of this feeding situation, written into the database, and print the code list. The software can also form a statistical report, which is convenient for settlement and financial statistics.
The site is equipped with manual operation control box, with local and remote control functions. Local control can realize completely independent of the PLC glue tank dosage feeding and discharging requirements, while the weighing instrument can realize instantaneous and cumulative measurement. If the PLC fails, it does not affect the normal functioning of the host computer, i.e., the weighing instrument can still collect and print the normal data when metering.
Three, dosage structure and technical indicators
1、Stereoscopic three-dimensional modeling of reaction tank weighing mechanism
Weighing control system consists of conical reactor, filtering sieve, fuel tank dosing support frame, static weighing module, vibrator, electro-hydraulic actuator, displacement module, control valves and so on.
2, loading and unloading horizontal tank metering device structure design
Loading and unloading batching tank automatic measuring device package:
Set in the top of the reaction kettle guide frame, used to support the support of the silo, the support frame is made of load-bearing beams, the concentration tank with the outer side of the system has at least four ear seats, each ear seat and load-bearing beams are set up between the weighing module, the guide frame is fixed on the inner wall of the filter sieve, in the bottom of the reaction kettle is set up with a discharge valve, the two sides of the outer wall is fixedly installed for the control of the discharge valve.
External electro-hydraulic actuator
The metering kettle is inverted conical, with a three-way limiter located above the load-bearing beam on each side. Discharge valve includes two matching swinging sealing frame, each swinging sealing frame is connected with an external electro-hydraulic actuator, each swinging sealing frame has a three-phase vibration motor fixedly mounted on the outer side, and the discharge valve is equipped with travel switches at both ends. The weighing module is connected to the weighing instrument, the external electro-hydraulic actuator and the three-phase vibration motor are connected to the control system, and the weighing instrument is connected to the computer workstation. The material transportation pipeline is set below the discharge valve. The working status of the modified metering reactor is as follows.
3、Dosing structure design features
(1) Adopt eight-face top bar limit;
(2) Alloy steel weighing module adopts column load cell;
(3) The buffer device is made of special metal rubber die-casting, which has better buffer effect;
(4) Anti-warping limit device and high quality limit switch are provided;
(5) Anti-stagnation liner adopts oil-containing rare earth nylon (thickness not less than 20mm);
(6) Stainless steel weighing module with 150% overload capacity.
(7) The outside of the bucket support frame is fixedly installed with an access bar and a connected staircase for easy access and maintenance;
(8) There are two hook hoists symmetrically installed on the outside of the reactor, which are connected with chains and weighting weights to accommodate on-site calibration of the dynamic weighing module using standard weights;
(9) In the reaction kettle and load-bearing support beams between the design and installation of the gantry and standard measurement module constitutes the field testing device, can let the engineering personnel on the reaction kettle for random testing and debugging, to ensure that the system at any time in the best accuracy.
4、Main technical index
(1) Volume of reaction tank ≥5m3
(2) Maximum weighing capacity 10t
(3) Working voltage 220VAC
(4) Measuring method static measurement
(5) Calibration and display index value 2kg
(6) Comprehensive accuracy Ⅲ
(7) Overloading capacity 150%.
Fourth, the dosage structure and operation can realize the function
1、Weighing and batching structure
The weighing and batching system is composed of Siemens S7-200 series PLC control module, 7-inch, 256-color touch screen, Siemens PLC communication cable, PLC industrial control software, touch screen software and so on. The main control cabinet of the weighing and batching system of Tianna water, the data management computer adopts Advantech industrial control machine, and the computer software integrates a variety of information types, including the operation status of the field equipment, weighing data, the processing and archiving of data and other functions. Users can get the receipt information through the network database, or manually enter the material name, supply unit, goods number designation and other information to establish a material management database. After the feeding is completed, the software saves the feeding data of the time and passes the data into the central database. The software supports viewing and printing the code list in chemical-specific format, as well as counting and printing the overall information of the shipment. The communication with PLC is based on the standard OPC protocol, with comprehensive functions and reliable data, and the user can realize the control of on-site equipment through the buttons on the software. The interface of the software can be customized according to the needs of on-site control.
2、Functions realized by batching operation
(1) Two modes: automatic mode and manual mode. The automatic mode does not need human intervention, and cooperates to control the automatic operation of each equipment on the site, and records and collects the data of transportation and weighing of water slag material; the manual mode is used for overhauling and debugging.
(2) Query equipment status: the touch screen real-time display of the current operating status of each device, such as the opening or closing of the warehouse door, the rotation of the pipeline and so on.
(3) Alarm function: real-time monitoring of each field device during operation, if there is an abnormality, an alarm message will be issued on the touch screen to remind the operator to take appropriate measures.
(4) Networking function: the upper computer software and the company's financial binder weighing and batching system networking, real-time update network database, to facilitate the work of financial personnel, and save manpower and material resources to achieve paperless office.
(5) Report Printing Function: After receiving and dispatching the goods, it can print the related records of the goods, such as buyer's unit, name of the goods, name of the goods, date of dispatching, quantity of the goods, unit price and amount.
(6) database: the upper computer software has a network database, easy to record and query cargo information. At the same time can be required to establish a report, easy to view statistics.
V. Conclusion
Application of PLC technology to transform the loading and unloading kettle automatic measuring device has been put into production in the material handling of the paint company to use, stable and reliable operation of the system, safety and labor-saving, to ensure that the coating material handling production delivery, measurement of the normal order of the use of good results, but also PLC technology applied to the successful exploration of weighing and metering control. This loading and unloading system automatic metering device can be applied to phosphorus trichloride, sodium hydroxide, sodium hydroxide solution aluminum trichloride solution, chlorosulfonic acid, acetone cyanohydrin, nitric acid and other reaction tanks loading and unloading metering control, has a certain degree of popularization value.