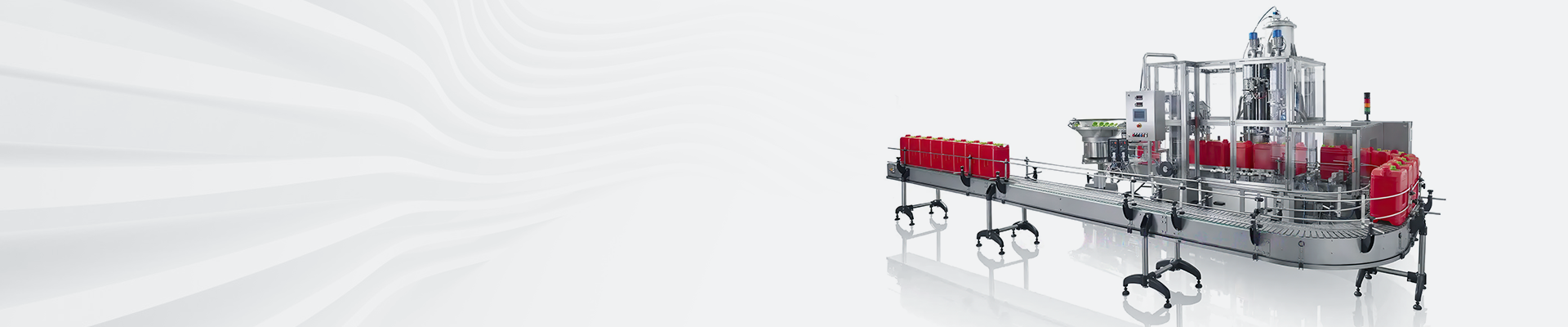
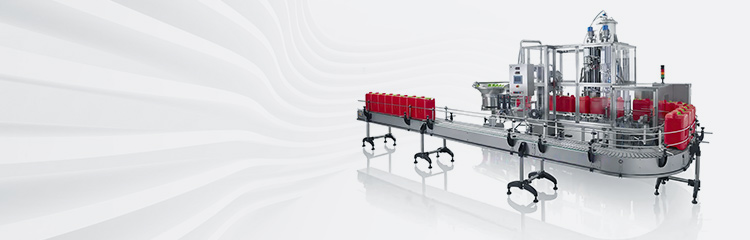

Summary:A PLC + weighing instrument realizes the structure, working principle, system characteristics and control method of the fluoride salt automatic batching control system.The control system adopts standardized, modular and systematic design, with flexible configuration, convenient configuration, system reliability and good on-site application effect.
Aluminum Corporation of China Qinghai Branch 85,000 tons of electrolytic aluminum technology reform project (hereinafter referred to as "8.5 project") in the fluoride salt dosage system of technological transformation, the use of PLC + weighing instrumentation (connected to the weighing module) + industrial computers, the successful automation of the fluoride salt dosage, the application of the effect of a good.
1 Control system overview
The composition of weighing control system is based on the existing dosage system, combined with the expansion of the new system process equipment configuration of the automatic control program. The newly expanded "8.5 project" fluoride salt batching system includes two sets of systems in the east and the middle, each set of systems has two alumina silos, four sets of fluoride salt fixed volume discharger, two sets of weighing and displaying instrumentation; control of the dosage system includes two sets of industrial controllers, one set of PLC control system, two on-site operation boxes and dosage scales of the control device. Among them, the industrial control machine is mainly to complete the formula management, historical data query. The core of the control system consists of a set of SIEMENSS7-300 series PLC, which mainly accomplishes.
1) supply and transportation control of raw materials.
2) material proportioning control of the formula; 3) communication and data exchange.
3) communication and data exchange, PLC and two industrial control machine composed of Ethernet, to facilitate the establishment of the future plant LAN and data transmission.
2 Working principle and design characteristics of batching control system
The dosage control of the dosage control system is carried out according to the formula ratio and control requirements inputted by the operator, and calculated by PLC according to the pre-set kilograms of fluoride salt dosage in batches. Firstly, set the high and low limits of alumina hopper, such as the high limit is set to 2500kg, the low limit is set to 500kg, and ton/aluminum needs to be matched with 20kg of alumina fluoride, then input: (2500-500)120=100 in the column of "formula number", the PLC will control the change of the actual measured value of fluoride salt according to the electronic weigher during the process of hopper discharging after the logic operation. After logic operation, the PLC controls the number of times and the interval time of the action of the cylinder of fluoride salt discharging according to the actual measurement value of the electronic scale in the process of discharging, i.e., for every 100kg of alumina, the fixed capacity cylinder with the capacity of 1kg will act for 1 time, and when the discharging speed of alumina is accelerated, the interval time between the action of the cylinder of fluoride salt discharging will be shortened accordingly to achieve the even dosing of fluorinated alumina. When the actual amount of material in the hopper reaches the low limit value, PLC sends a signal to the low material valve of the hopper and the fluoride salt discharging cylinder to stop discharging, and the dosage is completed, and then proceed to the next assembly process. In the remote terminal real-time display of the actual amount of alumina hopper and fluoride salt cylinder action times, industrial control machine in the CRT with text, dynamic graphics and digital display of the current actual dosage.
The control design of dosing and conveying must be combined with the actual working conditions of the cleanroom site.
The movement mechanism installed on the top and bottom of the hopper - cylinder, sealing, dust collecting device in the process of starting and stopping, if it is not necessary to carry out the necessary hardware and software processing, it will have a very big impact on the control accuracy of the dosage system. The structural form of the sensor and the structural form of the mounting accessories. Limit device of weighing hopper and anti-vibration method. Weighing change display device and PLC signal connection form and in the program BCD signal error code processing design.
Various types of valve structure in the design of the site should be combined with the characteristics of the working conditions to prevent leakage, blocking, not in place and so on. In order to prevent the inverter pollution of the power supply, instrumentation and other control power supply circuit should be added with a power filter to purify the power supply.
Improvements in the installation of the sensor, so that the hopper is not easy to produce relative displacement, to avoid the hopper random offset brought about by the many troubles and weighing and dosage of precision instability.
3 load cell signal acquisition
Load cell is actually a quality signal into a measurable electrical signal output device. Selection of load cell should first consider the working environment in which the sensor is located, which is related to whether the sensor can work properly as well as its safety and service life, and is related to the reliability and safety of the whole scale. The choice of load cell level must meet the following two conditions: ① Meet the requirements of the instrument input. Weighing instrument is the output signal of the sensor after amplification, AD conversion and other processing to display the weighing results, therefore, the output signal of the sensor must be greater than or equal to the size of the input signal required by the instrument, i.e., the output sensitivity of the sensor must be calculated to be greater than or equal to the input sensitivity required by the instrument. ② Meet the requirements of the entire electronic scale accuracy. Electronic scale is mainly composed of three parts of the scale, sensor, instrumentation, the choice of sensor accuracy should be slightly higher than the theoretical calculated value, because the theoretical calculated value is often subject to the limitations of the objective conditions, such as the scale strength, instrumentation performance, the scale's working environment and other factors, will directly affect the scale's accuracy requirements.
There are three types of load cells for electronic scales: series, parallel and hybrid. The parallel connection has the advantages of strong anti-interference ability and minimum number of power supply bridges (only 1). The reason why the parallel connection, but also take into account the clean room dosage site environmental conditions are poor, such as vibration, interference, dust and other factors
The installation of weighing module must pay attention to:①The lead cable of the sensor should wear iron pipe, and it should not be too close to the power line, it should be more than 50cm. ②)The cable must be four-core or six-core shielded cable. ③ in the same scale on the three sensors must be the same range, the force is also best to be consistent, also known as "pressure four corners", the output is consistent in order to achieve satisfactory results.
4 Upper computer software design
The industrial control configuration software IFIX launched by the U.S. Intellution is a powerful industrial automation software products. IFIX configuration software provides powerful functions required by industry, including real-time monitoring and supervisory control, alarms and alarm management, historical trends, statistical process control, user safety systems, system extensions, network functions and so on. It provides a visualization window for process processing, which enables the interface to provide graphical process information, including raw data, calculated data, variables, trend graphs, alarms, etc. IFIX's powerful graphical functions show the control point information of the dosage process in a clear way. IFIX open development interface can be embedded in the user's third-party language source program (such as C, VB and other languages), with good ease of use and flexibility to become the first choice of industrial control software for the "8.5 Project" expansion and reconstruction projects. The dosage control system can also be connected to the intranet through a switch, and can set the on-site control parameters in the control room; it can display the leakage of each scale so that the operator can take corresponding countermeasures; in the case of a long period of time without interrupting the dosage of the scale empty signal, the operator can determine the cause.
5 Conclusion
In the "8.5 project" fluoride salt dosage system technical reform project development process, the application of DDE technology to the powerful configuration software IFIX and rapid development tools VB combination, so that the recipe function to obtain very good results. Not only can more than 50 formulas be saved, but also the modification and updating of the formulas are convenient and flexible until the communication is transmitted to the PLC.