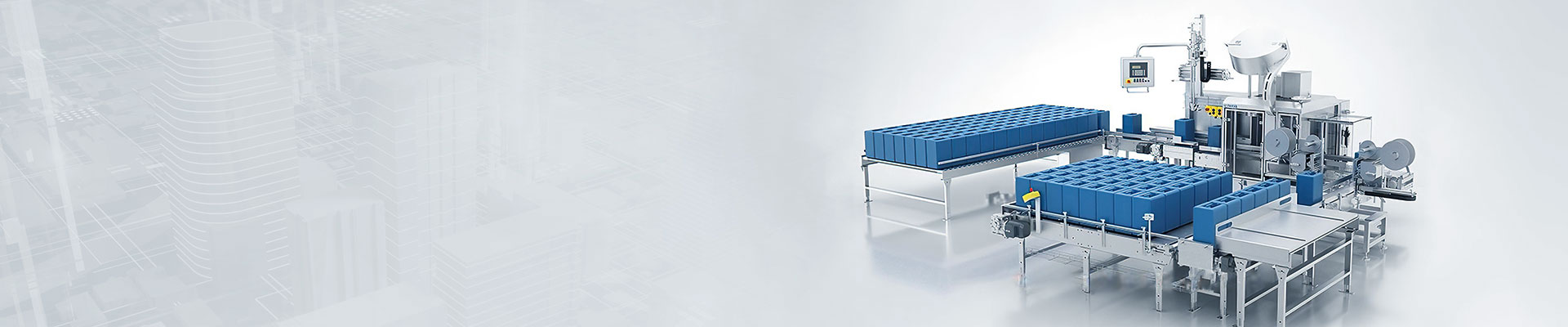
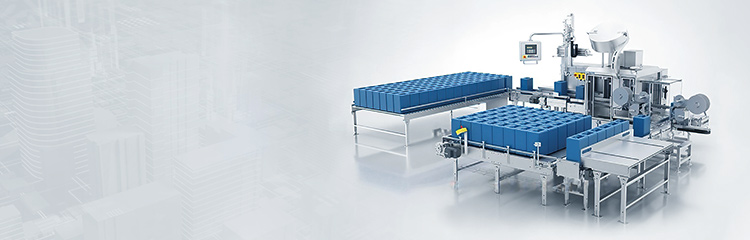
By placing one or more weighing modules at the foot of the weighing system of the reactor, the incoming weight of the system is controlled by the output signal to obtain the capacity of the tank. A weighing sensor is placed at the foot of each branch of the tank to measure the weight of the liquid in the reaction tank as measured by 3 weighing modules.

Automatic Batching system is composed of mechanical weighing frame, reaction kettle, stainless steel weighing module, weighing instrument, driving part, frequency converter, control cabinet and other main components. The formulation, feeding and discharging of the batching production line are all controlled by computer. In addition to the hopper, there are dynamic Weighing modules, precision amplifiers, A/D converters, microcomputers, monitors, printers and execution systems. The batching control system can control multiple batching scales and agitators, and can control the dry mixing and wet mixing time, can prepare several to dozens of materials, and can display the batching process and print the name of each material, quality, total quality, cycle time, formula, daily report, monthly report, etc. Computer automatic batching production line formula storage, ingredients variety, speed, high accuracy, can provide rich software, easy to modify the program, is a high degree of automation of the product. Through the weighing instrument or touch screen, the weight required by various materials is set, and the skein is automatically transported to the batching system in order to automatically weigh and control the flow, so as to achieve accurate measurement and batching.
Weighing and batching machine is a production and measuring equipment for controlling feeding, dynamic metering and continuous transportation of powdery materials. Batching refers to a balanced Weighing system for batching and measuring several substances in the said substance given mass ratio in advance. Spiral batching production line is divided into single tube single layer and double tube double layer, single tube single layer together to complete the measurement and transport, double tube double layer structure, the upper layer to complete the steady flow and transport, the base to complete the measurement and transport, the steady flow effect is better and save space.
The feeding system measures the spiral conveying material, and the computer integrator receives the weighing module signal and speed signal, which is converted into the cumulative value and instantaneous flow after processing, and the cumulative and instantaneous flow signal is transmitted to the industrial control machine (upper computer) by RS-485 port, and transmitted to the AI regulator with 4~20mA analog current signal. After the AI regulator compares the signal with the internal set value, the output 420mA analog signal is sent to the frequency converter, and then the frequency converter adjusts the speed of the screw Feeder. When the flow rate increases, the speed of the screw feeder is reduced, and conversely, the speed of the screw feeder is increased, so that the flow rate of the material and the cumulative amount of the stage are kept within the set range. Thus, reliable product quality is obtained.