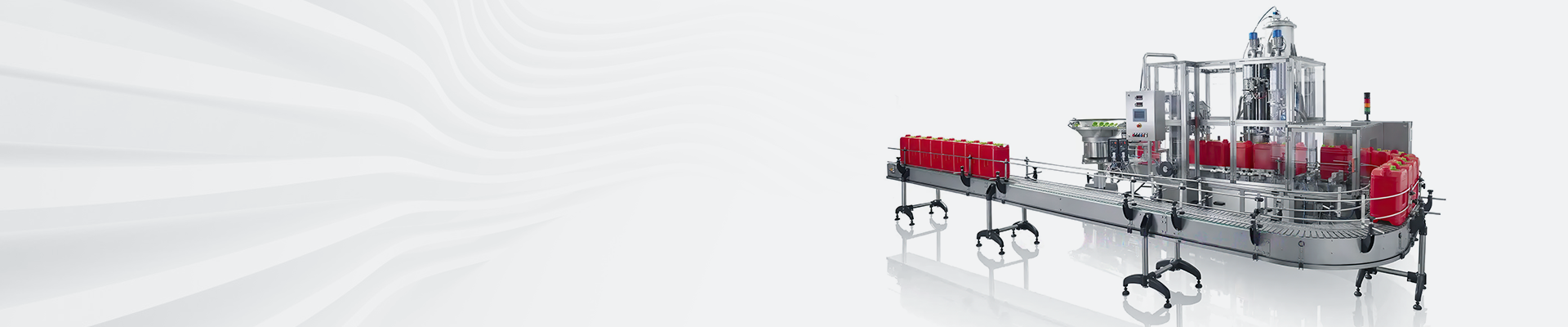
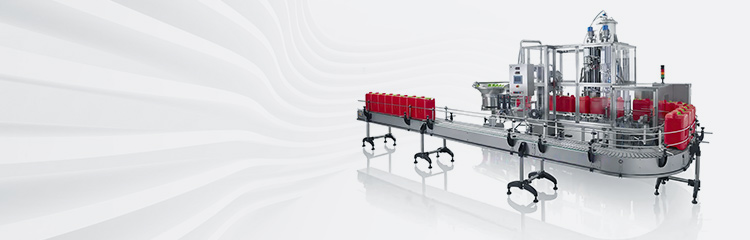

Summary:The batching system performs distributed control on the detergent production line using batch control and formula management, realizing a three-dimensional human-machine interface and realizing connection with the management network.
Detergent production line centralized dosage system discussed in this paper is a SIMATIC dosage based centralized system that we have designed and implemented in recent years mainly for high tower powder spraying process production line. The mainframe of the weighing and dosage system adopts SIMATICS7414-2DP from SIEMENS as the mainframe of the system, and PROFIBUSDP distributed I/O is used to connect the on-site I/O station with the The weighing and batching system adopts SIMATICWINCCV4 for the HMI automatic batching system. and draws the three-dimensional dynamic process flow by using 3DS and other three-dimensional graphic production tools. The weighing and batching system adopts the client/server mode, which makes the on-site weighing and batching system complete the on-site operation function, and at the same time serve as a server for the management personnel to check the on-site production status. The dosage control system in the 100,000 tons of laundry detergent expansion and renovation project has been applied, and on March 17, 1999 officially put into operation, the automatic dosage system has been running stably, high dosage accuracy, equipment interlocking protection is reasonable, by the factory's unanimous praise, the main purpose of this paper as an example to introduce the SIMATIC dosage system in the production line of detergents in the practice and application.
A system design
The high tower powder spraying production line includes the following processes.
Raw material transportation, solid dosage, liquid dosage, slurry preparation, spray drying, post-dosage, finished product metering and other processes. The automatic feeding system is set up in two control rooms, one for the central control room, responsible for monitoring the entire production line; the other for the post-dosing control room, responsible for monitoring the post-dosing part, the real-time data of the post-dosing through the PROFIBUSDP distributed I/O will be instantaneous flow rate and other data transmitted to the central control room, while accepting the central control room of the given flow rate.
The mainframe of the weighing and feeding system adopts SIMATICS7414-2DP, and ET200M is used to connect the field I/O station to the central control room through PROFIBUSDP. The electronic belt scale and flow meter control of the post batching adopts two SIMATICS7-214, and communicates with the S7414-2DP through the CP242-8 PROFIBUSDP processor template. Communication.
The weighing and dosage machine adopts Taiwan Axiomtek industrial controller with MPI card installed. The automatic dosage system adopts SIMATICWINCC configuration software, and WINCCSERVER software is installed in one of the weighing feeders to realize the connection with the automatic dosage system.
In the factory has been installed in the thick cable and other network lines, because of the central control room a weighing and dosage system also used as a server, therefore, we for its general manager (GM), deputy general manager (DGM) and other management departments have been given to stay in the network interface.
Two system functions
The main functions of the washing powder batching machine include.
Raw material conveying interlock.
As the raw material conveying adopts pneumatic conveying method, we have installed a position switch in the connecting part of the conveying pipe, so that the material conveying can be carried out only when the position switch is in place.
Solids weighing
The solid part weighing includes six kinds of materials such as zeolite, sodium pentasodium, mannite, soda ash, whitening agent and glue powder. Among them, zeolite and sodium pentasodium share a weighing hopper, manganese nitrate and soda ash share a weighing hopper, whitening agent and glue powder share a weighing hopper, material supply is realized by double-speed motor (i.e. fast and slow supply motor). The traditional weighing control is realized by weighing controller (such as PHILIPS PR1615), while in this automatic batching system, the weighing control is completed by S7414.
The principle of weighing control is as follows.
If the detected weight is greater than the fast supply value, the fast supply motor starts and the slow supply motor stops; if the detected weight is greater than the slow supply value and less than the fast supply value, the slow supply motor starts and the fast supply motor stops; if the detected weight is greater than the advance value and less than the slow supply value, the slow supply motor stops and the fast supply motor stops.
Liquid weighing
Liquid weighing includes six kinds of materials, such as caustic soda, caustic soda, water, sulfonic acid, non-ionic A and non-ionic B. Among them, caustic soda, caustic soda, non-ionic A, non-ionic B and so on. Among them, caustic soda, effervescent soda and water share one weighing hopper, sulfonic acid uses one weighing hopper, non-ionic A and non-ionic B share one weighing hopper, and the material supply is realized by pneumatic ball valve. The traditional weighing control is realized by weighing controller (such as PR1615 of PHILIPS), while in this automatic batching system, the weighing control is done by S7414.
The weighing control principle is as follows.
If the detected weight is greater than the fast supply value, the ball valve opens; if the detected weight is greater than the slow supply value and less than the fast supply value, the ball valve switches on and off at the point; if the detected weight is greater than the advance value and less than the slow supply value, the ball valve closes.
Slurry preparation
The dosing pot is divided into two pots, A and B, which can be used for single or double pot dosing alternately. The prepared slurry is sent to the high pressure pump through the filtering pot and staging pot, and then sprayed into the tower for drying. In the process of preparation, if there is any abnormal condition such as material breakage or blockage, the dosage cycle will be suspended automatically, and the cycle will be resumed automatically after recovering to normal.
The pre-dosing part (including solid weighing, liquid weighing and slurry preparation part) can be done automatically by filling in the corresponding data in the formula editing table and then starting the dosing cycle.
Spray drying
Including tail gas temperature control, settling chamber pressure control, into the tower slurry reflux control, degassing tank level control and other PID control circuit, all PID control parameters have a corresponding operation panel, you can modify the relevant parameters.
Post-dosing
After batching includes four electronic speed control belt scales for blue particles, soda ash, base powder and enzyme preparation, and two metering pumps for flavor and nonion. The total output and the proportion of each material can be set in the central control room to realize automatic quantitative feeding.
Safety interlock in automatic dosing, consider the key process to realize safety interlock, for example, after dosing, there are the following interlock control:.
Bucket elevator -> Mixer -> Transportation belt -> Belt scale and metering pump.
If the downstream equipment fails, the upstream equipment will be automatically interlocked and stopped, and sound and light alarms will be issued.
Weighing and mixing machine software using SIEMENS SIMATICSTEP7 software compilation to achieve, STEP7 software with hardware configuration, ladder programming, statement table programming, SCL high-level language programming, CFC function blocks and other programming methods. Among them, SCL high-level language programming function can realize the preparation of complex algorithms and "KnowHow" protection measures and other practical techniques, the automatic dosage function of this automatic dosage system that is the use of SCL language programming, and the use of PLC simulation function in the programmer to simulate the operation, in order to ensure the reliability of the automatic dosage system.
The weighing and dosage system is prepared by SIMATICWINCC configuration software, we divide the operation authority into different levels such as general personnel, operator, maintenance worker, processor, workshop supervisor and dosage engineer, in order to ensure the safety of automatic dosage.
As Wincc itself does not provide sound alarm function, but its embedded C compiler can call the dynamic link library function, we realized the multimedia sound alarm function by calling the sndPlaySoundA function in winmm.dll library.
As the Wincc database automatic dosage system adopts Sybase's SQLanywhere database and supports ODBC access method, through the analysis of the data structure of its running database, VisualBasic is used to realize the network query and printing of historical data records and other functions, which provides help for the management personnel to analyze the data. Since two weighing and batching systems are used, the weighing and batching systems can be redundant with each other, which improves the reliability of automatic batching.
Conclusion
Through the successful application of SIMATIC control products in washing powder production line, it opens up a new way for the centralized control of detergents. In the traditional control mode, no matter the domestic or foreign dosage system, it just adopts PLC as the interlocking control to be used, and the dosage control is still following the dosage controller, which makes it difficult to bring difficulties for management and maintenance. This automatic dosage system adopts SIEMENS new controller SIMATICS7-400, which makes the automatic dosage system have the ability to complete the complex program control and conventional interlocking control at the same time, and makes the dosage system have strong technical advantages and competitiveness, which has attracted the wide attention of the detergent manufacturers, and at the same time we are combining with the characteristics of the surfactant process and the process characteristics of liquid detergent, and continue to use SIMATICS7-400, which is the best solution for the dosage system in China. At the same time, we are continuing to use SIMATIC dosage system to develop new production process dosage by combining surfactant process characteristics and liquid detergent process characteristics.