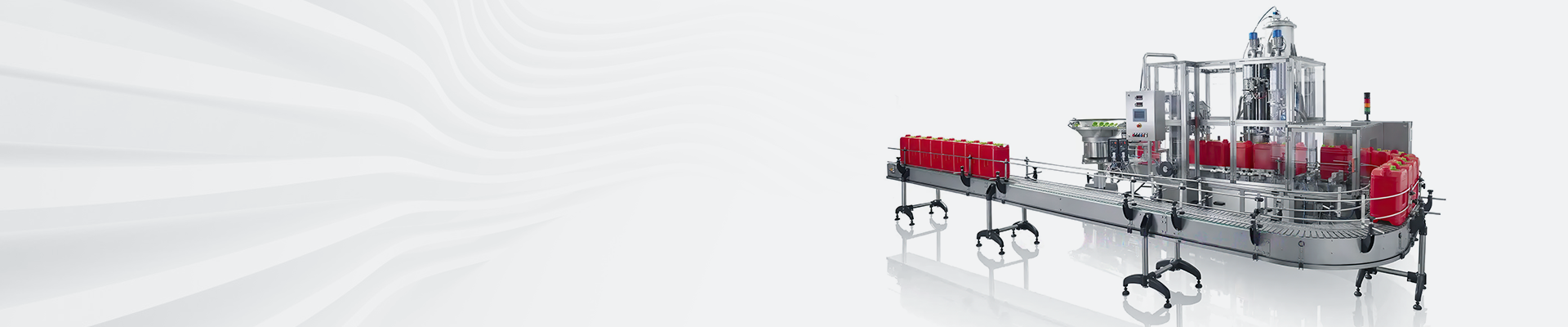
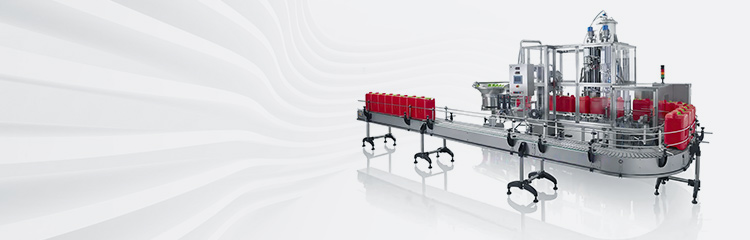

Summary:The operation, management and modification of the formula are realized through the batch batching system control center, and the formula formula and parameters are loaded into the formula program to complete the execution of a controlled formula.
BACKGROUND
With the development of the global economy and modern industry in recent years, the batch dosage system process has become an important branch of the modern industrial feeding system process, especially in the fine chemical feeding system has been widely used, with the rapid development of the fine chemical industry, there are obvious changes in the industrial structure, namely, from a large number of large-volume, less varieties of dosage way to small batches of multiple varieties of dosage way to change, and Need to adjust the product categories in a timely manner according to changes in the market. In the face of these new system changes, the original batch control has encountered some technical difficulties. First of all, the number of dozens or even hundreds of raw materials and products make the complexity of the formula greatly increased, the original batch controller can not meet the requirements of the processing capacity; Secondly, the continuous adjustment of product categories, resulting in the difficulty of the formula program modification and workload have increased. At the same time, with the continuous development of industrial automation process control theory and computer technology, for the integration of industrial control functions, standardization requirements are also increasingly high.
First, the S88 standard definition of technical terms
S88 defines a set of terms and models for describing the control requirements of manufacturers of batch batching systems, this international standard of procedural, physical and process models and terminology emphasizes excellent plant design and operational practices. Weigh batching defines more than 60 terms, including batch process, process, batch, unit, recipe, and more. A batch process is: a process in which a fixed-quality, fixed-quantity raw material is subjected to a series of processes using one or more pieces of equipment over a specified period of time to obtain a customized, quantitative product; weigh batching is different from discrete-quantity control and different from continuous-quantity control. The standard also defines four types of recipes: generic, plant, master, and control recipes, where the control recipe is implemented and executed by a batch control server to accomplish a single batch of batch batching, and the weigh batching system contains all of the information associated with a particular batch of batching and product. The definition of its weighing and feeding system terminology readers can refer to the relevant documents, and will not be recounted here.
Second, the S88 standard definition of the three models
Batch dosage standard ISAS88, defines the process model, physical model and program control model, although the three from different perspectives to describe the batch process, but the weighing and dosage systems are interrelated. The elements of the program control model are combined with the corresponding elements of the physical model to realize the relevant batching system tasks in the process model.
The process model divides the batch process into four parts: process, process phase, process operation and process action. The process action is the smallest processing activity in the batch process; the process operation is a relatively large processing activity consisting of one or several process actions, weighing dosage systems usually make the material to be processed to undergo a chemical or physical change; the process stage is composed of one or several process operations, relatively independent processing activities; the process consists of one or several process stages, and ultimately completes the batch batch dosage of a time.
The physical model is used to describe the equipment in the batch batching, and is divided into four layers: process unit, equipment unit, equipment module and control module. The control module consists of a set of sensors, excitation devices and other control modules to accomplish a basic control activity; the equipment module consists of certain control modules to accomplish a simple task; the equipment unit consists of the equipment modules and control modules to accomplish a specific task in the batching process; and the process unit consists of all the batch batching and auxiliary equipment in the batch dosage operation.
In a batch batching system, the products are processed in the order and according to the operational parameters specified in the recipe. The formulas are executed in real time by the batch actuator, and the weighing and dosing system contains all the information related to the product in a particular batch, including the raw material ratios of the product and the process information of the product dosage. A recipe consists of a title, a formula, equipment requirements, a program and additional information. Among these, the program is the most important part of the formula and according to the program control model in ISAS88, the program in a formula is divided into four levels from top to bottom: program, equipment unit program, operation and stage. Of these, stages are the most basic building blocks of the program control model, and automatic batching systems include discrete control of components, regulation loops and interlock protection. Selecting and combining phases constitutes the unit operation of a product batch dosage system within a single equipment unit. Weigh dosage defines a major processing sequence that results in chemical or physical changes in the material being processed. Further combination of unit operations constitutes the unit program.
Third, the core idea of the S88 standard
S88 to the system engineer to design the guiding principles of batch dosage, that is, the core idea of the S88 standard, that is, the recipe is separated from the equipment control program. The separation here refers to the design of the recipe and the design of the equipment control program is independent of each other. The device control program is designed as a relatively fixed module, which is referred to as the program element of the device. The combination of the recipe and the equipment control program is achieved only between the program element controlling the recipe and the program element of the equipment; there is no direct connection between the two in terms of their weighing and dosing. The two pieces of information, the program element of the recipe and the equipment requirements, ensure that the control recipe is uniquely and unambiguously associated with the program element of a particular piece of equipment.
It follows that in order to implement a batch control strategy, it is first necessary to perform a process analysis, i.e., to analyze the sequence of operations of a product batch dosage system process. When analyzing a batch dosage process, the process flow with control points is generally used to understand the controlled object, to become familiar with the dosage system process, and to study and analyze the hierarchical structure and modular attributes inherent in the batch dosage system process. The process analysis is carried out with the aim of correctly dividing the plant units according to the physical model in the ISAS 88 standard, identifying the dosage paths of the products, the interlocking protections of the individual components and equipment, and identifying the basic phases according to the program control model. After dividing the plant into equipment units and subsequently determining the final size of the system, the product dosage program is broken down into equipment unit programs on each equipment unit. An equipment unit program is a set of sequentially executed operations that occur in an individual equipment unit, which are further subdivided into stages.
Definition of the components of a batch dosage system based on the S88 standard
4.1 Definition of Phase
Phase is the smallest unit in batch dosage, usually a Phase corresponds to a sequence control program, which consists of a set of commands and parameters used to complete a basic process, and this process can be selected and called repeatedly. Charging, mixing, warming, stirring, transferring, etc. can be defined as a phase.
4.2 Division of Unit
The division of the unit has always been the key to the success of the batch dosage because of two main reasons: First, the division of the unit is determined by the process flow and process path selection, and the reasonableness of the division of the program involves the writing of the structure, effectiveness and flexibility. Secondly, most of the batch control software is now based on the unit as the billing unit, so the division of the unit will have a great deal to do with the cost control of the project. Unit is generally based on reaction tanks, tanks and other material storage, processing equipment, incidental or not incidental to its weighing and dosing component equipment, so that again, according to this principle, and then adjusted to make the unit in line with the process requirements.
4.3 Recipe preparation
The current batch control software is generally divided into two main components: one is the batch equipment editing software; the other is the batch recipe editing software. Equipment editing software is mainly a physical modeling process, which mainly includes the definition of Phase and the division of Unit described in the above two sections. And the recipe editing software is mainly the establishment of process model. The equipment editing software is closely related to the dosage system, and is usually written by the dosage system engineers. And recipe editing software work mainly involves the planning of the process, generally led by process engineers batching engineers to assist in the completion of the structure must be in line with the requirements of the S88 control model of the program, from top to bottom is divided into procedure, unitprocedure, operation and Phase, each recipe should contain these four layers of structure. In each layer of the structure can be defined in this layer of the program operation logic, after the main work for the program operation logic framework and the definition of the operation step conversion conditions.
V. Typical application case study of batch control
The following is an application of UWinBatch on a fine chemical plant with an intermittent dosage system active agent to illustrate how the DCS batch control based on ISAS88 standard realizes the batch control of formulations. This device takes more than 10 kinds of oxides and catalysts as the main raw materials, and the dosage system has nearly 40 grades of products in 8 categories, and the number of formulations is about 40 kinds.
5.1 Brief overview of the process
A brief summary of the dosing process: when the need to dosage a certain grade of product, the corresponding initiator alcohol from the middle tank area of the device to the reactor, while stirring and adding a certain amount of catalyst to generate the initiator alcohol's potassium salt. The reactor is filled with inert nitrogen and pressurized to heat the reactor. Maintaining the reaction temperature in the reactor, a mixture of oxides is continuously added to the reactor for a certain period of time (depending on the desired product). While adding the oxides, a certain reaction pressure is maintained. At the end of the reaction, the pressure in the reactor is released and the reactor is cooled at the same time. The reaction product after neutralization is cooled and exchanged by a heat exchanger and pumped out. After the products are analyzed and qualified, they are transported out of the factory through different channels, thus completing the dosing of a batch of products.
The reaction kettle as the most important process in the process of batching unit, realize the key control of the batch formula are concentrated in the reaction kettle, need to be a high degree of automation to realize the pre-set reaction steps, to the temperature, pressure and other important parameters for strict regulation and control.
5.2 Batch Control Implementation Steps
In the project implementation stage, according to the physical model specified in S88 for the design, configuration and integration, to complete the system functions. First of all, on the basis of process analysis, the equipment in the process flow related to the reactor is divided and combined. Based on the principle of balanced flexibility and simplicity, the corresponding process function groups are customized, that is, the unit operations and phases are decomposed in Unit based on the idea of sub-equipment.
After completing the definition of the physical model, the editing of the reactor unit recipe program is carried out in the recipe editor. The editor adopts a graphical user interface to make the recipe editing work simple and easy. It builds the organizational structure of the recipe program according to the process flow, calls the equipment module according to the block diagram of the recipe program, and, at the same time, establishes the recipe parameters and formulas to complete the creation of the main recipe and the library, as well as the modification.
In the dosage operation cycle, through the batch dosage control center to realize the operation, management and modification of the formula, the formula formula and parameters will be loaded into the formula program to complete a control of the execution of the formula. For example, when batching 1# grade product, the program will start the corresponding recipe of 1# grade in the main recipe library. When the program starts and runs to the stage level, the corresponding control module and equipment module will control the relevant equipment in the equipment unit in Table 1 according to the previous recipe parameters, so as to realize the batch batching of the batch, which means that the execution of the control recipe has been completed once. Functional diagram of the program corresponding to the "catalyst reaction" unit operation of the recipe program, the program through the controller in the stirring, reaction and other equipment stages of the call, to complete the specified unit operation.
In case of dosage of the weighed dosage grade, the corresponding recipe program is started in the same way, even for up to 30-40 recipes, the conversion of product batches can be easily accomplished. When a new grade of product is to be dosed, the new recipe is generated in the recipe editor by using the established master recipe program and adjusting the sequence and interrelationships of the unit operations and stages according to the requirements of the new product. This reflects the principle of ISAS88 standard that the formula is separated from the equipment, the formula as a program control is used to specify the order of operation, the creation of the formula does not need to relate to the internal logic of the equipment, there is no need to modify the formula to the physical equipment control logic for reprogramming or configuration, just change the sequence of the link between the various steps in the program function diagram or through the formula to change the formula parameters can be effectively reduce the difficulty of formula maintenance, and effectively reduce the difficulty of formula maintenance. This effectively reduces the difficulty of recipe maintenance and embodies the characteristic of batch control flexibility.
5.3 Operation effect
From the actual situation of the fine chemical plant which has been put into operation, it shows that the batching based on ISAS88 batch control software is stable and operable, which improves the product qualification rate, product quality, product replacement according to the market changes, the trial production time of new products is reduced significantly, the flexibility of the products is greatly enhanced, and improves the efficiency of the batching, which greatly reduces the labor intensity of the maintenance personnel, and facilitates the batching It has achieved good economic and social benefits and is generally welcomed by operators and managers.