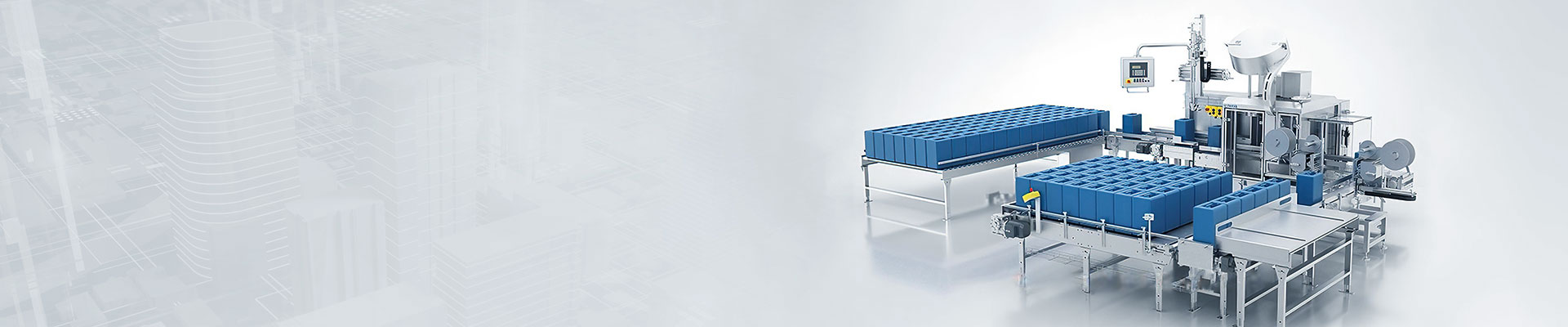
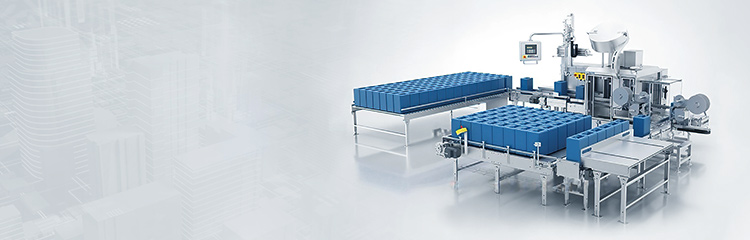
Powder dosing machine is based on many parameters such as raw material composition, auxiliary material composition, etc., and the specific production process design is calculated by combining the data needed for actual production calculation. The system software includes subsystems such as raw material composition input and ingredient calculation. The weighing system is designed and realized by using ORACLE database system and c# language, and it has been successfully applied to the batching site with the guarantee of calculation accuracy and beautiful and convenient interface.

Powder dosing machine is a device designed for weighing small doses of bulk and small single goods. According to the type of product and the required output, the corresponding quantity of weight is equipped. Weighing dosing machine is usually installed with weighing and packaging machine, and can be used for semi-automatic measurement alone. Weighing ingredients allows easy and quick conversion to another cargo and dose weight.
The automatic Batching system includes raw material storage, transportation, weighing and batching, dust removal, material mixing, packaging and filling, etc., involving many kinds of materials such as powder, granule, block, sheet and liquid; Among them, the batching system can reasonably select a variety of metering methods such as single material batching, multi-material sequential accumulation, weight reduction batching, weightless scale batching, belt scale/spiral scale, bulk scale, etc. according to industry characteristics and process requirements.
Main functions of dosing machine solution
1. Dust-free feeding in ton bag/dust-free feeding-dust-free feeding
Dust-free charging of the ton bag adopts a ton bag unpacking station, which is lifted by an electric hoist or a traveling crane and then connected with a ton bag gripper to realize dust-free sealing. Manually open the ton bag and tie the rope to start discharging, and dust-free charging is carried out for small bags of 10-20KG. The dust-free charging station is adopted, and the charging door on one side is opened, and the dust flying in the charging process is collected by negative pressure dust removal.
2. Vacuum Feeder–vacuum conveying automatic feeding.
The feeding system transports the materials fed in the previous step to the cache bin for temporary storage, and adopts negative pressure to suck the materials, which is dust-free and airtight. At the same time, it takes into account the dust removal at the feeding inlet, which plays a role in preventing dust.
3. Buffer bin temporary storage–multiple bins can be configured to realize the configuration of multiple material ingredients in the Weighing system. High and low material level bin top dust collector.
The material enters the cache bin, and the high and low material levels are configured to realize real-time alarm. Equipped with warehouse top dust collector, automatic dust removal, no waste of materials, better than the traditional dust collector.
4. Weighing and metering bin/metering screw conveyor–mettler TOLEDO metering module.
The hopper scale can be equipped with weighing module and PLC control to realize automatic weighing and batching, multi-stage variable speed control and automatic adjustment. The metering screw conveying feed is equipped with auxiliary blanking devices such as vibration, stirring and fluidizer according to the material situation. The traditional manual batching method is easy to scatter materials, the batching accuracy is poor and the efficiency is low, and the site environment is poor, which affects the corporate image. The automatic weighing batching of carbon powder designed and developed by Shanghai Youwei Electromechanical Co., Ltd. improves the working efficiency of batching technology, and the site environment is clean and tidy, and the employees are active.
Basic parameters:
Material of equipment: 304/316L/ anti-corrosion spraying/anti-sticking spraying.
Weighing accuracy: 0.2%-0.5%
Ingredients: The materials can be customized according to the working conditions.
Auxiliary devices: vibrator, stirring and fluidization to assist blanking.
Control mode: PLC+ touch screen, upper computer
Load cell: mettler TOLEDO
Batching efficiency: 100KG-5000KG/H
Weighing mode: weight loss type and weight gain type are designed according to field working conditions or process.