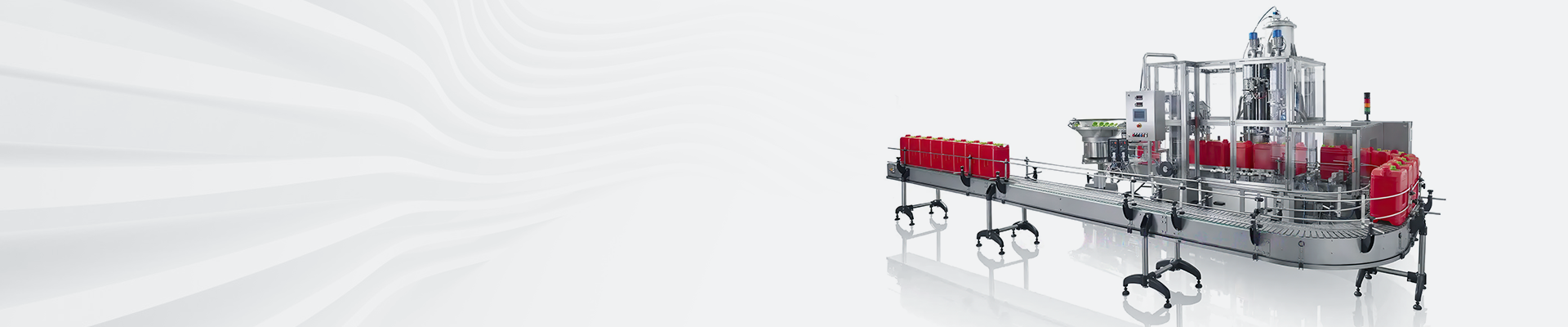
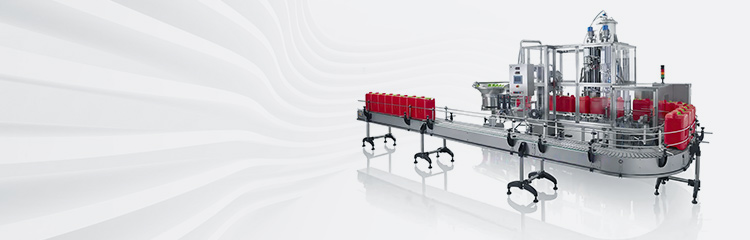

Summary:The function of the batching system is to heat the batching liquid, fine-tune the mixing ingredients, dilute, decompose, mix, control inclusions and uniform temperature to improve the quality of titanium dioxide.
1 Introduction
The reaction kettle is also known as stirring metering reaction tank dosing system its function is to dosing liquid temperature, mixing composition fine-tuning, dilution, decomposition, mixing, inclusions control and uniform temperature and other treatments in order to improve the quality of titanium dioxide, is the resin and dosage process is an important link between the production of coordination between the reaction kettle to turn the weighing and dosage machine production rhythms, etc., and is now being more and more polyester is widely used. And one of the dosage liquid into the controlled amount of titanium dioxide and mixing materials, in order to accurately control the chemical composition of the dosage liquid, the quality of polyester has a crucial role in regulating. In this paper, the reactor as the background, the reactor titanium dioxide with automatic dosing system control for a brief introduction.
2 kettle titanium dioxide dosage process briefly
Reactor titanium dioxide dosing process includes titanium dioxide dosing, dosing, discharging and feeding.
2.1 loading: titanium dioxide with or miscellaneous materials into 2m3 volume size of the bottom of the open tank, transported to the reactor by car, through the reactor crane will be titanium dioxide with or miscellaneous materials tank lifting, lifting to 10m3 titanium dioxide with high level bin.
2.2 Dosing: each tank of dosing liquid sent from the resin to the reactor, due to some differences in composition and different products polyester, so you need to add different quantities and types of mixing materials. Mixed and miscellaneous materials are weighed according to the dosage list confirmed by the operator and unloaded from the high level silo to the hopper scale through the vibrating feeder.
No.1 hopper scale completes the weighing of 1#~6# bins according to the order of the dosage list, No.2 hopper scale completes the weighing of 7#~10# bins according to the order of the dosage list, and No.3 hopper scale completes the weighing of 11#~15# bins according to the order of the dosage list.
2.3 Discharge: Discharge includes normal discharge and accidental discharge. Normal discharging is the transportation process of the prepared materials from each hopper scale to the middle hopper of the reactor. Under the normal condition of batching and production, normal discharging will start the equipment sequentially in the direction of reverse materials. Accidental discharge, is in the dosage or production abnormality, the hopper scale material to the accident hopper empty.
2.4 Feeding: Feeding is through the reactor cover mixing and dosing door on the ball valve, the middle hopper vibrating feeder control will be the middle hopper of materials transported to the reactor.
3 system design
Feeding system consists of basic automation system (L1) and secondary process computer system (L2). Basic automation system includes automatic dosage system and HMI monitoring system, to complete the field data acquisition, process loop control, parameter setting, equipment sequence control, equipment operation monitoring and alarm and other basic control functions; two-level computer to complete the design plan, design model calculations, dosage model calculations, dosage of liquid components logistics tracking and other process control functions, the two levels of dosage to complete the kettle titanium dioxide dosage control, to achieve accurate and accurate dosage. The two levels of dosage together complete the control of automatic dosage, realize accurate dosage, automatic feeding function, and control the variety and quantity of added materials in time.
The control station of automated feeder adopts S7-400 of Siemens Germany, CPU board is CPU414-2DP, and adopts Ethernet to communicate with L2 and above systems. The control station has 5 ET200 remote I/O stations, using PROFIBUS-DP interface communication. The system programming software adopts STEP7, and the software platform is based on MicrosoftWindows2000/XP operating system, which is easy to install and has a friendly interface. The monitoring software adopts WonderwareINTOUCH, which is extremely convenient for screen graphic preparation, data reading and writing, communication configuration, trend recording and alarm recording. Reasonable system layout, stable network operation and smooth communication.
The metering mixer process control computer system consists of a server, a development and maintenance terminal, an operation station and the corresponding Ethernet; the server adopts disk array technology to ensure the reliability of the system data; the server, the development and maintenance terminal and the operation station are installed in the operation room of the reaction kettle, and they are connected through the star-type Ethernet; the second-level computer communicates with the basic automation through the server; the server The secondary computer communicates with the basic automation through the server; the server realizes the data communication with the upper computer system through Ethernet.
4Control function
The control of the automatic mixer includes the control of the loading system, the control of the dosage, the control of the discharge system and the control of the feeding system.
4.1 Feeding control
(1) manual feeding, according to the operation screen of the titanium dioxide and miscellaneous materials on the screen with the low level of the bin alarm signal or by virtue of the experience of the operator regularly feeding. The use of ultrasonic material level meter through the ultrasonic echolocation detection bin mixed stock, when the material level is lower than 15%, there is an alarm display on the operating station to remind the operator to supplement the mixing in a timely manner.
(2) The feeding process should be interlocked with the dust valve of the high level silo.
(3) The name of each silo is displayed on the L2 operation screen. If there are changes in the corresponding material varieties of the silo, the actual material will be recorded on the L1 operation screen and uploaded to the L2 system, while the control table of the silo number and the name of the stored material on the L1 operation screen will be adjusted accordingly by automatic action.
4.2 Batching control
(1) The batching control is divided into machine-side manual, remote manual and automatic batching control. The switching place of machine-side and remote is set on the machine-side operation panel, and the switching point of automatic and remote manual control mode is on the screen of operation room.
(2) Machine-side manual. It is not used for production, but used for equipment debugging and maintenance, and the debugging and maintenance personnel can manually start and stop each vibrating feeder at the machine side.
3)Manual dosing
(a) On the operation screen, cut the "operation mode" to "manual" mode.
(b) The batching system is under manual control in the operation room, the operator can manually start and stop each vibrating feeder respectively; and manually switch the vibrating feeder to the weak vibration state when it is close to the end point of weighing, so as to realize the slow speed of dosage.
c) Manual dosage is used for the micro-adjustment of mixing varieties after dosage or the mixing and replenishment of hopper scale when the production requirements change. Under normal production mode, automatic dosage is adopted for dosage.
4) Automatic dosage
(a) In the operation screen, cut the "operation mode" to "automatic".
b) The batching liquid is sent to the inspection system through temperature measurement and sampling, and the composition of the batching liquid analyzed by the inspection system is transmitted to the L2 level of the process batching system through the computer, and the L2 integrates the factors of measuring polyester, temperature of the batching liquid, chemical composition, and the performance of the equipment, etc., and obtains the required quantity of mixing and the heating time through the calculation of the mathematical model. Press the "Request L2" button on the screen, the mix and miscellaneous materials to be added to the reactor will be downloaded to the basic automation system, and displayed in the set value suggestion area on the HMI screen. For the set value in the suggestion area, the operator can confirm it according to the actual experience, and can also modify the calculation results of the process computer; in case of abnormal process calculations, the process calculator must In case of abnormal process calculation, the operator must manually input the set value on the operation screen.
(e) The materials of different hopper scales can be weighed at the same time, and the material level signal of the high level bin to be discharged is not "empty".
The set weight value of each kind of material > the "fall amount" after the vibrating feeder of the corresponding high level bin stops feeding.
The cumulative weight and volume of all materials weighed by a hopper scale cannot exceed the weighing range and effective volume of the hopper scale.
If the set value is not validated, an alarm should alert the operator. After the set value is verified, the set value in the suggestion area is sent down to the acceptance area; the set value in the acceptance area cannot be modified, but can only be accepted or cleared. In the set value from the proposed area into the acceptance of the area after the transfer, and automatically reset to clear the proposed area of the set value.
(d) After the set value verification, the operator triggers the "automatic dosage start" button, dosage check "dosage" preconditions are established. At the beginning of computerized dosage, check whether the electrical system is "ready", the corresponding weighing hopper is empty, and the vibrating feeder under the corresponding hopper scale is in a state of vibration stoppage. If the check is not passed, the dosage process is stopped and there is an alarm prompting the operator; if it is normal, the button of "automatic dosage start" is invalid during the automatic dosage process and it is forbidden to modify the set value of the material; the dosage system starts the vibrating feeder of the corresponding hopper immediately and starts the automatic weighing. During the automatic dosage process, the "stop automatic dosage" button has priority. If the "stop automatic dosage" button is pressed during the automatic dosage process, the system stops immediately.
(e) different hopper scale materials can start weighing at the same time, for the same hopper scale, weighing using the cumulative weighing method, that is, a hopper scale, if there are two kinds of materials need to be weighed, must be carried out in accordance with the order of precedence, to be a kind of materials weighed, do not have to empty the hopper scale, and then immediately start the second kind of materials weighed, the weight of the cumulative.
(f) for each hopper scale, the weighing process is the hopper scale weight value (hopper scale pressure head feedback weight signal) and the target value close to the process. When the weight value and the target value of a certain amount of difference (to low-speed value), that is, from high-speed to low-speed "speed point", vibration machine in the weak vibration state operation. When the weight value and the weight of the target weight difference of a certain amount (drop), that is issued to stop the vibration signal, stop vibration machine, due to inertia continue to drop the material (drop) just so that it reaches the set value, a material weighing is complete.
(g) all the set materials are weighed in order, the computer automatic dosage process ends automatically.
4.3 Discharge control
(1) The discharging system is set up in three control modes: "automatic", "remote manual" and "machine-side manual". The switching place of "machine-side manual" and "remote" is set on the machine-side operation panel, and the switching place of "automatic" and "remote manual" is on the HMI. The switching place of "automatic" and "remote manual" is set on the HMI operation screen.
(2) Remote manual discharge. When the operation location is remote and the manual mode is selected on the HMI, the discharging system is in the remote manual control state, and the operator can manually start and stop the equipment of the discharging system.
3) Machine-side manual. Not for production, for equipment debugging and maintenance, debugging and maintenance personnel can manually start and stop the discharge system equipment at the machine.
(4) the operator to judge the actual situation of the hopper scale weighing and production, decide to choose "normal discharge" or "accidental discharge" mode on the HMI.
(5) automatic normal discharge. When the HMI selected "automatic discharge" mode; first confirm that the hopper scale weighing operations have been completed, and the intermediate hopper vibrating feeder is in the state of vibration; the operator in the HMI press the "normal discharge" button. The buttons "Normal Discharge" and "Accidental Discharge" are disabled to realize automatic normal discharge.
(a) Automatic normal discharging, according to the order of vertical screw conveyor, horizontal screw conveyor against the direction of the material in order to delay the start of the belt.
(b) After receiving the signal of screw conveyor operation, the vibrating feeder of the hopper scale with material starts to start sequentially according to the order of the number of the hopper, but the hopper scale can not be discharged at the same time.
(c) When the weight of the material in the hopper scale reduced to the "offset value", the vibrating feeder stops with a delay of 5 seconds.
(d) The last hopper scale vibrating feeder stop vibration delay of 10 seconds after the stopping of the horizontal screw conveyor.
e) Stop the vertical screw conveyor 20 seconds after the horizontal screw conveyor stops, and the normal discharging process ends.
6)Automatic accident discharge. When there is an abnormality in the production, the material needs to be discharged into the accident hopper automatically. First confirm that the weighing operation of the hopper scale has been completed, and the vibrating feeder in the middle hopper is in the state of vibration; the operator can choose "automatic discharge" on the HMI, press the "accidental discharge" button, "normal discharge" and "normal discharge" and "accidental discharge". Discharging" and "accidental discharging" button is invalidated to realize automatic accidental discharging.
(a) Automatic accidental discharging starts the equipment against the material direction in the order of opening the accidental discharging three-way valve and horizontal screw conveyor.
(b) After receiving the signal of screw conveyor operation, the vibrating feeder of the hopper scale with material starts to start sequentially according to the order of the hopper number, but the hopper scale cannot be discharged at the same time.
(c) When the weight of the material in the hopper scale reduced to "offset value", the delay of 5 seconds vibrating feeder stop.
(d) The last hopper scale vibrating feeder stop vibration delay of 10 seconds to stop the horizontal screw conveyor.
(e) After the horizontal screw conveyor stops for 3 seconds, close the accidental discharging three-way valve, and the accidental discharging process ends.
4.4 Feeding control
(1) Electrodes are only allowed to be mixed and discharged when they are in the high position.
(2) The feeding system is set up with three control modes: automatic, remote manual and machine-side manual. The switching place of machine-side and remote is set at the machine-side, and the switching point of automatic and remote manual control mode is on the HMI operation screen.
(3) Remote manual feeding. When the operation place is remote and the manual mode is selected on the HMI, the feeding system is in remote manual control state, and the operator can manually start and stop the intermediate hopper vibration machine and the feeding ball valve.
(4) Machine-side manual. Not used for production, used for equipment debugging and maintenance, debugging and maintenance personnel can be at the side of the machine, manually start and stop the feeding system equipment.
(5) Automatic feeding. At the end of normal discharging, the operator can press the "automatic feeding" button on the HMI according to the need to automatically start feeding control.
(a) Firstly, open the nitrogen seal of charging sliding pipe, and delay for 2 seconds to open the ball valve of mixing and charging above the reactor cover.
(b) After opening the mixing and dosing, start the vibrating feeder under the middle hopper with a delay of 2 seconds.
(c) After the vibrating feeder under the middle hopper is started, delay 10 seconds to stop the vibrating feeder under the middle hopper.
(d) After the vibrating feeder under the intermediate hopper stops, delay 2 seconds to close the ball valve of mixing and dosing gate of the reactor lid, then delay 2 seconds to close the nitrogen seal of dosing skid, and the automatic dosing ends.
4.5 Interlock processing
(1) When an equipment failure occurs, all the equipment in front of it (against the direction of material conveying for the front) stops immediately, and the equipment behind it should continue to run until the material is empty, to avoid the accumulation of material.
(2) The screw conveyor is equipped with deflection switch, slip detector and pull rope switch, whose signals should be interlocked with the related control equipment.
(3) The operation screen and the emergency operation desk are equipped with "emergency stop" button, which can make the equipment stop reliably to ensure the safety of the equipment in case of emergency stop during the operation.
5 Conclusion
Reactor titanium dioxide dosing system was put into operation in May 2016, the current system is running well, the automatic commissioning rate of 100%. The typical dosing cycle is 1 minute 30 seconds, and the precision is 1.5%.