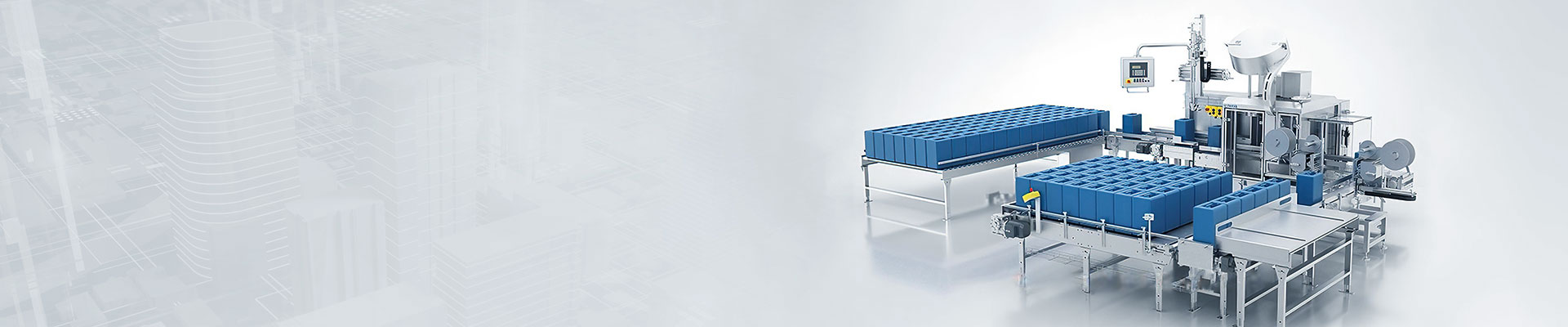
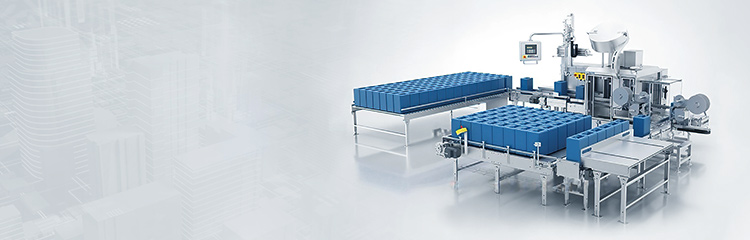
The mixing system is an on-line measurement dynamic measurement system which integrates the functions of transportation, measurement, batching and quantification. The weighed material automatically descends according to the preset formula, and the actual blanking error is automatically corrected at the next blanking. After weighing, set early mixing according to the discharging time to avoid uneven mixing in the mixing bin. 混配系统适用于定型、不定型耐火材料以及其它行业的配料自动化控制,适合于物料的连续计量和生产过程中的配料作业。使用本系统可有效提高配料精度,提升产品质量,大大降低工人劳动强度,提高工作效率,改善工作环境。基本做到配料车间微尘化、配料工作无人化,降低企业生产成本和管理强度,提升企业生产装备技术水平和产品的科技含量。 投料系统可自动根据配方要求控制移动配料称量车自动在256(可以更多)个料仓下完成多种料的计量配料,到每个排料口自动卸料,控制室内采用工控计算机及PLC系统(DCS),移动配料称量车上安装称重专用控制仪表(简称下位机)和电子秤,上、下位机之间通过通讯线连接。上位机操作使用汉字菜单和图形显示,屏幕动态显示移动配料称量车位置,动态显示配料重量,自动监测系统是否正常,整个配料线状态在工控计算机屏幕上可一目了然,系统还可记录打印各次配料结果,打印日报表、月报表,电脑最多存储1000个配方。 配料控制系统根据客户生产工艺要求采用PLC编程控制 使用组态监控系统作为人机操作控制界面,完成各种配方输入和动作命令的控制。通过人机组态监控系统和PLC程序控制对加载到称重配料车的物料进行称重、流量的控制,从而实现准确计量和配料,提高效率。 技术参数: ①微机自动控制整个生产过程;用户操作员可制定、修改、编辑生产配方; ②液晶显示器可监控设备的自动工作运行状态; ③微机可以存储多种生产配方; ④电子料斗秤采用双速加料控制方式,保证加料既快又准确; ⑤自动停车对位精度:±10mm;单料斗最大称重量:300~1500kg; ⑥内轨距、车体高度、卸料口形式见图纸(可按用户工艺修改); ⑦ 环境温度:称量车工作现场 -20℃~+50℃,微机控制室 0℃~+30℃; ⑧ 工作方式:微机自动操作,控制室半自动操作。 ⑨ 称量电子料斗秤的进料口安装了能自动升降的密封装置以及除尘系统,可以有效地解决加料和卸料过程中的粉尘飞扬问题,使生产现场环境清洁有序; ⑩ 电源功率:380V±10%,50Hz,11~37Kw,控制系统工作电源:AC 220V±10% ,50Hz,0.5Kw;

The mixing system is suitable for automatic batching control of shaped and unshaped refractories and other industries, and is suitable for continuous metering of materials and batching operation in production process. Using this system can effectively improve the batching accuracy, improve the product quality, greatly reduce the labor intensity of workers, improve work efficiency and improve the working environment. Basically make the batching workshop dust-free and the batching work unmanned, reduce the production cost and management intensity of enterprises, and improve the technical level of production equipment and the scientific and technological content of products.
The feeding system can automatically control the mobile batching weighing vehicle to automatically complete the metering and batching of various materials in 256 (or more) silos according to the formula requirements, and automatically discharge materials at each discharge port. The control room adopts industrial control computer and PLC system (DCS), and the mobile batching weighing vehicle is equipped with a special weighing control instrument (hereinafter referred to as lower computer) and an Electronic scale, and the upper and lower computers are connected through communication lines. The upper computer operates with Chinese menu and graphic display. The screen dynamically displays the position of the mobile batching weighing car and the batching weight, and automatically monitors whether the system is normal. The state of the whole batching line can be clearly seen on the industrial computer screen. The system can also record and print the batching results, print daily reports and monthly reports, and the computer can store up to 1000 recipes.
The batching control system adopts PLC programming control according to the production process requirements of customers.
The configuration monitoring system is used as the man-machine operation control interface to complete the control of various formula input and action commands. Through the man-machine configuration monitoring system and PLC program control, the materials loaded into the weighing and batching vehicle are weighed and the flow rate is controlled, so as to realize accurate metering and batching and improve efficiency.
Technical parameters:
① Microcomputer automatically controls the whole production process; Users and operators can formulate, modify and edit production formulas;
② LCD can monitor the automatic operation state of the equipment;
③ Microcomputer can store a variety of production formulas;
④ Electronic hopper scale adopts two-speed feeding control mode to ensure fast and accurate feeding;
⑤ Automatic parking alignment accuracy: 10 mm; Maximum weighing weight of single hopper: 300 ~ 1500 kg;
⑥ See the drawings for the inner gauge, car body height and discharge port form (it can be modified according to the user's process);
⑦ ambient temperature:-20℃ ~+50℃ in the work site of the weighing truck and 0℃ ~+30℃ in the microcomputer control room;
⑧ Working mode: microcomputer automatic operation, semi-automatic operation in control room.
Pet-name ruby weighing electronic hopper scale inlet is equipped with automatic lifting sealing device and dust removal system, which can effectively solve the problem of dust flying in the process of feeding and discharging, and make the production site environment clean and orderly;
Attending power supply: 380 V 10%, 50Hz, 11 ~ 37 kW; working power supply of control system: AC 220 V 10%, 50Hz, 0.5Kw;;