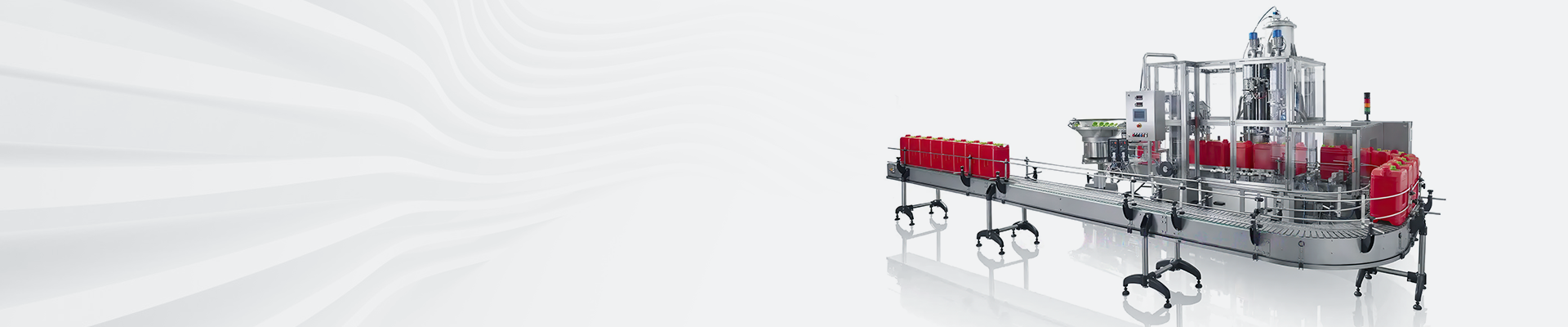
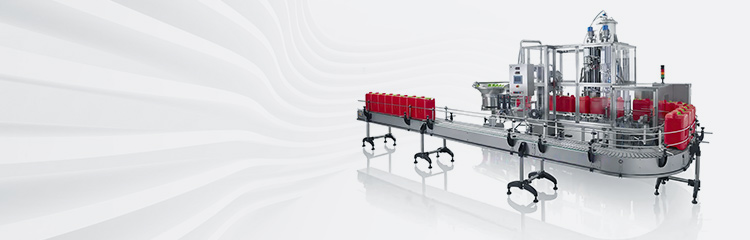

Summary:The batching system selects and weighs the raw materials according to the set formula and puts them into the finished product mixer. It collects the information of the finished product and sends it to the central control unit. The central control unit stores the set formula, raw material information and finished product information together in the memory.
I. Design conditions, equipment composition and technical requirements
1.1 Design technical requirements
1.1.1 Batching process:
Reactor weighing production of products for low microcarbon ferrochrome, the process flow is: the production of silicon chrome alloy iron (ladle) and mineral powder, white ash (material bell or hopper containing) through the batching measurement, through the overhead crane 20t transported to the shaking package for wave wheel method reaction, to produce the required products.
1.1.2 Realize the function of reducing dosage and realize the arithmetic function of the above table.
1.2 Equipment composition
1.1.1 There are three storage tanks, storage tanks were installed at the mouth of the drum conveyor belt conveyor, easy to discharge the material to the main conveyor belt, the material is transported to the smelting kettle, three weighing storage tanks out of the conveyor belt as well as the main belt conveyor are configured with 2.2KW frequency converter manually adjust the speed of the operation, adapt to the different material conveying speed, to meet the user's process requirements.
1.1.2 The three storage tanks are installed with FW metering module for material metering, which is connected to the weighing instrument for real-time measurement of material weighing weight after balancing the signals through the junction box, and the three weighing instruments communicate with the PLC serial port in the control cabinet, and the touch screen is adopted as the human-computer interface, and all the batching parameters and the batching weights are measured by the touch screen.
The touch screen is used as the human-machine interface, all the dosage parameters as well as the dosage process status, the actual dosage data report and so on are displayed and set on the touch screen, the whole Chinese interface is intuitive and easy to understand.
1.1.3 The three storage tanks adopt the method of decreasing the amount of material, the user only needs to set the amount of material needed each time on the touch screen, the automatic dosage system automatically calculates and controls the operation of the material belt conveyor, maximizing the control of the material metering accuracy.
1.1.4 There are two operation modes: automatic and manual, which can be switched flexibly to meet the requirements of different production processes.
1.2 Parameters and public works parameters
No.1 storage tank: install 3 FW-2T weighing modules, and install a set of 0.75KW motorized pulley belt conveyor at the outlet of the storage tank.
No.2 storage tank: install 3 FW-2T weighing modules, and install a 0.75KW motorized pulley belt conveyor at the discharge port of the storage tank.
No. 3 storage tank: 3 FW-2T weighing modules are installed, and a set of 0.75KW motorized pulley belt conveyor is installed at the discharge port of the storage tank.
The main belt conveyor for material conveying is divided into two sections, and a 2.2KW motor drive is installed respectively.
Temperature range: -10℃~+45℃.
Relative humidity: <95% (non-condensing).
Power supply: 380V, 50HZ, 15KW
1.3 Weighing weight 20 tons.
1.3 Main components of batching:
Carbon steel spraying control cabinet (double-layer sealing structure, tempered glass outer door, inner door installing weighing instrument, touch screen, frequency converter operation panel, outer door installing operation buttons, signal indicator lamps)
The electrical control cabinet of batching control system installs all the electrical control components, mainly including three weighing control instruments, touch screen, five inverters, PLC, serial communication module, isolation transformer, power filter, switching power supply, circuit breaker, contactor, small relay and other low-voltage electrical components, installing auxiliary parts, terminal blocks and so on.
The whole set of electrical rely on the company's independent design and preparation of the software control program, the user set to adjust the necessary production parameters, can realize the automatic operation of the dosage, improve production efficiency, reduce the intensity of manual operation.
1.4 Main functional characteristics of batching
The storage tank is equipped with FW weighing module, which is stable and reliable, with reasonable structure, suitable for continuous and long-term measurement of weighing and batching.
Touch screen setting to monitor the production data flow, full Chinese interface, intuitive and easy to understand.
Adopting frequency converter to adjust the running speed of belt conveyor steplessly, adapting to different batching process requirements.
The weighing instrument communicates with PLC in real time, after sampling the weighing data, PLC automatically calculates and automatically controls the amount of material discharged from each weighing tank, maximizing the accuracy of measurement and preventing human error.
The actual data of batching are automatically saved in the data report, which is convenient for users to inquire.
The control cabinet adopts double-layer sealing structure, and the overall protection level is IP54, which is suitable for long-term use in the harsh environment.
1.5 Dosing operation process
1.5.1 Set the corresponding dosage parameters on the touch screen, set the frequency converter operation frequency by the speed knob on the operation panel of the frequency converter, and select the type of dosage on the touch screen.
1.5.2 Press the "dosage start" button, first start the main belt conveyor, delay a few seconds (touch screen can be set), the corresponding dosage storage tank discharge belt conveyor also start running, the material in the storage tank gradually to the main belt conveyor to transport out, when the corresponding weighing tank discharge weight reaches the touch screen settings When the discharge weight of the corresponding weighing storage tank reaches the target value set by the touch panel - advance amount, the corresponding weighing storage tank discharge belt conveyor will stop running and the discharge will be finished, and when the discharge of all storage tanks is finished, it means that a dosage working cycle is finished.
1.5.3. In the process of dosage, according to the actual speed of material conveying, the frequency converter of storage tank belt conveyor and the frequency converter of main belt conveyor can be adjusted manually to change the conveying speed.
1.5.4 At the end of a dosage cycle, the actual dosage weight of each kind of material is automatically saved to the touch screen data report, which is convenient for users to inquire.
1.5.5. Press the "dosage stop" button to interrupt the current dosage process and reset the program to the initial step.
1.5.6. In order to increase the flexibility of the system, as well as the convenience of system debugging, the automatic dosage system is designed in manual mode, the main belt conveyor, the belt conveyor of the three storage tanks can be started and stopped independently.
1.5.7 When the weight of the material in the storage tank is less than the target value set for each discharge, the automatic dosage start will be prohibited, and the touch screen alarm will prompt the operator to pay attention to the need for manual reset and restart only after the storage tank is full of material.