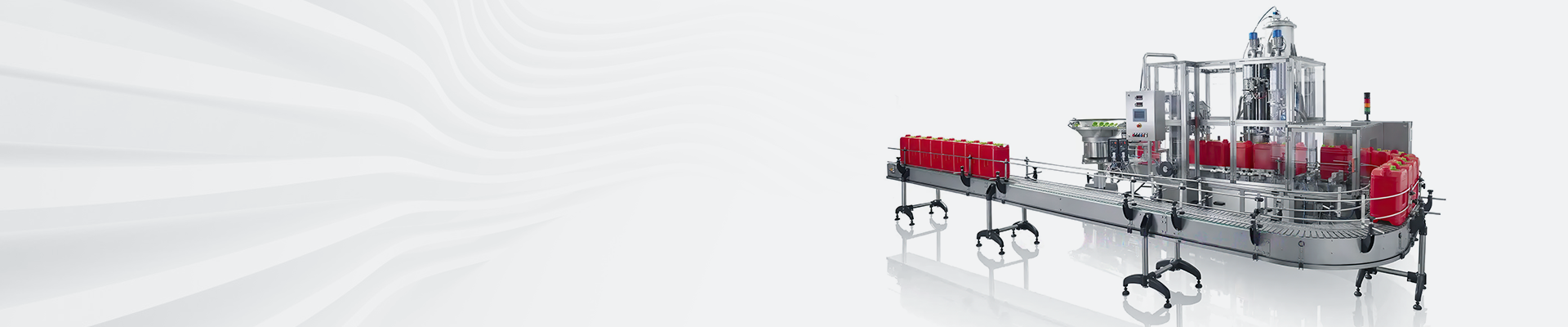
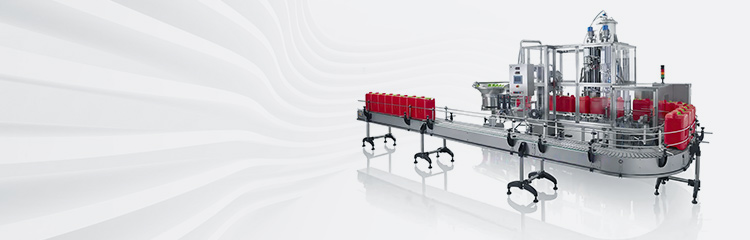

Summary:The automatic batching system realizes automatic and manual control of the main belt, screw conveyor, alarm and analog input and output, and realizes chain start and stop.The speed of the motor can be directly controlled to achieve uniform batching of materials.
Feeding system is with the high degree of automation of modern industrial production and process control of the increasing complexity of the development of the integration and automatic control technology, computer technology and communication technology as a whole, with advanced technology, complete functionality, flexible application, reliable operation and other advantages, and with the increase in the degree of measurement instrumentation intelligence, so that the control of a more flexible, more powerful. It is the ideal control system for the production process of the enterprise.
Collective-distributed feeding system can form intelligent and programmed production management to achieve and improve the accuracy of dosing. Strong on-site anti-interference ability, no signal attenuation, high degree of automation, decentralized risk; simple troubleshooting and easy maintenance.
Main Technical Parameters
Material name: powder material
Material bulk density: 800kg/m3
Maximum feeding granularity: ≤3mm
Moisture of material: 10%-14
Dosing type: 8 kinds
Maximum feeding capacity of single unit: 250KG
Minimum feeding quantity of single unit:8-25KG
B eight quantitative batching; 1 # measuring volume designed for 3m3
2#3#4# volume design for 2m3
5 # 6 # 7 # 8 # volume designed for 1m3
9# volume design for 3m3 (spare)
10# volume design for 2m3 (spare)
Material particle size: <3㎜, moisture: <14%;
C. Composition and working principle of batching
The batching machine consists of a set of industrial PC management system, a set of PLC electrical control system, and N sets of single-loop closed-loop control circuits; each closed-loop control circuit consists of screw conveyor, automatic batching system (including weighing control display, weighing sensor, etc.), frequency converter and field control box. And leave the communication interface with the upper computer.
The material is conveyed into the hopper scale. The weight signal is sent to the weighing instrument. The weighing instrument will load the weight signal through arithmetic and processing to arrive at the weight of the material, which is displayed on the weight indicator respectively.
The configuration of the instrument is a high performance intelligent weighing instrument, the instrument and frequency converter speed control screw conveyor speed to form a closed loop control. The built-in intelligent software regulator of the weighing instrument can set high, medium and low feeding levels to ensure the accuracy of the dosage. The output of three sets of signals is used to control the frequency converter, which in turn controls the feeding speed of the screw feeder, so as to achieve the purpose of accurate dosage. Intelligent weighing instrument can set the feeding quantity manually, or set the proportion through the two-way communication between computer and instrument.
The industrial computer communicates with the PLC through the serial port. According to the actual process of dosage process, the ICC can reflect the operation status of feeding, dosage, delivery and related equipment in the form of dynamic screen. When there is over-limit failure during operation, there will be Chinese character alarm prompts and alarms (sound and light) will be activated to alarm, or shutdown, or change the warehouse, and the control status analysis can be made according to the operation data, and the dynamic dosage process of the system will be reflected in bar charts with different colors. According to the operation data, the industrial control machine can give the ratio or feeding quantity, and truly reflect the dosage status. In addition, the ICC is installed with the system developed by YUKE. It also has other functions, such as shift report, daily report, monthly report, yearly report and so on. It is convenient for management.
Fourth, each part of the performance characteristics
1、Weighing and batching system
The mixer uses the reduced weighing instrument. Below the use of spiral feeding, both sides are designed with poke holes to ensure that the material can be blocked in time to solve the problem of blocking. In order to ensure the effectiveness and accuracy of dosage adjustment, the frequency converter regulates the speed of screw feeder.
2、Downloading system
Conveying system includes driving device, screw conveyor, gate and so on.
a. Conveying device: Reasonable selection according to the size of the amount of transported materials, to ensure that the motor has high efficiency and high life expectancy. Installed in straight line with output shaft, occupies little space. Head drive, motor and reducer are integrated.
b. The sealing of the shaft and bearing of the conveyor adopts labyrinth sealing, and the bearing life is more than 50,000 hours.
c.The inlet and outlet are easy to dismantle to ensure that no material is spilled during operation.
3.Measuring system:
Choose YUKE YKLP-60 series batching machine. Designed according to the weight, fluidity, physical properties and other parameters of the material, the hopper, frame, weighing module, weighing instrument and junction box and other components.
a. Weighing hopper
3 weighing modules, system checking accuracy 0.3%, running accuracy 0.5%.
4mm manganese plate welding, strong rigidity, weighing stability.
The weighing instrument is easy to operate and low maintenance;
It has the function of hanging code and physical calibration.
b. Load cell
Adopting HBM pressure cantilever beam measuring module, the accuracy is better than 0.3‰, the specific parameters are as follows:
Repeatability: less than 0.01% of rated output
Sensitivity temperature drift (10℃): less than 0.015% of rated output.
Zero temperature drift: less than 0.026% of rated output
Excitation voltage: 10VDC supplied by the accumulator
Safe overload: 150%
Protection level: IP68 after oil immersion
d.Intelligent weighing instrument
4、Electronic control system
a. Batching mode
Full-automatic control mode: the industrial control machine automatically controls the starting and stopping of the equipment and the changing of the warehouse through the communication with PLC controller, and sets the feeding quantity through the communication with the weighing instrument; after starting the dosing system, each automatic dosing system in the system will start and stop the screw conveyor and regulate the quantity of the material through the PLC outputting the control signals to the frequency converter to start and stop the screw conveyor and regulate the quantity of the material, and the PLC will output the secondary control signals to the frequency converter to regulate the rotating speed of the spiral feeder when the quantity of the material is close to the set value. PLC will output the secondary control signal to the frequency converter to adjust the speed of the screw feeder to ensure the accurate dosage (each batch of dosage can be divided into high, medium and low feeding). Each batch is composed of a multi-material dosage through the industrial control computer, and each batch can be dosed according to the weight (or ratio) specified in the recipe list selected on the computer;
Semi-automatic dosage control: in case of malfunctioning of the industrial control unit, it is possible to choose the start-stop of the equipment by means of buttons on the operating table. The instrument manually sets the dosage amount, which can ideally reach the proportion, and the two control methods perfectly realize the purpose of dosage control.
b. Operation procedure
The PC starts the dosage program, calls the dosage program or re-inputs all kinds of material dosage parameters from the keyboard, the button starts the PLC programmable controller to control each terminal equipment: the following screw conveyor starts sequentially, the computer completes all kinds of data processing and control.
System through the PLC and electronic control equipment to realize the sequence of start, stop operation is as follows:
The final equipment of the system starts, against the direction of material transportation to start sequentially, to ensure that the head of the material is aligned;
When stopping, first stop the feeding equipment, and then from the beginning of the production system equipment, along the direction of material transportation, in order to ensure that the end of the material is aligned.
When an accident occurs in a device, its back (the direction of material transport for the front) of all equipment immediately stop running, while it is still in front of the equipment continues to run until the receipt of the fault release signal, so as not to affect the next start.
In case of emergency, it can be unlocked or stopped on the spot.
c. Control box/cabinet setting
The power supply cabinet, frequency conversion cabinet and instrumentation console are placed in the batching control room, and a field operation box is placed next to each automatic batching system for debugging and use in case of failure;
The electrical components adopt domestic and foreign famous brand products, and the power cable interface and signal cable are set separately to meet NEMA standard;
All switch contacts should be passive contacts, contact capacity of not less than 3A, 220VAC; all input and output current signals are standard 4-20mA;
The strong power circuit, strong power control circuit and weak power signal circuit of the control cabinet are arranged separately to prevent the strong power circuit from interfering with the weak power signal circuit, which is conducive to the operation and safety maintenance requirements;
1 operation desk, place industrial control PC, weighing instrument and other components, in the operation desk can choose field / local / computer three kinds of control mode, local single machine start / stop, fault alarm indication, and so on;
A: On-site control, when on-site control is selected, manual start/stop of the equipment can be realized by the on-site machine side box.
B: on-site control, when selecting on-site control, the equipment can be started/stopped manually by the operation desk in the control room, the amount of feed can be set manually, and the inverter can be controlled by PLC to reach the ideal target value.
C: computer control, by the computer directly with the PLC and PID communication to realize automatic control.
One inverter cabinet, inverter cabinet installs 10 sets of inverter and electric control components. The inverter control panel displays current parameters and can also be set to frequency, voltage, or speed parameters;
The weight indicator operator console is combined into one to set PLC, and PID,, UPS and intermediate relays, knobs, buttons, indicators and other low-voltage electrical components.
Field box 10, set the machine side / centralized switching switches, a variety of condition indicators, and inverter frequency display, etc..
d. Programmable controller (PLC)
Programmable controller (PLC) adopts Siemens S7-200 series products, mainly to complete the coordination between the equipment, start-stop interlock and other functions.
S7-200 series PLC adapted to a variety of occasions in the detection, monitoring and control of automation. With powerful functions, whether in independent operation or connected to a network can realize complex control functions. Detailed features are listed below:
High reliability
Rich instruction set
Easy to master
Convenient operation
Rich built-in integrated functions
Real-time features
Powerful communication capability
Rich expansion module
PLC controller realizes the main belt, screw conveyor, alarm and analog input/output to realize automatic and manual control of the system and chain start/stop. If you choose to chain with the main belt, PLC accepts the main belt start signal, the automatic dosage system screw conveyor start, a dosage process end or the main belt for some reason stop, all the screw feeder stop and then all the equipment stop.
e. Frequency conversion controller:
Choose Swiss ABB510 series products, the frequency converter is a new type of intelligent motor speed controller based on microprocessor, which can directly control the speed of motor, with low noise, large adjustment range, high adjustment quality, torque vector control, large starting torque, self-adjustment and other characteristics. Its basic features are as follows:
Automatic/manual speed control function
Automatic/manual non-disturbance switching function
Various protection (over/under voltage, overload, overcurrent, overheat, short circuit, etc.) functions
Automatic fault diagnosis function
Alarm indication and alarm output function
Human-machine screen interface function
Torque feedback (analog and digital) function
Speed feedback (analog and digital) function
Input/output control function
Power failure data retention function
Frequency, current, voltage and other parameters are displayed on the frequency converter cabinet and the operation desk box respectively.
5、Batching management system
a. Industrial control computer
IPC610 series industrial control computer produced by Taiwan Advantech Company is chosen to fulfill the functions of data management, system monitoring and report output.
Unique structure, specially designed for harsh environment;
Resistant to high/low temperature, vibration, electromagnetism, interference, humidity, dust, salt spray, etc;
Average trouble-free time for continuous operation is more than 50,000 hours;
Dedicated power supply UPS with input and output isolation;
The system is easy to upgrade and modernize;
The main configuration is as follows: P41.8 CPU; memory 1G; hard disk 150G; 52X optical drive, HP1007 printer, Samsung 22-inch LCD display
PCI-1602 communication card, and PLC communication