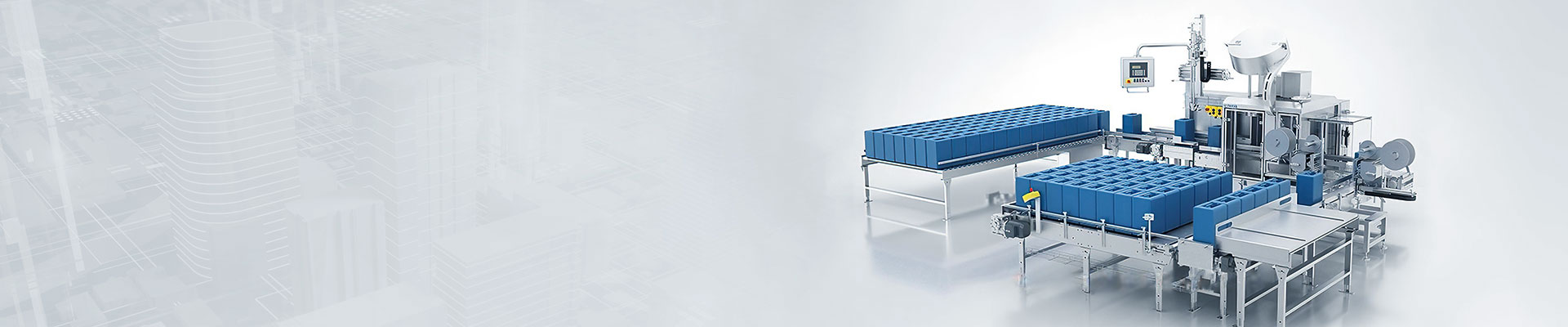
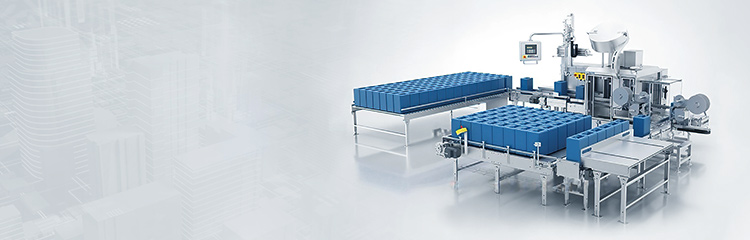
The automatic feeding system accomplishes the tasks of parameter control, sequence control, position control, speed control, tape control, temperature and shape control. It mainly accomplishes the tasks of initial data input, material tracking, process parameter setting calculation, data recording and reporting, man-machine dialogue processing, data communication, simulation modeling, historical data processing, application system startup, event monitoring, etc. The process control automation level computer system reserves the communication interface with continuous casting and computer system.

Automatic Feeding machine system is a kind of production equipment used in industry for different powder or liquid main materials and auxiliary materials in a certain proportion of automatic and accurate formula, usually by the Weighing system, weighing module, weighing control instrument, PLC system and the upper computer and other components. Automatic feeding system includes raw material storage body, conveying body, weighing and dosing body, dust removal body, material mixing body and other equipment; dosing mode, according to the characteristics of the industry, production process requirements, feeding machine specific material characteristics, a reasonable choice of "zero method" or "reduction method" and other weighing methods, feeding machine with a single hopper single material, single hopper multi-materials, multi-bucket multi-materials and other modes of operation. The smaller surge hopper on the loss of weight bulk output bulk bag discharger provides sufficient capacity to allow the main ingredient to be transferred at a lower rate and reloaded by the small diameter flexible screw conveyor. Also conveyed by the weight loss flexible screw conveyor is the secondary ingredient, which is manually dumped at either one or two dumping stations equipped with a vacuum filtration system containing airborne dust. All flexible screw conveyors discharge into a common shoulder weight transition hopper mounted on a load cell, which confirms the accuracy of a batch of fed material prior to passing it through a rotating airlock into the pneumatic line described above.
The automatic feeding system consists of industrial control machine, PLC, industrial weighing instrument, frequency converter, vibration motor, mixer, sensor, conveyor belt and other parts. The upper industrial computer provides human-computer interaction interface to complete the control information input, data management, data display, storage, statistics and reports and other functions. It accomplishes the tasks of parameter control, sequence control, position control, speed control, belt material control, temperature and shape control. It mainly accomplishes the tasks of initial data input, material tracking, process parameter setting calculation, data recording and reporting, man-machine dialogue processing, data communication, simulation modeling, historical data processing, application system startup, and event monitoring. The process control automation level computer system reserves the communication interface with continuous casting and computer system.
Product Features:
Data processing: the Dosage system can automatically calculate and process the collected signals, so as to automatically control the normal operation of the equipment.
Communication function: bi-directional data communication between computer and PLC and meter.
Monitoring function: detects and monitors the instantaneous flow rate, daily totalization, monthly totalization, yearly totalization and other parameters of the dosage process.
Screen display: the computer monitor or the weighing instrument can display the operating status of the control parameters during the dosage process.
Print management: dosage reports can be printed at any time for saving and querying (user selectable).
Alarm function: the computer to screen and sound and light signals to the various parameters over the limit or equipment state abnormal alarm. PLC in the conveyor equipment, weighing process for real-time control at the same time, complete the system failure detection, display and alarm.
The system can adopt various working modes such as single hopper single material, single hopper multiple material.
Dosing method: screw dosing, vibration dosing, belt dosing.