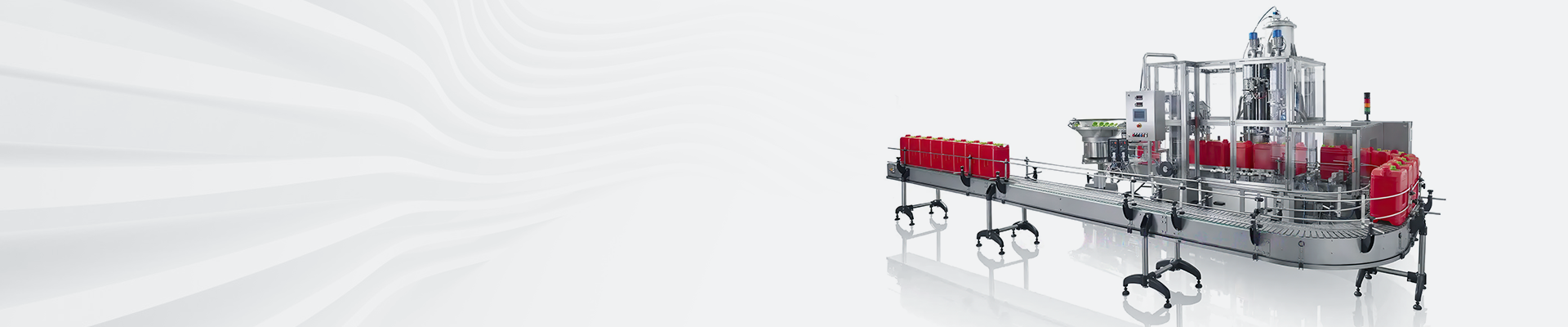
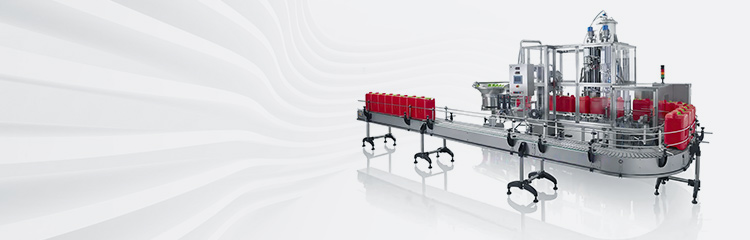

Summary:The batching system is composed of Schneider's PLC, which respectively completes the control of speed, temperature, pressure, tension and logic in batching.Communicate with the host computer to complete data exchange.
Composition and function of dosing hardware
Upper computer part
The upper computer is composed of six computers respectively, one server PC, one engineer PC and four workstation PCs. The engineer PC and the main workstation PC are equipped with dual-port ModbusPlusPCI communication adapters, which form a redundant ModbusPlus network with each PLC to accomplish data collection and operation control of each part of the dosage system. The feeding system utilizes a redundant network design to improve the safety and stability of the dosage.
The functions of each computer are as follows:
In general, the master workstation is responsible for exchanging data with the PLC, and the other three workstations call up screens and data to the master workstation via industrial Ethernet (TCP/IP). When the main workstation fails, it can be immediately switched to the engineer PC, which will control the operation of the dosage to ensure that the dosage can run smoothly.
The main function of Engineer PC is to design and change the program, including the configuration of the upper computer screen and PLC program, and at the same time, it can also be used as the main workstation. In short, the Engineer PC is the most complete and important core computer.
The function of server PC is to backup all the control programs; save the historical data about temperature, pressure, tension, speed, etc. in the dosage system (the data can be saved for two years); save the alarm record of the dosage system and the process formula of the dosage system.
2PLC part
The whole feeding system is composed of PLC from Schneider, which can control the speed, temperature, pressure, tension and logic of the dosage. Communication with the host computer to complete the exchange of data. At the same time, for the purpose of I/O expansion during the retrofitting process, each PLC is equipped with a RIO network, a Modbusplus network and an Interbus network according to the actual needs.
Here is a brief introduction to the main network ModbusPlus and redundant network design: (1): ModbusPlus network is a high-speed peer-to-peer communication network, the data sharing between the nodes of the network is very simple. ModbusPlus network supports up to 32 peer-to-peer nodes, and its communication distance can be up to 450 m. (2): The design of the redundant network: the network in the high-reliability The redundant line cable is used to realize the ModbusPlus communication in two independent cable systems, and the reliability of the cable is checked and verified every time the information transmission is carried out. If one of the cables fails, the system automatically switches to the other cable. The cable that has failed is identified in the network statistics, and if the cable fails, the network will continue to work with the second cable until that cable is repaired.
The control functions of each PLC in dosing are as follows:
PLC1 - Controls the transportation of the raw material and the proportioning of the principles, as well as heating and drying the raw material;
PLC2 - is responsible for the temperature of the extruder and the control of the drive system;
PLC3 - temperature and drive system control for longitudinal and transverse drawing;
PLC4 - responsible for the drive control of the haul-off and winding section.
Application of control software
Monitorpro software
Monitorprov6.5 from Schneider is used as the software platform for program development in the configuration of the human-machine interface. The development version of the software is installed in the engineer's PC for designing and modifying the screen, only the running version of the software is installed in the PC of the main workstation, and the WebClient software is installed in the other three workstations to call the screen of the main workstation through the TCP/IP network. and stability. In the interface, it is designed with real-time production process monitoring function, equipment switching control function, automatic alarm detection, recording and display function, automatic fault diagnosis function, real-time and historical trend graph display function, and various report statistics and printing function.
Concept Software
The programming software for the PLC is ConceptV2.2XLSR2. The Concept software editor supports five IEC programming languages: Function Block Diagram (FBD); Ladder Diagram (LD); Sequential Function Chart (SFC); Instruction List (IL); and Structured Text (ST).
Two languages, FBD and LD, are used for programming this control system. In the FBD language, variables within the FBD can be merged with basic functions, elementary function blocks (EFBs) derived function blocks (three FFB types) through the IEC 61131-3 function block diagramming language.Concept provides a variety of function block libraries with predefined EFBs for FBD programming. In these libraries, EFBs are grouped according to the type of application to make them easier for the user to find. In the FBD editor, the user can display, modify and load initial values, as well as display current values.
Summary
The weighing and feeding system is running normally after more than two months of installation and commissioning. This dosage system realizes the monitoring automation and intelligence, and has the advantages of safety, reliability, speed, convenience and strong expandability, reflecting and realizing the powerful function of Schneider's control technology. Up to now, the whole control system has been running stably and reliably, and the performance indexes have reached the process requirements.