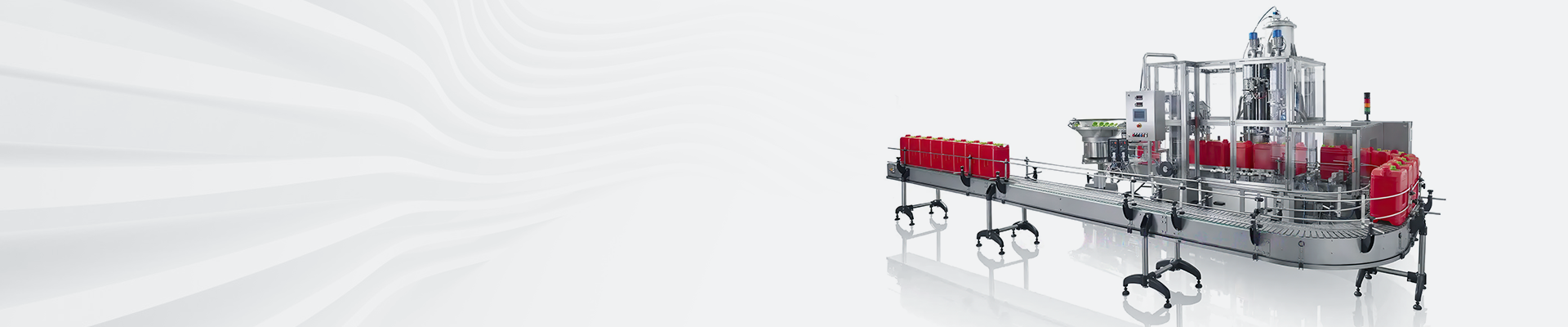
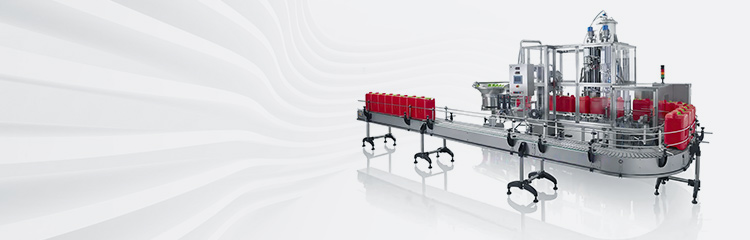

Summary:In the processing and application of plastic films, weight-increasing and weight-loss automatic batching systems each have their own advantages, and film manufacturers can choose according to their own needs.
The automatic feeding system and the weighing hopper for multilayer co-extrusion control are the most central parts of the whole processing application system, while the in-line automatic recycling equipment is the best complement to the system. At a time of high raw material prices, in-line recycling is particularly important to avoid wastage of raw materials and secondary contamination from edge material recycling.
ABB Dosing Advantages
In order to meet the functional requirements of the film, the addition of various additives has become a must in today's plastic film production. In most cases, additives are added in the form of masterbatches or pre-mixed specialties for granulation. Pellets have good plasticizing properties and are relatively easy to meter and mix. In terms of pellet metering and mixing equipment, ABB's batch weighting and continuous loss-in-weight automatic loading systems have maintained the highest accuracy in the industry; however, in some special cases (to avoid the performance degradation and cost increase caused by secondary pelletizing, etc.), some customers require that powders and liquids be added to film extruders at the same time as the pellets. extruder. In order to meet these special requirements, ABB has developed special metering and mixing devices for powders and liquids, which can be used in both gravimetric and loss-in-weight automatic dosage systems to metrically feed and mix pellets, powders and liquids on-line according to the customer's requirements. Depending on the fluidity, regularity of shape and viscosity of the raw materials, the design of the metering and mixing equipment can vary considerably, thus truly meeting the individual needs of the customer.
In plastic film processing applications, weight-incremental and loss-in-weight gravimetric dosing systems each have their own advantages, and film producers can choose according to their needs. Gravimetric automatic dosage systems have lower investment and can meet most of the application requirements in terms of precision and output, which is favored by a considerable part of domestic enterprises; while loss-in-weight automatic dosage systems are generally more likely to attract the attention of customers with high output or higher mixing precision. In the case of increased components and very high output, compared with the batch weighting automatic dosage, continuous loss-in-weight feeding system will undoubtedly be able to meet the production requirements with a smaller footprint. In addition, the separate discharge ports for each component in the loss-in-weight mixer make it easier to change materials quickly during production. As we all know, leaving aside the stretching and other subsequent processes, the extrusion process of film processing is mainly two types of molding: casting (flat film method), blowing method (tube film method). For blow molding, our Guardian series of batch weight dosage is generally preferred to save the user's investment. For customers who require greater accuracy in high volume situations, our X-Series Continuous Gravimetric Dosing offers the highest dosing accuracy and mixing uniformity available on the market today.
Multi-layer co-extrusion of films has advanced rapidly to meet the ever-increasing demands for barrier properties in packaging. In the multilayer film structure, each layer is given the corresponding performance, generally known as the substrate layer, bonding layer, barrier layer, 5-layer film has been more common, 7 to 9-layer film due to a more reasonable structure, better barrier, in China is about to face high-speed development. Multilayer co-extrusion of the various layers, there will always be price differences, high barrier film, this difference is undoubtedly more obvious, therefore, how to control the thickness of the high barrier layer, control the entire multilayer film thickness ratio between the layers, and then in order to ensure that the film high barrier, control the amount of high-priced raw materials, to obtain the ideal structure of the multilayer film, which has become an important subject. ABB's multilayer co-extrusion control system based on dynamic loss-in-weight dosing technology is currently the market's most effective solution to this problem. In the field of film production lines, ABB's leading design concepts of individual dosing control, continuous mixing and independent weighing give ABB's continuous loss-in-weight dosing a huge advantage in terms of dosing accuracy, mixing homogeneity and control accuracy. (Some practices are that the main material is only metered and not controlled, which makes it difficult to guarantee the ratio required by the recipe; others are only metered and controlled according to the ratio without mixing, which makes the mixing uniformity dependent on the mixing performance of the extruder; and others do not set up an independent weighing hopper to independently weigh the final feed rate into the extruder, but only rely on the feed rate of one of the components to convert to control the extruder).
sr online dosing advantages
As mentioned earlier, the asr online feeding system is of great importance in ensuring film quality and reducing costs at the same time. In the film production process, asr online automatic dosing system for the production of waste and trimmings to achieve automatic online recycling, without having to invest in the rest of the re-pelletizing equipment, which avoids the pollution caused by the material in the transportation process, but also to avoid the raw material again heated and melted to maintain the original properties of the material in the recycling application to ensure that the product's intrinsic properties and improve the quality of the product. The recycling of waste materials and trimmings reduces the waste of raw materials and makes the product yield rate of the whole production process greatly improved, and finally obtains the maximum profit and realizes the maximum return for the production investment.
A complete asr system consists of several parts. The trim removal unit transports the strip trim from the extruder line to the film crusher, where rolls of film and/or loose scrap can also be added. The crusher breaks up the scrap and transfers it to the internal hopper of the re-feeder, which meters it into the extruder at a certain scrap-to-material ratio. For lines equipped with the Gravitrol Gravity Extrusion Control System, the crushed material can be gravitationally controlled by the Gravifluf system for full control of the extruder's rate. In China, the system has also been successfully applied in the CPP, BOPET, BOPP and blown film production lines of a number of large-scale film enterprises, which has brought obvious benefits to the customers.
For the plastic film industry's great contribution is not only in the film production process, but also in the film production of upstream links, such as in the masterbatch and film special materials production process, Guardian series batch gravity batching system and X series of continuous gravity batching also plays an important role. In the granulation industry, the X-Series continuous gravity dosage system is generally recommended, mainly because the control of the ratio of the components is particularly critical here, especially in the production of granules with side-feeding, where the components do not need to be pre-mixed and where the dynamic metering accuracy of the loss-in-weight scales is crucial for the functional stability of the granulated product. In the granulation industry, where the addition of powders and liquids is more common, ABB has a wealth of engineering experience and is constantly innovating to provide customers with the best equipment in the industry. In the continuous loss-in-weight gravity dosing, ABB can provide up to 8 components of continuous accurate measurement to meet the needs of most customers, however, due to the initial investment in equipment considerations, there are often users will be a few components of similar density and properties of the component premixed, and then classified as a number of components added to their respective loss-in-weight feeder, and then to meet the customer's metering requirements for accuracy under the premise of this practice, the loss-in-weight feeder will be reduced. This practice reduces the number of loss-in-weight feeders used.