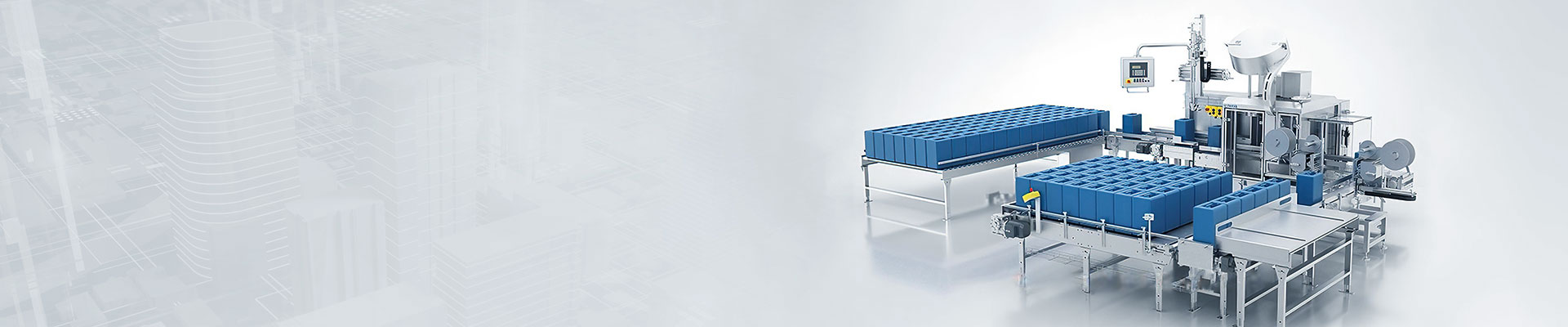
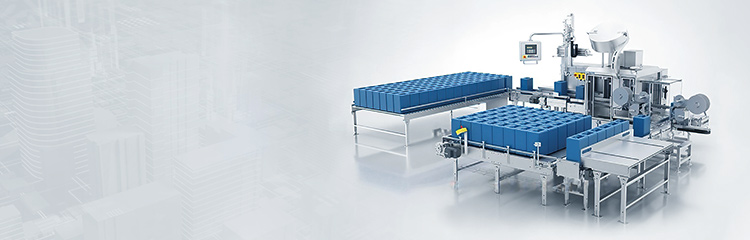
The weighing mixer adopts automatic control to realize the automatic control and supervision of raw material feeding, weighing and metering, vacuum feeding, dispersion and mixing, etc. The dispersion time and cylinder number can be selected and adjusted on the computer according to the production requirements, and the opening and closing of the motor equipment and the opening and closing of the feed valve in the process are controlled by the computer. Automatic filling line is adopted for filtration and packaging of finished products, and the palletizing process is robot palletizing.

Components of the mixer
1) control part: the upper computer adopts industrial control microcomputer, with Mitsubishi or Siemens series PLC communication module and switching input and output modules, as well as manual/automatic control switch, hand-control buttons and lights, etc. are all installed in the integrated control cabinet, easy to operate;
2) Software part: according to the basic requirements of the Dosage system, the actual needs of the user combined with customized;
3) Weighing part: It adopts high-precision weighing module, combined with weighing control instrument combination;
4) Feeding part: pneumatic valve control and screw frequency conversion are adopted for feeding and discharging control;
5) Mixing part: according to the mixing of materials and customer requirements to configure the relevant mixing equipment;
6) Conveying part: adopting screw feeding method or pneumatic method is responsible for feeding the material to the specified position.
workflow
The hopper scales are equipped with a weighing module and connected to an industrial control computer. The system is designed to manually check the zero position of each set of hopper scales during shutdown to monitor whether the zero position of the hopper scales is normal or not, and automatically check the zero position during continuous batching operation to correct the zero position change of the hopper scales to ensure the accuracy of measurement.
After the operator clicks on the dosage running process starts, PLC controls the pneumatic valve and screw of the first material dosing to open, and the material is added into the hopper scale, the computer monitors the signals transmitted from the weighing and metering module in real time and compares them with the target value set by the formula, and when the target value of the formula is reached the PLC control output is disconnected and the pneumatic valve and screw of the first material dosing closes, and the total weights of the hopper scale and the added materials are measured after stabilization, and this value is used as the zero position before the second material is dosed. After stabilization, measure the total weight of the hopper scale and the added material, and take this value as the zero position before the second material is added. Immediately after the start of the second material charging process, and so on repeatedly to the second, third, ......, until all the material charging is completed.
When the dosing process is finished and all pre-set discharge conditions are met, the discharge process starts. The discharge pneumatic valve opens and the mixture flows out naturally under the action of gravity. The system monitors the signals transmitted from the hopper scale sensors in real time. When the total weight of the hopper scale is detected to return to the initial zero position, the discharge valve closes and the discharge process ends, entering the mixing process. The operator can pre-set the opening sequence of each feeding. The system can record the tank number in the transportation type, the actual dosing amount of each raw material, the deviation from the target value set in the formula, the dosing start and stop time and dosing time, as well as the discharging start and stop time and discharging time and other operating data. Through the upper computer application program, you can query and print the raw data and statistical reports of the system operation.
system control
The equipment is controlled by advanced automation products. It adopts Germany SIEMENS programmable controller (PLC) and touch screen (HMI) for logic control; well-known brand low voltage electrical appliances; Delta frequency converter; and weighing module. The products are exported all over the world, and many customers have given high praise.
The whole system is designed to be customer-oriented, with reasonable configuration and humanized operation. Let you use high-tech products at the same time, giving you the pleasure of working and convenient fulfillment.