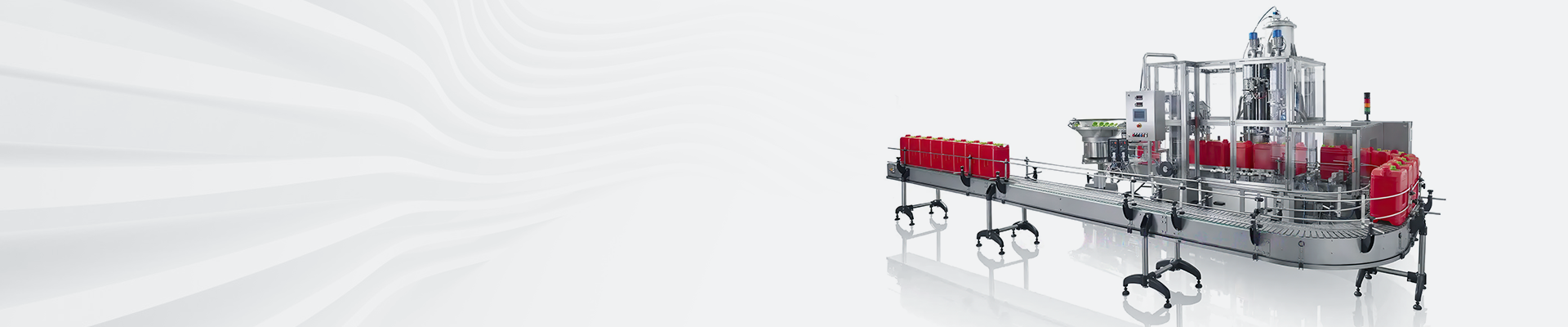
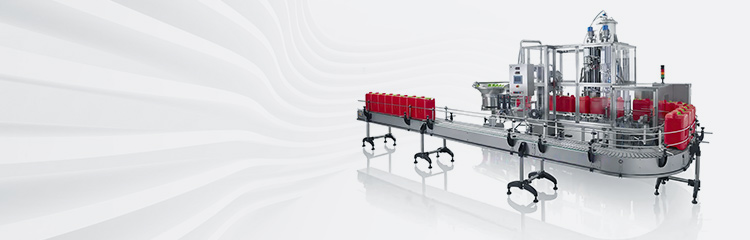

Summary:A set of automatic oxidant screening and weighing batching system based on PLC and fieldbus technology is described. This system is based on Siemens PLC and industrial control computer and uses fieldbus technology to realize remote operation of oxidant screening and weighing, improving Improve work efficiency and protect the health and life safety of operators.
0Introduction
Oxidizer is an important raw material for modern defense industry, commonly used in fire chemical products and solid propellant products in the formula, with flammable, explosive and other characteristics. In the formula before loading, oxidizer raw materials and weighing is an essential process, this process is still used in most of the domestic loading plant manual, face-to-face way of working, there are potential accidents. This paper describes a set of oxidant automatic sieving and weighing control system based on PLC and fieldbus technology, which realizes the remote isolated operation of oxidant sieving and weighing.
1 System composition and structural principle
The oxidizer automatic sieving and weighing control system consists of feeding turntable, elevator, cart, material guide device, rotary brush sieve, three-way distributor, receiving turntable and receiving hopper.
The operator will open and pack the 10 buckets of oxidizer raw material, place them on the 10 stations of the feeding turntable, select the receiving object, and then return to the control room to start the control system. The system will automatically complete the cycle of lifting, receiving, traveling, turning, guiding, screening, receiving, weighing, returning and other actions until all 10 barrels of oxidizer have been screened.
1.1 Feeding turntable
The main function of the feeding turntable is to position the material barrels so as to facilitate the transfer of the elevator. There are 10 stations on the feeding table, which can place 10 drums of raw material packaging drums of oxidizer.
1.2 Elevator
Elevator is used to elevate the raw material barrels filled with oxidizer from the ground to the second floor platform. The elevator consists of oil cylinder, hydraulic station, frame, base, movable frame and protection system. The movable frame contains finger claw, horizontal moving cylinder and horizontal moving frame, the finger claw is usually hidden inside the moving frame, when there are raw material barrels, the finger claw is erected to play the role of stabilizing the raw material barrels. Horizontal moving frame can be extended and retracted when picking up and delivering raw material barrels.
1.3 Trolley
The cart receives the raw material barrels from the elevator, transports them to the front of the rotary brush screen, docks with the material guide device on the top of the rotary brush screen, and then turns over to pour the raw materials into the hopper on the top of the rotary brush screen. The cart consists of overturning frame, chassis, big bracket, legs, cover mechanism, valve plate, rotary clamping mechanism and a series of cylinders, oil cylinders and so on. The chassis is equipped with wheels, which are pushed on the guide rail by double guide rod magnetic pistonless rod cylinders. When the raw material barrel is lifted into place by the elevator, the slewing clamping mechanism will hold the raw material barrel back towards the overturning frame, the cover mechanism will seal the mouth of the raw material barrel, the cylinder will push the chassis to move to the back position along the guide rail, and the cylinder will be driven to realize the raw material barrel flip, and then open the valve plate, and the raw material will be dumped into the hopper above the rotary brush screen through the material guide device. Figure 2 is the schematic diagram of the cart structure.
1.4 Material guide device
The material guide device plays the role of connecting the cart with the hopper of the rotary brush sieve. When the cart is docked with the material guide device, the valve plate of the material guide device opens, and the material enters into the hopper of the rotary brush sieve from the material bucket on the trolley. When the cart leaves, the valve plate closes, which can avoid the material flying.
1.5 Rotary brush screen
The rotary brush sieve is used for sieving oxidizer. The rotary brush sieve consists of explosion-proof motor, drive shaft, brush, chamber, screen and receiving port. The explosion-proof motor provides the power source for the rotary brush screen, and its rotational speed can be adjusted remotely with a frequency converter.
Above the rotary brush screen there is a hopper and material guide device, connecting the cart with the rotary brush.
1.6 Three-way distributor
The main function of the tee splitter is to select the direction of material transfer after screening. The valve plate is inverted to the left when the hopper is selected to receive the material, and to the right when the receiving table is selected to receive the material. 1.7 Receiving table
The main function of the receiving turntable is to quantitatively dispense the screened material into the receiving bucket. The structure of receiving turntable and feeding turntable is largely the same, the difference is that the pallet structure of the material bucket is different, and the pallet of the receiving turntable is also equipped with a jacking weighing mechanism below.
1.8 Receiving hopper
The hopper scale adopts the feeding hopper of the automatic feeding system of the mixing process. The METTLER TOLEDO weighing module is installed under the receiving hopper for weighing the material, the weight of the material is displayed remotely in the control room, and a prompt signal is issued automatically when the weight of the oxidizer in the receiving hopper reaches the set value.
2 Control System
2.1 Control system working principle
The control system of oxidizer automatic sieving and weighing dosage system takes Siemens PLC as the control core (CPU selects CPU313C-2DP), and its main role is: responsible for detecting the state of cylinders and oil cylinders of each device of oxidizer automatic sieving and weighing dosage system, and controlling and coordinating the action of each cylinder and oil cylinder. The dosage control system is equipped with a high-performance upper computer to communicate with the lower PLC, which is used to display the process status and action simulation, and at the same time issue operation instructions to the system.
2.2 Lower computer system design
The control system of the oxidizer automatic sieving and feeding system is equipped with two control cabinets: the on-site cabinet and the remote operation cabinet.
The field cabinet is placed in the power room, equipped with ET200M interface module 153-1 and PLC input/output module. Mainly connected to the hydraulic station motor, electromagnetic reversing valve, cylinder magnetic switch, explosion-proof screen motor, explosion-proof vibration motor and other components, the field cabinet is also installed with gas-electric converter and electronically controlled gas valve, close to the connection of the various cylinders and field operation of the push-pull type reversing valve.
The remote operation cabinet is placed in the control room. It is equipped with Siemens CPU313C-2DP, which acts as the host of Profibus-DP field bus and exchanges data with the field cabinet through Profibus-DP protocol, so that the exchange of field signals and remote signals can be realized through only one Profibus-DP field bus, which greatly reduces the number of cables and shortens the installation and maintenance time.
After the control system of the oxidizer automatic sieving and loading system is started, PLC automatically coordinates the action of each cylinder and oil cylinder to complete the 26-step linkage program such as lifting, receiving, traveling, turning, sieving, guiding, returning, weighing and so on.
2.3 Upper computer system design
The upper computer adopts Advantech industrial control computer, installs Siemens CP5611 board and Configuration King software, and uses Siemens MPI protocol to communicate with the lower PLC, which is used to display the process status and action simulation, and at the same time, issue operation commands to the system.
3 Conclusion
Based on PLC and fieldbus technology, the oxidant automatic sieving and automatic dosing system has a high degree of automation, remote controllable, realizes human-machine isolation operation, minimizes safety hazards, and at the same time greatly improves work efficiency.