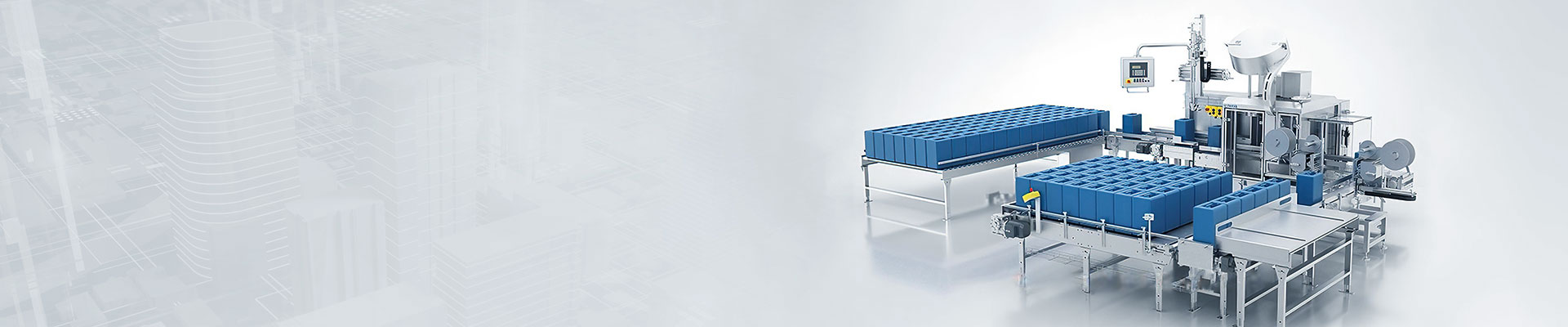
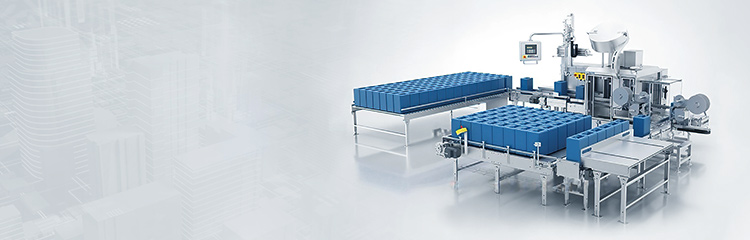
Automated dosage system adopts reducer and mixer with various components, when adding a small amount of powder, it is necessary to configure liquid spraying device, which is more conducive to the uniform dispersion of powder mixed in the main material, so as to achieve the purpose of uniform mixing.

Automatic batching machine consists of upper computer, programmable controller (PLC), weighing instrument, travel switch, frequency converter, temperature sensor and so on. At the beginning of powder batching, the trolley arrives at the bottom of the designated hopper scale, the frequency converter controls the double-speed feeding of the screw Feeder, the weighing instrument outputs the quality signal collected by the load cell to the PLC, and the unloading gate of the hopper scale opens after reaching the set quality value to unload the dispensed powder into the review hopper. If the value of the unloaded powder is within the specified range, the next powder formulation will be carried out, otherwise the alarm will be stopped. When all the powders in the selected formula have been prepared, the gate of the review hopper will be opened, and the prepared powder will be unloaded and sent to the mixer to start the next cycle of the powder preparation process. During the weighing process, the position of the trolley is controlled by a travel switch. Since some of the powder needs to be heated and dehumidified, there is a heating and insulation circuit on these bins, and the temperature sensor collects temperature signals at certain time intervals and sends them to the PLC, which controls the temperature of the bins to keep it in a predetermined range.
According to the powder mixing process, it consists of powder bin, screw feeder, hopper scale, review hopper and powder control system, the hopper scale corresponds to the lower part of the bin, in order to prevent omission and wrong weighing, and to ensure the weighing accuracy, a review hopper is set up under the hopper scale to review the weight of the powder every time it is weighed. Each hopper scale and review hopper is equipped with 3 Weighing modules. The weighing modules are mounted in the radial direction of the hopper and send the weight signal to the weighing instrument through a junction box. The review hopper is driven by a self-propelled trolley, and the review hopper also serves as a collecting hopper.
Through the PLC control of the powder distribution process, the manual control panel to complete the control of the powder distribution process, the failure of the upper computer can also be controlled by the control panel of the manual buttons for emergency control, the control panel buttons and the upper computer can achieve the same control functions, the upper computer as the host, send a variety of commands, store a variety of data. When the upper computer is controlled as the host, it will select the formula, press the start button and then the powder mixing production line will finish the powder mixing work automatically, and store the powder mixing data in the real-time database of the upper computer, so as to carry out the data statistics and report printing.
System features:
1. Fast mixing and large capacity
A batch of materials mixed evenly in just a few minutes, a mix from a few tons to dozens of tons, while saving mixing operating costs.
2.No dead angle design
No recessed round holes, corner residue, etc., can be applied to medical, food and so on.
3. No mechanical rotating parts in the mixer
There is no friction to generate heat and no lubricant to contaminate the product. Because there is no churning, it can be mixed without damage, such as chicken essence, compound fertilizer particles, etc.. Especially suitable for mixing micro-powder, will not jam the rotating machinery such as bearings, etc., trouble-free for a long time.
4. Closed mixing, no dust and environmentally friendly
5. Simple to use, can be set freely, automatic operation.
6. Convenient for feeding and discharging.