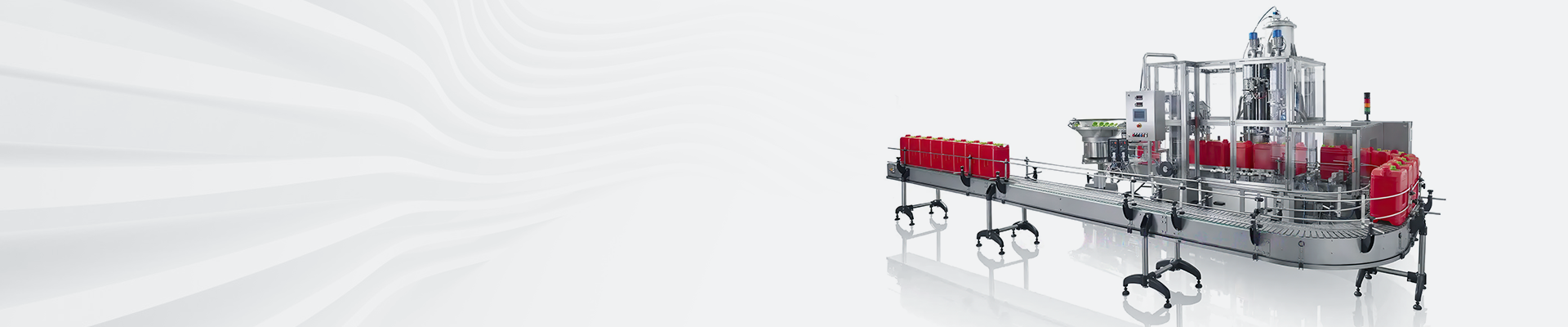
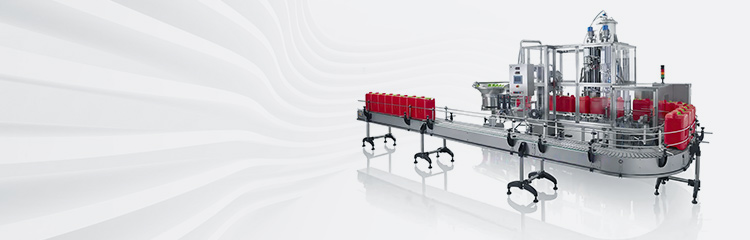

Summary:Distributed batching system (DCS) is a control technology that uses computer technology to centrally monitor, operate, manage and decentralize the production process.Realize data collection, data processing and real-time monitoring of experimental equipment.
Distributed feeding system (DCS) is a control technology that uses computer technology to centralize monitoring, operation, management and decentralized control of the production process. With the development of computer technology, distributed feeding system as a more advanced control technology, the use of automation configuration software and peripheral control acquisition circuit to realize the experimental device data acquisition, data processing and real-time monitoring. It has been widely used in a variety of engineering fields such as electric power, refrigeration, chemical industry, machinery manufacturing, traffic management and so on. In the distributed feeding system, due to the need for communication between a large number of control devices and process monitoring devices, the monitoring and data acquisition system is receiving more and more attention from users, which leads to a large number of configuration software.
2Technical Requirements
Acrylonitrile 2L experimental device is a set of experimental devices for polyacrylonitrile synthesis, polymerization reaction raw materials are strong reducing agent, strong oxidizing agent, acrylonitrile and strong acid. When the experiment is carried out, all kinds of raw materials are placed on the top to monitor the discharging condition of raw materials, and the raw materials are sent to the polymerization kettle by metering pump. The stirrer in the polymerization kettle is driven by the motor at the top of the kettle. Inside the kettle, there is a heating rod to heat up to reach the required temperature of the experiment, and the polymer is automatically discharged through the discharge port at the top of the kettle. The weighing of raw materials in each container, the temperature of the reactor, the speed of the mixer, the PH value of the discharged material and the temperature of the discharged material are all important data that directly affect the experimental effect, because the experimental raw materials contain acrylonitrile with strong toxicity, which makes the experimental environment more severe. Therefore, it is necessary to avoid the experimental personnel to record the data on site as much as possible. It is of great significance to establish a set of stable and reliable real-time dosage.
The computer system to be established should be able to detect the operation progress of the whole experimental device, and the system needs to collect the important parameters in the experiment at regular intervals and realize the alarm for the state that does not meet the experimental requirements. The important signal parameters to be collected and monitored in the whole experiment include:
(1) The weight of raw materials in the four containers, which is output by four DY0Ks with 0~500mv analog signals;
(2) Mixer speed, output by FUJIVR-E1 inverter with 0~10V analog signal;
(3) Polymerization kettle temperature and polymer temperature, by two Pt100 platinum resistance signal converted to 0 ~ 10V analog signal output;
(4) polymer PH value, PH meter produced by Mellter-Toledo company to 4 ~ 20mA analog signal signal output.
3 dosage system development
3.1 Introduction of dosage configuration software
Configuration King is running on Windows98/NT/2000, the user can quickly construct the generation of the upper computer system configuration software package, he easily constructed to adapt to their needs of the data acquisition system, at any time needed to the scene of the real-time transmission of information to the control room, to ensure that the information in the people and the field between the smooth flow. So that field operators and plant managers can see a variety of data. Managers do not need to go deep into the production site, you can get real-time and historical data, optimize the control of field operations, improve labor productivity. kingview 6.02 provides users with a platform for the operation of the work from the device driver, data acquisition to data processing, process control, animation display, report output and other configurations. With multi-tasking, multi-threading capabilities, its system framework using VC++ programming, providing a wealth of equipment to drive components and a wealth of library components, the user can also expand the system at any time according to their own needs.
3.2 Ingredient development process
3.2.1 Create graphic screen
According to the production operation requirements to establish their own screen, in each screen to generate the interrelated static or dynamic graphic objects. The screen includes buttons and menus with certain functions, real-time trend curves, historical trend curves, alarm displays and so on.
3.2.2 Constructing Database
The database is the core part of the configuration software. When TOUCHVEW is running, it contains the current values of all data variables. The set of data variables is called "data dictionary". The data dictionary defines the variable name and variable type of each data variable, etc. Kingview 6.02 also provides commonly used data functions and arithmetic and logical operation modules, and utilizes the C language syntax rules to write a command language to operate on the data variables and generate corresponding data reports.
3.2.3 Defining animation connections
Establishing an animation connection establishes a specific correspondence between the graphical objects on the screen and the data variables in the database, so that when the value of a variable changes, it is represented on the screen by the animation effect of the graphical object; you can also change the value of a data variable through the graphical object.
3.2.4 Running and Debugging
During the development process, the real-time running environment TOUHVEW can be used continuously to run and debug the animated graphic screen created in the screen production system.
3.3 Measurement and dosage function realization
3.3.1 Data acquisition and database establishment
Through the device driver and peripheral I / O data acquisition hardware for data exchange, in order to collect the experiment to get the eight important parameters, data sampling period of 500ms, and will be collected to generate a database of data timed to save the disk, save the disk period of 60000ms.
3.3.2 Dynamic display
(1) Main screen. It displays the whole process flow of acrylic 2L experiment and the real-time display of the measured values of 8 main related parameters. Among them, the mixer impeller rotation animation can react to the working state of the mixer, mixer on, impeller rotation, mixing machine, impeller stationary.
(2) Data display interface. Real-time display of the measured values of all parameters related to the system.
(3) Real-time trend curve: In the process of acrylic 2L experiment, the flow of each raw material can be monitored by the change of weight in four containers, and the change of weight is displayed intuitively and conveniently by the trend curve. In the design process, not only the real-time curve of the weight of the raw materials in the four containers is drawn, but also the real-time curve of other variables.
(4) Historical Trend Curve: The historical trend curve plots the historical changes of data variables, and the experimenters can get the trend curve of each experimental variable through various query operation buttons on the interface, and they can also arbitrarily set the time period for the system to plot the trend curve of the variables during this period. The interface is also designed with a help button, the operator in the query operation process can be obtained through the help file query operation help.
3.3.3 Alarm Function
The acrylic 2L experiment is mainly a process study of acidic acrylics, and the requirements for polymerization temperature and polymer PH value in the experiment are relatively harsh, so the polymerization kettle temperature and polymer PH value are equipped with an alarm function. And according to the experimental requirements, the upper and lower alarm limits can be set arbitrarily.
3.3.4 Reporting system
The data report system has been established and the data report operation menu has been designed. The report menu can query the values of specified time period, specified time interval and specified data variables. The report menu can query the value of specified time period, specified time interval and specified data variable. And the report is designed with printing, layout and refresh function.
4 Conclusion
At present, the weighing and dosing system has been debugged and passed, and the whole system meets the process requirements of acrylic 2L device. The upper computer system realized by Kingview6.02 configuration has friendly interface, stable operation and easy to operate. In the future, the upper computer in industrial control can still choose the software for configuration.