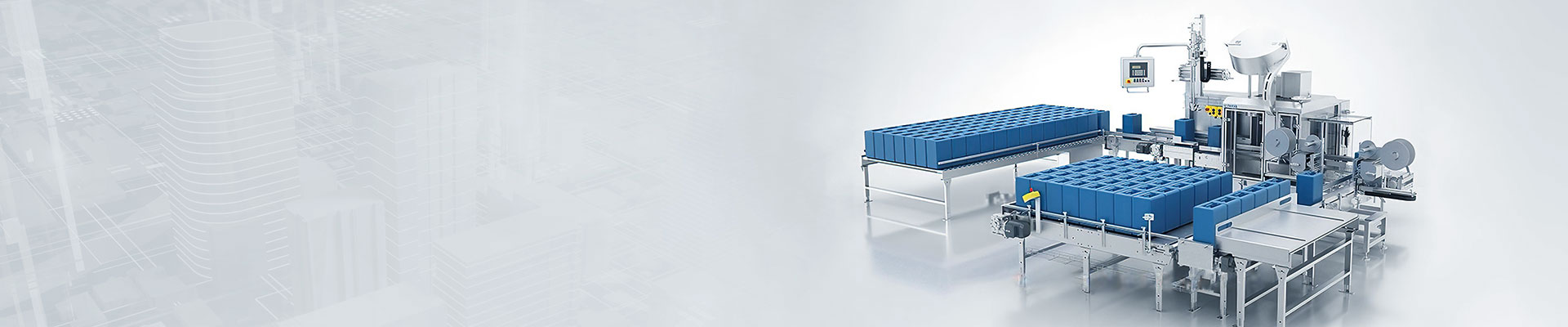
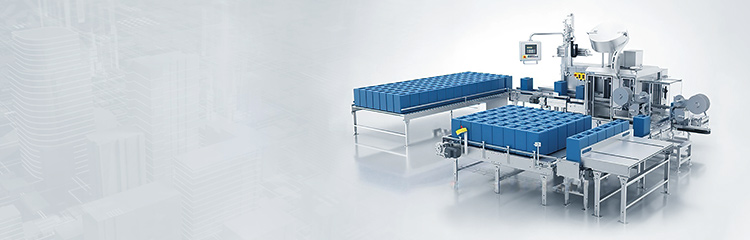
Weighing hopper machine detects and samples the weight of material in the metering hopper by the controller, and stops feeding when the weight of material in the metering hopper reaches the upper limit value set for dosage. It reads the main totalization, instantaneous flow rate, set flow rate, weighing instrument status and other related data from the weighing instrument. Weighing instrument status display (zero state, interval state, running state or alarm state), online monitoring and management by computer, with high requirements on weighing speed, weighing accuracy, system compatibility and expandability.

Automatic batching machine can continuously and automatically complete the weighing and quantitative batching, automatic conveying control and other operations for powder, granule, block and bulk materials in various industrial production environments. It is mainly used to batch small mixes and various powders and miscellaneous materials according to the ratio given by the technology center into the batching silo after a batching process, and the spiral high-speed cylindrical stirring bar stacks the ash to the external discharge port while mechanically stirring, and in order to ensure the humidifying effect of humidifying mixing, it To ensure the humidifying effect of humidifying mixing, 0.6-0.9MPa medium-pressure water is used as the water source of humidifying mixing, and the atomization effect when the water pressure passes through the nozzles of humidifying mixing is better, which is conducive to full wetting; at the same time, a filter is installed on the water inlet pipe of humidifying mixing, to prevent the nozzles of humidifying mixing from being clogged; a ball valve is installed in front of each nozzle, and a shut-off valve is installed in front of and behind the pipeline filter in the water inlet pipe. The ball valve in front of the nozzle is used to adjust the water volume of the nozzle, so that the humidifying mixer has the best humidifying effect. Once the ball valve in front of the nozzle is adjusted, it will not be closed under normal circumstances, but the shut-off valve on the main pipe will be used to cut off the water supply, and a shut-off valve will be installed before and after the water inlet main pipe filter to facilitate the regular cleaning of debris in the pipe filter.
The ratio of the ingredients is the most important part of the whole dosing process, directly related to the quality of the mix. According to the chemical composition of the raw materials used in the small mix, will be similar to the composition of a variety of miscellaneous materials mixed together with mixing, mixing process, used to match the lower miscellaneous materials, raw materials mixed into a material, occupying a batching silo, saving the use of batching silo, shorten the raw material field batching discs of the change of warehouse time and the spiral transportation pressure, to ensure that the amount of material under the disc to improve the quality of the mix. It plays an important role in stabilizing the mixing quality and optimizing the raw material structure.
Product Features:
With safe operator management, realizing multi-level password protection operation.
With perfect formula management function. It is simple to modify and increase the formula, and there is no limitation on the number of formulas;
Can change the order of material drop from the bin at will;
With the function of automatic overshoot compensation for falling material, which makes the dosage precision more accurate;
With input/output detection function, which makes the fault query simpler;
With perfect production report system, including batch report, shift report, daily report, monthly report, and also real-time printing of each batch of production records. Provide detailed data for factory analysis;
Raw material transfer setting can be realized to ensure the normal production when there is no material in the silo;
Convenient dosage parameter and control parameter modification function; self-test function of dosage control system automatically confirms whether each component is normal or not to guarantee normal operation of production;
Power-down self-protection function, which can restore the state before power-down after unexpected sudden power-down. Need to configure UPS;
With alarm function, displaying alarm information and prompting information, and taking corresponding measures;
Individual control can be realized, and its production is not affected when one of them fails, which is more reliable;
Real-time display of various data, real-time display of batching process simulation diagram, intuitive image;