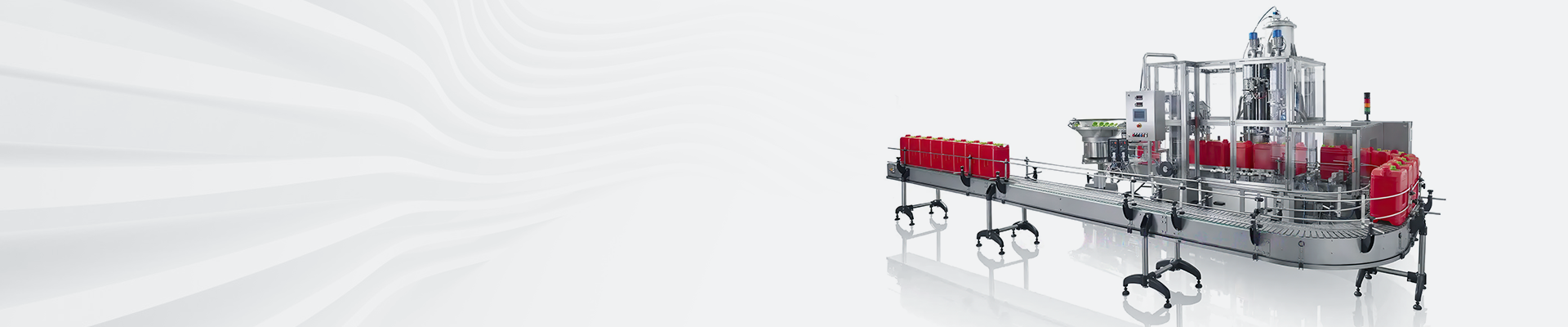
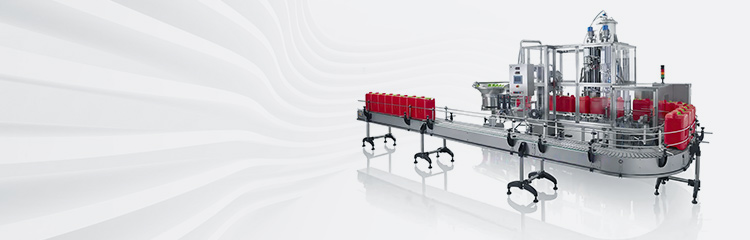

Summary:The hopper scale uses advanced computer network technology, automatic control technology, and automatic measurement and detection technology to realize dynamic storage capacity and inventory management of raw material storage, and to monitor and record the consumption and destination of raw materials throughout the process.
Hopper scales should be set up so that the entire material handling system as simple as possible, if possible, the original hopper on the weighing device is ideal. Even if the new weighing hopper, it should also make the hopper scale and the intermediate link between the belt scale as little as possible, in order to reduce leakage losses in the process of material transfer, improve the accuracy of the test.
Hopper scales can be installed on the hopper before the belt scale according to the principle of weighing in advance; can also be installed on the hopper after the belt scale according to the principle of weighing afterwards.
Hopper scales can be installed in the main flow of material or in the auxiliary flow. Normal material handling needs to pass through the part called the main process, when the hopper scale installed in the auxiliary process, normal material handling does not go through the hopper scale, test the material only after the hopper scale.
When the process is equipped with multiple belt scales, if possible, a hopper scale should be able to test as many scales as possible. Such as in more than one dosage belt scale system, can be installed in the total belt below a hopper scale, so that not only can test the total belt scale, but also can test each small dosage belt scale.
For some particularly large conveyor belt scales, the capacity of the hopper scale is correspondingly large, in order to reduce the capacity of a small weighing hopper can be used in a small weighing hopper after the addition of a large storage hopper method.
As a material test used to determine the quality of the test material control, according to the electronic belt scale national calibration regulations, in the material test immediately before the calibration or verification, hopper scales weighing allowable error should not be greater than the first inspection of the belt scale dynamic cumulative error of the value of 1 / 3, in other cases, its error is at least not greater than the automatic weighing of the corresponding maximum permissible error of 1/5. control can be used to use hopper scales, if you use a rail scale as a control, no matter how much the hopper scale, if it is used as a control, it is not possible to use a large storage hopper. Track balance as a control, whether tare or gross weight should be determined on the same.
Hopper scale capacity should be determined in accordance with the national measurement and verification procedures "continuous cumulative automatic (JJG195 - 2002)" on the minimum test load provisions, that is, not less than the maximum value of the following values.
Hopper scales itself should also be considered in the design of the test facilities, such as the use of stereotypes with calibrated hopper scales material test device. If this can not be done, it is necessary to consider the method of loading weights on the reaction tank and the location of the storage of weights, etc., so that its test as convenient as possible.
Combined with the characteristics of the process, strengthen the intelligent chain management of the process path and fail-safe protection functions, to realize automatic process path selection, chain, fault identification and control;
Measurement and detection of raw materials in and out of storage and safe chain control of the conveying process, realize the dynamic storage capacity and inventory management of raw materials storage, carry out full supervision and record of raw materials consumption and destination, continuous measurement and monitoring control and data management of the material ratio of the production process, comprehensive record management of the data of the finished products packaging and storage, realize the consumption of raw materials and semi-finished products from the classification of the use of raw materials and the consumption of the process of the power consumption of the whole process, to the product output ratio and energy consumption, to the product output ratio and energy consumption. It realizes the comprehensive analysis and statistical management function of processing data from raw material and semi-finished product consumption, process segmentation and power consumption throughout the whole process, to product output ratio and energy consumption ratio;
The batching machine adopts advanced computer network technology, automatic control technology, automatic measurement and detection technology to set up an automatic control system with excellent and reliable performance, reasonable construction cost, convenient expansion and easy maintenance, realizing the overall system functions of automatic control, automatic batching, full measurement and monitoring and comprehensive data management;
Conveying control mode adapts to the conveying type characteristic requirements of different processing links, such as horizontal and vertical conveying control of conventional conveying equipment and corresponding safety monitoring and chain control of conveying equipment; dilute-phase pneumatic conveying of powdery materials and dust collection management control;
Dynamic process flow display screen, the operator can monitor the entire production and dosage control process intuitively through the color monitor, including the bin conveying equipment, weighing data, mixing or processing equipment and a variety of process gate and valve work status;
The hopper scale can detect, monitor, display, store and print the instantaneous signals, variables, parameters, etc. in real time, realizing the whole production data record, and adopting dynamic database for storage and management;
The system can not only apply Profibu/Modbus/Canbus/RS232 and RS485 serial communication in the industrial control network interface specification requirements, also has a high-speed industrial Ethernet reliable connection capability;
For the material ratio measurement of professional requirements, the system has a zero point / tare weight quickly remove the function; measurement control error can be achieved ± 0.25-0.5% of the control capacity, measurement accuracy and cost and site conditions are closely related;
Can be set up to prevent misuse of the system and other functions, with self-diagnostic capabilities; multiple operator login and password security management, enhance system data integrity and security protection capabilities.