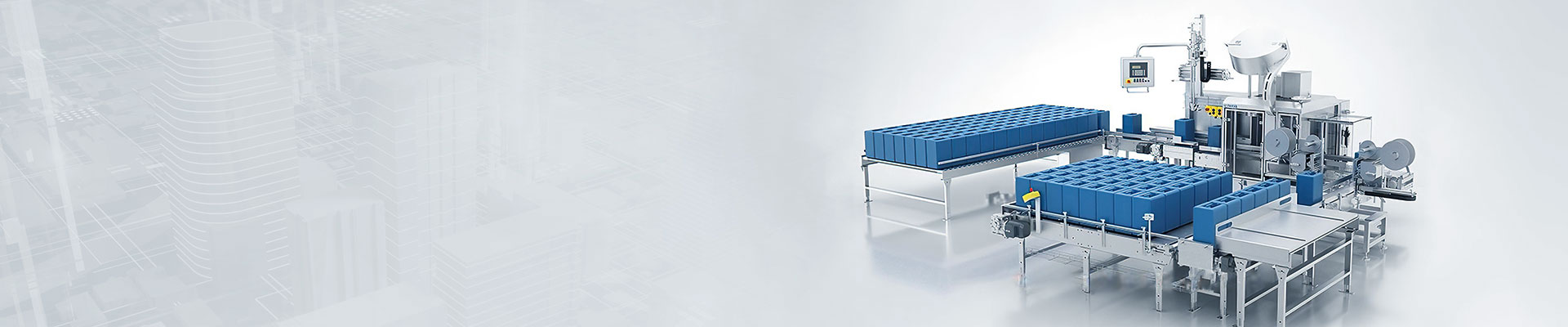
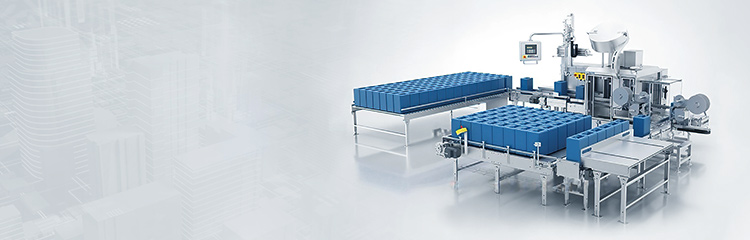
The lubricating oil dosing system realizes PLC on-line control, the valve position and discharger position signal detection adopts load sensor, and the bin location adopts heavy weight type material level meter, which can realize continuous warehouse location detection. The control unit is mainly a touch screen, PLC as an auxiliary control system, man-machine interface display ratio parameters (formula) and monitoring and recording real-time data. According to the speed of weighing material, the lead amount is provided. When the weight is detected to reach the set value, the lead amount is subtracted, and the control instrument closes the feed valve. The lead amount can be manually corrected or automatically corrected, so that the control instrument can control the batching precision of each batching scale to reach the set target value.

The automatic Dosage system with liquid materials for several storage tanks is fed to the reactor after volumetric metering, realized by the weighing module and weighing controller with fixed value and ratio functions, which can be directly used for the process control of production dosage. According to the standard signals entered into the weight module, it realizes weighing and metering, automatic control, data counting and uploading; according to the operating environment and the actual requirements, it is possible to set the minimum credible weight, if the proportioning material is less than the minimum set value, the weighing controller alarms on the display that the value obtained is not in the set range. The weighing controller is also equipped with an RJ45 Ethernet port, which allows access to the upper control system. The operator in the control room can monitor the weighing data, adjust the settings, generate reports, backup or restore the data through the control system, which is a complete solution for the realization of the measurement and control of the weight in a single unit.
Three Weighing modules are installed at the bottom of the kettle, and the three weighing modules output signals 4~20mA to the weighing controller installed at the site, and the weighing controller superimposes the three values into the quality of the materials, and at the same time accumulates the quality of inputs of all kinds of materials. A shut-off valve is installed on the main pipe of all the material lines into the reactor to interlock with the weight signal; the weighing controller communicates with the control system in the control room through PROFIBUS-DP bus, and the control system in the control room carries out the automatic metering and control of the material according to the stored or set formula ratio. The on-site controller has the functions of manual feeding and automatic feeding selection, and the weight of the materials fed manually and automatically are recorded and accumulated by the control system. At the same time in the automatic feeding state cut-off valves and pumps and set parameters automatically interlocked.
The high precision of weight metering ensures the high quality of the product, and the bus transmission of weight metering improves the control system capability and reliability, thus perfecting the operation capability and level of the whole kettle feeding system. With the rapid expansion of the scale of industrial automatic production, industry competition is becoming increasingly fierce, the requirements of the control system from the simple completion of the production task, to the set of control, optimization, management, communication and other aspects as a whole, weighing module monitoring system into the kettle feeding control use has a very good prospect.
Lubricant dosing system process flow overview:
(1) the base oil, additives from the storage tank through the diaphragm pump into the blending kettle;
2)Mixing, using pulse mixing device or frequency conversion stirrer to make the base oil and additives completely mixed;
3)The finished oil is pumped into the high level storage tank by diaphragm pump;
4) Filling and packing out of the warehouse.
Overview of batching production:
(1) The base oil and additives are pumped from the storage tank into the blending kettle by diaphragm pump.
2)Mixing, using pulse mixing device or frequency conversion mixer to make the base oil and additives completely mixed.
(3) The finished oil is pumped into the high level storage tank by diaphragm pump.
4) Filling and packing out of the warehouse.
Production points: dosing accuracy for the lubricating oil industry is one of the most important production process, which directly affects the quality and sales of oil products.
Dosing equipment configuration:
1. The whole set of lubricating oil dosing equipment consists of reaction kettle, mixing equipment, storage tank and heating device, etc. The parts of the whole set of equipment contacting with materials are made of stainless steel.
2. Strong power cabinet: Schneider brand electrical components are used to control the strong power equipment.
3. Weak power cabinet: It is used to load the industrial controller to realize the control of the production equipment and the acceptance of data.
4. Field operation box: the components include weighing display instrument, four-way data display instrument, touch screen, etc. The buttons can realize the start-stop control and speed regulation function of the motor.
5. Central control room: it contains industrial control upper computer, sound and light alarm device and other equipments.
6. Configure static electricity elimination device in workshop and tank area, and voice prompts will be carried out after static electricity elimination is completed.