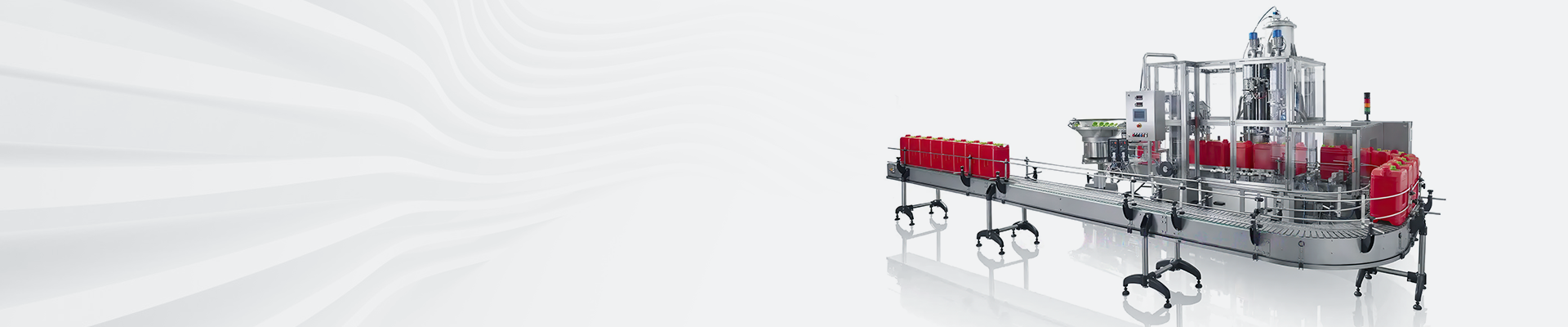
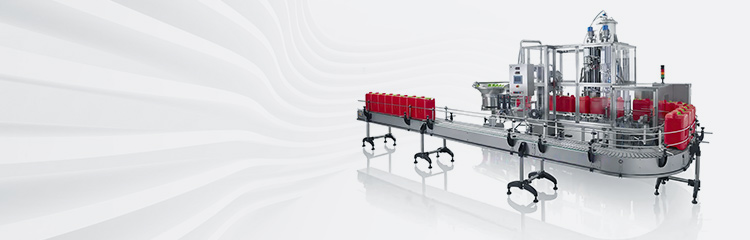

Summary:The batching system consists of upper and lower computers composed of PC and PLC, combined with weighing module technology, communication technology and fuzzy control technology, with the weighing display as the control center to control other equipment to complete the batching.The raw materials are driven from the silo into the weighing hopper by the auger, and different materials are transported respectively.
Lubricating fluid industry is an extremely important key link in the industry chain connecting the seed processing industry, shipbuilding industry, locomotive manufacturing and so on. As one of the emerging industries in the world economy, it has developed rapidly in a relatively short period of time, and has been highly valued by governments and business circles. Lubricant processing line control is characterized mainly by the sequential control between the processing equipment and testing devices, and this sequential control is exactly where the advantages of PLC control.PLC control is the current industrial batching in the application of a very wide range of control methods, the use of PLC control can greatly improve the degree of automation of production. Programmable controller and the upper computer PC communication to achieve, can make the production process overall optimization, to ensure normal production and management of the liquid level. Various pre-mixed lubricant, concentrated lubricant, with lubricant-based lubricant production workshop two, the latest production line built using microcomputer control technology, modernization of the liquid level is relatively high; while the early construction of the production line is still contactor, relay control mode, the management of the liquid level and production efficiency are far lower than the other production line. In order to adapt to the production demand, the old production line has been technologically modified.
1 lubricant production process
The traditional lubricant production enterprise adopts series arrangement, that is, the material from the raw material warehouse, according to the process flow in turn through the various workshops, and then arrive at the finished product warehouse. However, with the increasing variety of products and the continuous difference of product types, in recent years the parallel layout has been replaced, that is, the material can be divided into multiple routes, while passing through different workshops, and finally reach the finished product warehouse. Obviously, this method greatly improves the yield of serial materials, reduces interference, and is more efficient in production. At the same time, this layout is also conducive to the reasonable laying of power lines for aids, electricity and gas, reducing investment costs. At present, the company's workshop layout is designed according to the parallel layout. At present, some production ingredients also put forward the workshop combination layout mode, that is, to set up the raw material warehouse, finished product warehouse, laboratory, inspection room, etc. for specific products in the production workshop. Combined, the material flows in the workshop, changing the original raw material warehouse, workshop and finished product warehouse split, saving the logistics of the trip and time, greatly improving production efficiency.
Most of the traditional lubricant dosage workshops are established according to the process, especially in the former large and medium-sized lubricant factories, the vast majority of which are established according to the process of specialized production lines. The advantages of setting up the workshop according to the process specialization include:
(1) high utilization rate of liquid filling machine in batching;
(2) Dosing facilitates professional management of the process. The computer weighing monitor is used as the control center to control other equipment to complete the batching. Raw materials are driven by the motor to fall into the hopper scale from the silo, which conveys different materials separately. The running speed is regulated by a frequency converter according to the output voltage of the weight indicator. For the actual dosage, the dosage recipe and the batch are set through the keypad of the weight indicator, then the automatic dosage system is run and the weight indicator automatically selects the required silo, drives the motor and makes the material fall into the hopper scale. Through the weighing module of the hopper scale to control the frequency converter speed regulator, adjust the speed to control the feed amount, so that the end point value to achieve sufficient accuracy, the end of the dosage, automatically open the door, the material into the mixer mixing. Weighing display automatically calculates the mixing time, until the end of mixing, put the finished product out of the material.
2 PLC-based overall control program design
Automatic batching machine consists of industrial computer, PLC module, industrial configuration software, intermediate relay, AC contactor, thermal relay, air switch and so on. In the Windows environment, the metering and batching system using industrial configuration software to draw the actual process, you can make the production line of the various motors, control valves, pumps, pipelines, the flow of the process is displayed, you can be very intuitive to understand the production situation and control the entire process. The whole system is centralized in the central control room. The center control room is set up next to the platform in the workshop for placing the main control cabinet and the center console.
Measuring process: Enter the formula before production, the computer will start the corresponding automatic valve according to the formula amount, when the weighing reaches the set value, the weighing module senses the target weight and closes the feed valve automatically, and at the same time, it will start the measurement of another kind of additives. When the metering is finished, the discharge valve of metering reaction tank will be opened automatically, and the corresponding automatic valve of dispersing kettle No. E1 (the number of reaction tank will be set first) will be opened, and the additives will be sucked into the dispersing kettle No. E1 in a vacuum. After all the additives are fed, input the weight of lubricant feeding in the same way, click the lubricant feeding valve, and use a small amount of lubricant to clean the metering reaction tank and the downstream pipeline to ensure that there is no residue of additives.12 kinds of additives are measured and transported as an automated process of control, and the metering reaction tank can be taken to add add the additives first, and then add the liquid way.
Automatic dosage system tons of raw materials from the pressure feed reaction tank pressed into the silo for storage. 5 kinds of raw materials measurement and delivery for automated control process, the use of raw materials metering reaction tank measurement. Computer control, according to the weight of the charge, automatically open the corresponding valve, linkage start the corresponding screw conveyor to start charging, when the weighing reaches the set value, the metering module senses the weight of the chain control of the feed valve and screw conveyor closed. Measurement is complete, the metering reaction tank discharge valve is automatically opened, and open the GD1 transition reaction tank feed valve raw materials into the transition reaction tank storage, E1 dispersing kettle to add raw materials, take the bottom of the kettle feeding, vacuum inside the kettle, the transition reaction tank discharge valve and the E1 reaction tank feed valve is automatically opened, the raw material from the bottom of the reaction tank body into the kettle.
Lubricant production process of each dosage is relatively independent, the automation of lubricant production, including the automatic control of the entire dosage and the automatic control of each process and the automatic control of stand-alone equipment; which PLC is responsible for controlling the operation of on-site equipment and access to the operating state and fault information, sensing system to collect the on-site information and data, computers use network communication to obtain data for storage and management, dynamic display of the process flow The PLC is responsible for controlling the on-site equipment and obtaining its operating status and fault information. Its core control component PLC, the use of modular programming ideas, separation of subsystems and relatively independent of the internal function, and the functional blocks in accordance with the lubricant production dosage of the process flow through together to form the entire dosage of the centralized control, and through the network to achieve the remote monitoring and command system with the production management.
3 mixing design
3.1 Mixing process program selection and dosage determination
Dosing process is the key link in the lubricant production process, its dosing accuracy directly affects the quality of lubricant products. Mixing and dosing to realize the two or more materials in accordance with certain ratios automatically added to the mixer, after mixing to meet the pre-determined requirements of the process of automatic discharge. Through the comparison of the advantages and disadvantages of common weighing and mixing process solutions, the electronic scale mixing process is selected, that is, all the measured materials in accordance with their physical properties or weighing range for grouping, and each group is equipped with the corresponding measuring device to achieve the measurement operation, so as to economically and accurately complete the entire dosage process. The mixing process can significantly shorten the mixing time of the lubricant and greatly increase the output.
The automatic batching machine consists of PC, PLC, feeder, hopper, weighing module and actuator. The batching operation process is firstly transmitted from the upper computer to the lower PLC by the raw material formula data, and then controlled by the PLC. Various lubricant raw materials are distributed into the corresponding dosing reactor for storage through the reactor top conveying equipment and distributor. When dosing, the raw materials are sent to the hopper in sequence by the feeder. Raw materials with large proportion (20%) are sent to the large hopper weigher; raw materials with small proportion (5%-20%) are sent to the small hopper weigher. The weighing module detects the quantity of each material and transmits the signal to the weighing controller to control the feeding of the feeder, thus controlling the dosing of each material. When all the materials of the reactor according to the set formula requirements weighing dosage is completed, to reach the specified cumulative quality (the amount of each batch of material), the PLC in accordance with the control program to open the material valve, the hopper weighs the material into the mixer mixing room for mixing. Mixer to achieve a predetermined mixing time, that is, mixing uniformity to meet the requirements, under the control of the PLC, the material valve opens out of the material, feeding to the buffer kettle, falling into the finished product scraper-type conveyor, sent to the entrance of the bucket elevator transported to the mixer kettle storage, to the next process.
3.2 Hardware design of dosage
The upper computer selects the brand machine with standard RS232C communication port and printer interface, this system requires high control accuracy, according to the number of input and output signals, the lower computer selects a Mitsubishi FX2N-80MR PLC and two FX2N-16EX expansion units, and selects SC-09 programming cable as the connecting line of the communication between the computer and PLC. In the whole system, the dosage system selected resistance strain type weight weighing module, its accuracy to meet the requirements of the dosage, should be higher than the dosage accuracy of one level.
3.3 Batching software design
According to the production process, the computer transfers the corresponding formula and production process parameters to PLC, which controls the inverter to start the dosage work according to the formula parameters and the order of dosage, and the weighing signal is detected by PLC. Batching sequence: weighing is completed, when the mixer has material, the hopper valve is closed; when the mixer is discharged off the valve in place, the hopper valve is open. Hopper weighing valve open time arrives, detect the hopper weighing the remaining material, when the remaining material exceeds the limit value, the system alarm, the hopper weighing valve does not close. When it is lower than the limit value, the hopper weighing valve is closed. After the hopper scale valve is closed in place, if the scheduled production batch is not completed, dosage continues and a signal is sent to add premix and grease. After the premix is added and the answer reset is completed, the mixer starts mixing and timing, and after the mixing time is reached, the mixer opens the valve to discharge the material according to the material level in the buffer hopper. Mixer open valve timing, open the valve time reached, the mixer valve automatically closed, such as the next batch of material fall, start a new round of circulation. The dosage system uses modular programming approach, the central idea is to divide a complex application program into a number of relatively independent program modules according to the overall function. In this dosage system, according to the functions accomplished by the program, it is mainly divided into three program modules:
(1) The feeding module completes the raw material discharging and weighing signal acquisition of each material reactor according to the formula parameters and feeding order to ensure that each raw material is within the tolerance range. After the feeding stops, from the screw feeder to the hopper weighing part of the raw material to fall into the hopper weighing, need to take into account this part of the material, the program with the amount of retention on behalf of this value. Retention is based on the enterprise production experience data, through the test to select the optimal value to determine. The frequency converter is set to multi-speed frequency, and the frequency of the frequency converter is controlled by the output point of PLC. When the feeder is dosing, PLC controls the feeder motor to run in the high-speed section of the frequency converter, and when the amount of raw material is approaching (feeding amount - retention amount), the feeder motor is controlled by the PLC output point to run in the low-speed section of the frequency converter for slow dosing. Feeding process, PLC will be the amount of raw materials and (feed amount - retention) real-time comparison, within the tolerance for qualified, stop feeding; close to the lower limit of the tolerance, should be carried out inverter low-speed section of the feeding; greater than the upper limit of the tolerance for the exceeding the tolerance, the alarm.
(2) The valve module controls the weighing reactor valve to open and close in a logical sequence, so that the dosing of the current batch is completed smoothly.
(3) The mixer valve module realizes the logic control of buffer reactor valve and mixing valve, so that the dosage will complete mixing and stirring according to the set time.
In the program design, the entire program is divided into several functional modules are realized, PLC work through the main program to call the subroutine to complete the corresponding function.
4 dosage fuzzy control and simulation
Due to the changes of process parameters, material properties, fallout, etc., the model of the dosage system is nonlinear and time-varying. In order to improve the impact of fallout and other factors on the accuracy, can be used to predict the fallout and approximate control of the dosage amount to improve the dosage accuracy. According to the characteristics of lubricating fluid plant repeated batch weighing, the use of a large number of existing weighing error data on the spatial material amount of fuzzy adaptive compensation control can ensure that the material error fluctuates within the minimum range.
4.1 Control principle of fuzzy PID
The dosing controller receives the control flow data from the host computer as a given, compares it with the actual detected flow, and through the fuzzy PID control method, calculates the corresponding output (0~5V voltage or 4~20mA current) to control the frequency converter, so as to control the rotational speed of the motor, and make the flow rate of the dosed raw materials reach the given value.
5 Application
The batching production line is mainly composed of monitoring screen, industrial control machine, operation desk, distribution cabinet and so on. Its functions include the following aspects:
(1) Dynamic monitoring function: the running status and material flow of the liquid filling machine can be clearly displayed on the screen.
(2) Recipe management function: the technical recipe is stored in the computer. In the production process, the formula determines the material proportion and feeding order in the dosing process of different products. Therefore, the automatic dosing system needs to call up the formula before production, automatically calculate and weigh various materials, and maintain the accuracy of the proportion.
(3) Automatic batching, filling and measuring: Filling and batching is one of the most important processes in the production of chemical products, known as the "throat" process. The quality of the filling and dosing process plays an important role in the quality of the whole product. In the production process, the pneumatic ball controlled by the dosing system can realize automatic measurement and automatic feeding according to the formula to ensure stable product quality.
(4) Mixing speed control: the batching system controls the frequency converter to control the mixing speed, different materials can be mixed at different mixing speeds to ensure uniform mixing.
(5)On-site adjustment control: a small amount of material can be added according to the production requirements of the product to realize on-site adjustment.
6 Conclusion
Application of PLC technology on the traditional lubricant dosage modernization technology transformation research, developed an overall control program, combined with weighing module technology, communication technology and fuzzy control technology and other related knowledge, theoretical research and practical demonstration, designed a set of PLC as the core of the control, composed of PC and PLC up and down the machine of the system. Practice has proved that the batching system runs reliably, the accuracy basically meets the requirements, and it is fully adapted to the requirements of modernized production management of the enterprise.