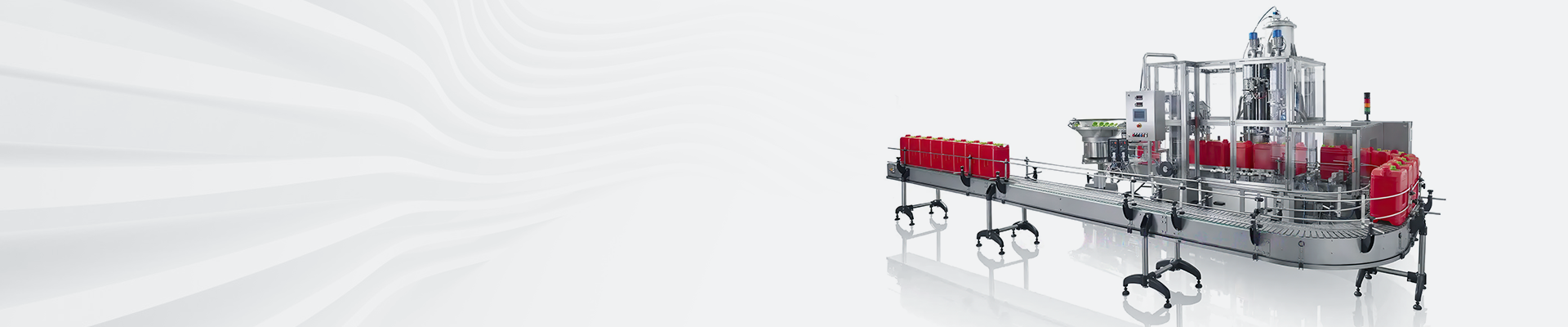
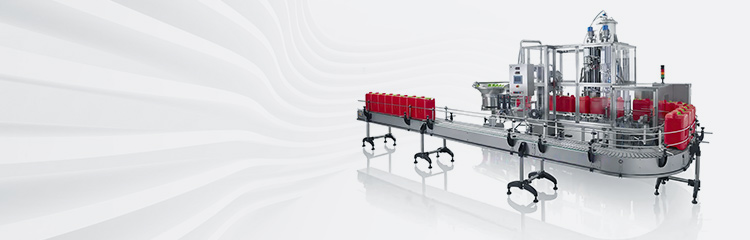
摘要:配料系统由PC机和PLC组成的上下位机结合称重模块技术、通信技术和模糊控制技术,以称重显示器为控制中心,控制其它设备完成配料。原料由绞龙驱动从料仓落入称斗,分别输送不同的物料。
以润滑液配料技术改造为背景,阐述了润滑液生产的工艺流程,采用基于PLC的分布式配料系统作为总体控制方案,分析了润滑液生产的主要环节并给出了控制方案。设计了基于PLC的配料系统,给出了加料系统的硬件设计和软件控制流程,并对加料系统的PID控制进行了研究。结果表明,PLC技术改造后润滑液的调配精度大大提高。
润滑液产业是连接加工业、造船业、机车制造业等产业链中极其重要的关键环节。润滑液产业是连接加工业、造船业、机车制造业等产业链中极其重要的关键环节。润滑液产业是世界经济中的新兴产业之一。 它在短时间内迅速发展并得到了世界各国政府和企业界的高度重视润滑液加工生产线的控制特点主要是加工设备和检测装置之间的顺序控制而这种顺序控制是PLC控制的优势PLC控制是目前工业配料中广泛使用的控制方法, PLC和PC之间的通信可以优化整个生产过程,确保生产的正常进行和管理水平的提高有两个润滑剂车间,包括预混合润滑剂,浓缩润滑剂和混合润滑剂新建的生产线采用微机控制技术,现代液位相对较高。为适应生产需求,对旧的生产线进行了技术改造。
1润滑液生产工艺
传统的润滑剂生产企业采用串联排列,即物料从原料仓库开始,按照工艺流程依次经过各个车间,然后到达成品仓库。然而, 随着产品种类的不断增加和产品类型的不断差异,近年来平行布局已被取代,即物料可以分为多条路线,同时经过不同的车间,并最终到达成品仓库显然,这种方法大大提高了系列物料的产量,减少了干扰,同时具有更高的生产效率, 这种布局也有利于添加剂、电力和燃气等电力线路的合理铺设,并降低投资成本。目前公司的车间布局是按照平行布局设计的。一些生产配料也提出了车间组合布局模式,即在生产车间内设置原材料仓库、成品仓库、实验室和特定产品的检验室。
大多数传统的润滑液配料车间都是按照工艺建立的,尤其是在以前的大中型润滑液厂,绝大多数都是按照专业生产线的工艺建立的。根据工艺专业化设立车间的优点包括:
(1)配料中液体灌装利用率高;
(2)配料便于工艺专业管理。以电脑称重显示器为控制中心控制其他设备完成配料。原料由电机驱动从料仓落入料斗秤,分别输送不同的物料。运行速度由变频调速器根据称重显示器的输出电压进行调节。在实际配料中,通过称重显示器的键盘设置配料配方和配料批次,然后操作自动配料系统。称重显示器自动选择所需的料仓,并驱动电机使物料落入料斗秤。通过料斗秤的称重模块控制变频调速器,调节速度来控制给料量,使最终数值足够精确。配料完成后,门自动打开,物料进入搅拌机进行混合。称重显示器自动计算混合时间,当混合完成时,成品排出。
2基于PLC的总体控制方案设计
自动配料机由工控机、PLC模块、工业组态软件、中间继电器、交流接触器、热继电器和空气开关组成。在Windows环境下,计量配料系统采用工业组态软件绘制的实际流程图,可以显示生产线各电机、控制阀、泵、管道的流程图,可以直观地了解生产情况,进行全程控制。整个系统都集中在中央控制室。车间内平台旁有一个中央控制室,用于放置主控制柜和中控台。
计量流程:生产前输入配方,电脑根据配方量启动相应的自动阀门开始投料。当称重达到设定值时,称重模块感应目标重量并自动关闭进料阀,同时开始计量另一种助剂。计量结束后,自动打开计量反应釜的出料阀,打开E1分散釜(先设定好反应釜的编号)上相应的自动阀,将助剂真空吸入E1分散釜中。添加完所有添加剂后,同样,输入润滑液的添加重量,稍微移动润滑液进料阀,用少量润滑液清洗计量反应罐和下料管道,确保没有添加剂残留。12种添加剂的计量输送是一个自动控制过程,计量反应罐可以采用先加添加剂后加液体的方式。
自动喂料系统吨包原料由压送反应罐压入料仓进行储存。5种原料的计量和输送为自动化控制过程,利用原料计量反应罐计量。计算机控制,根据加料的重量,自动开启对应阀门,联动启动对应螺旋输送机开始加料,当称重到达设定值,计量模块感应重量连锁控制进料阀门及螺旋输送机关闭。计量完毕,计量反应罐的出料阀门自动开启,并打开GD1过渡反应罐进料阀门原料进入过渡反应罐储存,E1号分散釜加原料时,采取釜底上料,对釜内抽真空,过渡反应罐出料阀及E1反应罐进料阀自动打开,原料从反应罐体底部进入反应釜内。
润滑液生产过程中的每一个配料相对独立,润滑液生产的自动化包括整个配料的自动控制与各工序自动控制以及单机设备的自动控制;其中PLC负责控制现场设备的运行并获取其运行状态及故障信息,传感系统采集现场信息数据,计算机利用网络通讯获取数据进行储存管理,动态显示工艺流程、设备运行状态、生产数据、报警信息,并生成各类生产报表。其核心控制部件PLC,采用模块化的编程思想,分离各子系统与相对独立的内部功能,并将各功能块按照润滑液生产配料的工艺流程贯穿在一起,形成整个配料的集散控制,并通过网络实现与生产管理的远程监控指挥系统。
3混合设计
3.1混合工艺方案选择及配料确定
配料工序是润滑液生产过程中的关键性环节,其配料精度直接影响着润滑液产品的质量。混合配料实现将两种或两种以上的物料按照一定的配比自动定量加入到混合机内,经过混合达到预定要求后自动出料的过程。通过对常见称重混合工艺方案优缺点的对比,选择电子秤配混工艺,即将所有计量的物料按照其物理性能或称量范围进行分组,每组配上相应的计量装置来实现计量作业,从而经济、精确地完成整个配料过程。配混工艺能够显著缩短润滑液的配混时间,大幅度提高产量。
自动配料机由PC机、PLC、送料器、料斗、称重模块和执行机构等组成。配料运行过程是先由上位计算机将原料配方数据传到下位机PLC,然后再由PLC进行控制。各种润滑液原料经反应釜顶输送设备和分配器分配进入相应配料反应釜中存贮。配料时由送料器分别依次将原料送至料斗称中。大配比(20%)的原料送至大料斗称;小配比(5%~20%)的原料则被送至小料斗称称量。称重模块检测每种料的数量,将信号传给称重控制仪,控制送料器的给料,从而控制每种料的定量。当全部料反应釜的物料按设定配方要求称量配料完毕,达到规定累计质量(每批料量)时,PLC依照控制程序打开料阀门,将料斗称内物料放入混合机混合室中进行搅拌混合。混合机在达到预定的混合时间,即混合均匀度达到要求时,在PLC的控制下,料阀门开启出料,送料至缓冲反应釜,落入成品刮板式输送机,送至斗式提升机入口升运至混合料反应釜贮存,至下一工序。
3.2配料硬件设计
上位机选择带有标准的RS232C通信口、打印机接口的品牌机,本系统控制精度要求高,根据输入输出信号数量,下位机选用一个三菱FX2N-80MR型PLC和两个FX2N-16EX拓展单元,选用SC-09编程电缆作为计算机与PLC通信的连线。在整个系统中,配料系统选用电阻应变式重量称重模块,其精度满足配料的要求,应该比配料精度高一个等级。
3.3配料软件设计
计算机根据生产工艺把相应的配方和生产工艺参数传递到PLC,PLC根据配方参数及下料顺序控制变频器启动配料工作,称重信号由PLC检测。配料工作顺序:称量完成后,当混合机内有料时,料斗称阀门关闭;当混合机放料关阀门到位后,料斗称阀门打开。料斗称开阀门时间到达后,检测料斗称上的余料,当余料超过限制值时,系统进行报警,料斗称阀门不关闭。当低于限制值时,料斗称阀门关闭。料斗称阀门关闭到位后,如果没有完成预定生产批次,配料继续,同时发出添加预混料和油脂添加信号。预混料添加并完成应答复位后,混合机开始混合计时,达到混合时间后,混合机根据缓冲斗的料位情况开阀门放料。混合机开阀门计时,开阀门时间到达后,混合机阀门自动关闭,等下一批料落下后,开始新一轮的循环。本配料系统采用模块化程序设计的方法,其中心思想是把一个复杂的应用程序按整体功能划分为若干相对独立的程序模块。本配料系统中,按程序完成的功能主要分为三个程序模块:
(1)送料模块按配方参数和进料次序完成各料反应釜的原料下料以及称重信号采集,保证各原料在允差范围内。加料停止后,从螺旋喂料器到料斗称之间还滞留一部分原料要落入料斗称中,需考虑这一部分物料,程序中用滞留量代表这个值。滞留量是根据企业生产经验数据,通过试验选择最优值确定。将变频器设置为多速段频率,用PLC的输出点控制变频器的频率。送料器配料时,PLC控制送料器电机在变频器高速段运行,当原料量逼近(给料量-滞留量)时,由PLC输出点控制送料器电机在变频器低速段运行,进行缓慢加料。加料过程中,PLC将原料量与(给料量-滞留量)实时比较,在允差范围内为合格,停止加料;接近允差下限,应进行变频器低速段加料;大于允差上限为超差,报警。
(2)阀门模块控制称重反应釜阀门按逻辑顺序开启和关闭,使当前批次的配料工作顺利完成。
(3)混合机阀门模块实现缓冲反应釜阀门和混合阀门的逻辑控制,使配料按设定时间完成混合搅拌。
在程序设计时,将整个程序分为几个功能模块分别实现,PLC工作时通过主程序分别调用各子程序完成相应功能。
4配料模糊控制与仿真
由于工艺参数、物料性质、落差等的变化,使配料系统的模型具有非线性和时变性。为改善落差等因素对精度的影响,可采用对落差进行预测和对配料量进行逼近控制,以改善配料精度。根据润滑液厂重复批量称量的特点,利用大量已有的称量误差数据对空间物料量进行模糊自适应补偿控制,可以保证物料误差在最小范围内波动。
4.1模糊PID的控制原理
配料控制器接收到来自主机的控制流量数据作为给定,与实际检测到的流量进行比较,通过模糊PID控制方法,计算相应的输出量(0~5V的电压或4~20mA的电流)来控制变频器,从而控制电机的转速,使所配原料流量达到给定的值。
5应用
配料生产线主要由监控屏、工控机、操作台、配电柜等组成。其功能包括以下几个方面:
(1)动态监控功能:可在屏幕上清晰显示液体灌装机的运行状态和物料流量。
(2)配方管理功能:技术配方存储在计算机中。在生产过程中,配方中确定了不同产品配料过程中的物料配比和投料顺序。因此,自动配料系统需要在生产前调用配方,自动计算和称量各种物料,并保持配比的准确性。
(3)自动配料、灌装和计量:灌装和配料是化工产品生产过程中最重要的工序之一,称为“喉部”工序。灌装和配料过程的质量对整个产品的质量起着重要的作用。在生产过程中,由配料系统控制的气动球可按配方实现自动计量和自动送料,保证产品质量稳定。
(4)混合速度控制:配料系统控制变频器控制混合速度,不同的物料可以以不同的混合速度混合,保证混合均匀。
(5)现场调整控制:可根据产品生产要求添加少量材料,实现现场调整。
6结束语
应用PLC技术对传统的润滑液配料现代化技术改造进行研究,制定了整体控制方案,结合称重模块技术、通信技术和模糊控制技术等相关知识,进行理论研究和实际论证,设计了一套以PLC为控制核心,由PC机和PLC组成的上下位机的系统。实践证明,该配料系统运行可靠,精度基本达到要求,完全适应企业现代化生产管理要求。