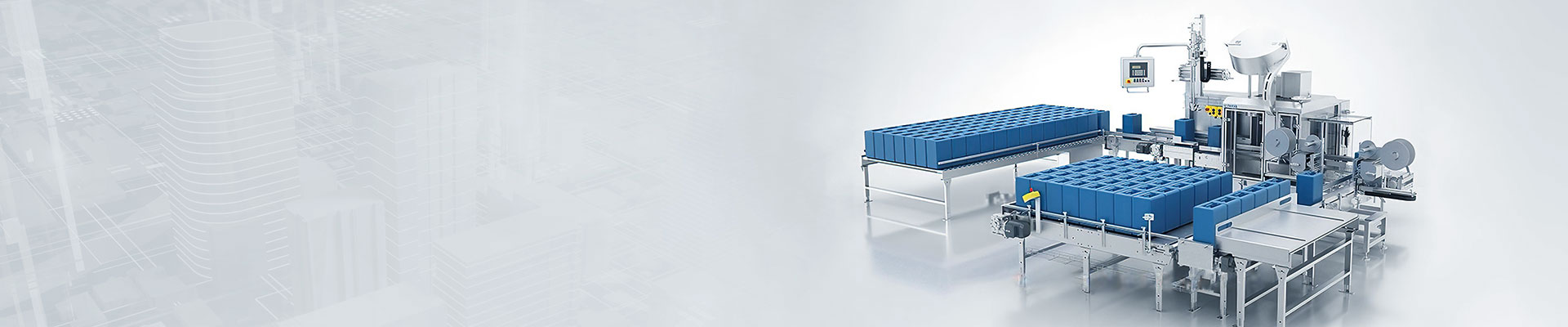
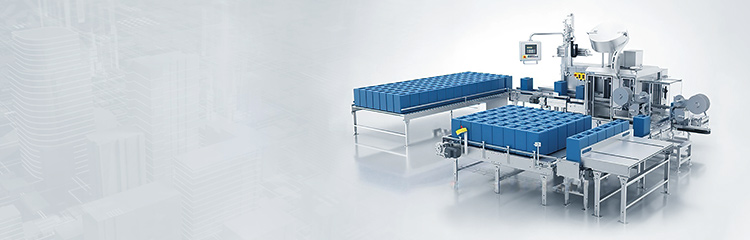
In addition to meeting the performance indicators required by the weighing instrument, the selection of weighing sensors should try to use sensors with consistent output sensitivity and input impedance, and connect them correctly in the wiring compensation box. The wiring compensation box shall be installed near the weighing instrument in the metering room.

The weighing module realizes signal acquisition, processing, control and output based on digital intelligent module, industrial control computer and RS485 field bus, which constitutes a weighing system with high cost performance. The communication between on-site monitoring computer and management computer is realized by LAN. The software is programmed with VC++ by modular method.
By adjusting the stress consistency of the sensor, the weighing module can reduce the influence of the problem of "static uncertainty" of the multi-fulcrum balance of the weighing platform and ensure the stability of the supporting of the weighing platform, so as to ensure that the bearing capacity of the center of gravity of the weighing platform does not deviate, and to ensure the accuracy of the weighing instrument and the relevant metering performance requirements. The weighing module has been compensated in many ways, including output sensitivity compensation.
Technical indicators
Rated load: 5/10/20/30/40/50/60/75/100/150/200/250klb.
Accuracy: C3
认证:OIML R60 C3,OIML R60 C4
Maximum verification score: max3000n
Minimum calibration score E:max/5000 v min
Comprehensive error: ≤ 0.030 (%fs)
creep:≤0.024(% FS/30分钟)
Effect of temperature on output sensitivity: ≤ 0.017 (%fs/10℃)
Influence of temperature on zero output: ≤ 0.023 (%fs/10℃)
Output sensitivity: 3.0±0.008(mv/v/v)
Input impedance: 700 7 (Ω)
Output impedance: 703 4 (Ω)
Insulation impedance: ≥ 5000 (50VDC) (mω)
Zero output: 1.0(%FS)
Temperature compensation range:-10 ~+40 (℃)
Permissible temperature range:-35 ~+65 (℃)
Recommended excitation voltage: 5 ~ 12 (DC) (V)
Maximum excitation voltage: 18(DC)(V)
Safety overload range: 120(%FS)
Limit overload range: 150(%FS)