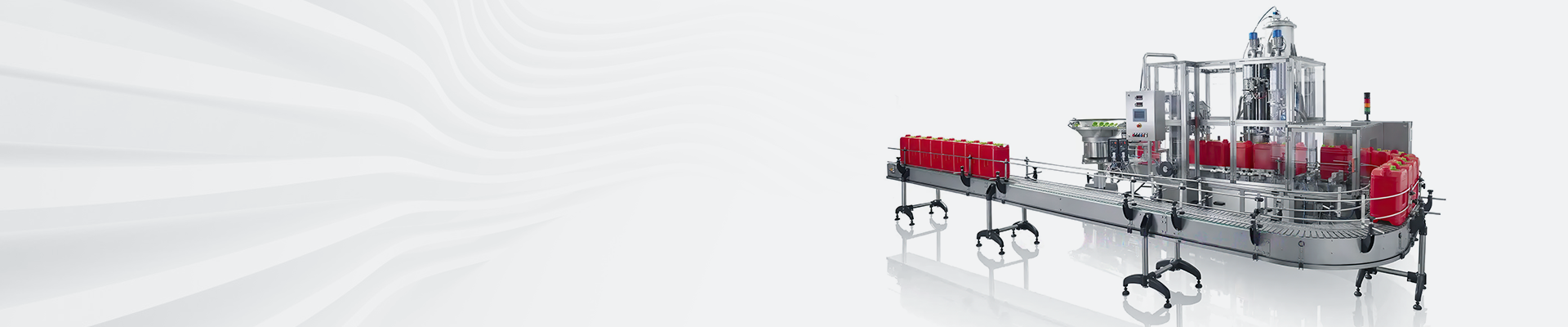
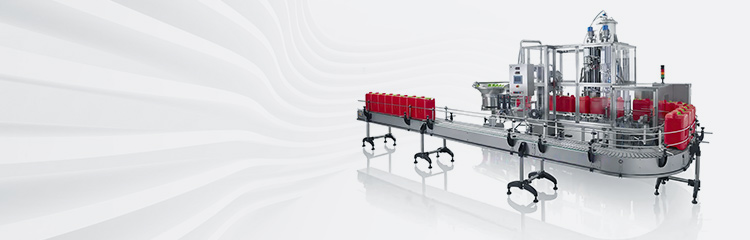

Summary:The batching system seamlessly forms a three-in-one metering system through the CC-Link fieldbus, together with PLC and HMI/IPC, to complete the mixing and feeding of different raw materials and logistics control, achieving integrated management and control, and optimizing the performance and efficiency of process control.
I. Overview
Fully automatic dosage system has been frequently used in various industries, such as: metallurgy, non-ferrous metals, chemical industry, building materials, food and other industries. Weighing and batching system is the first link in the production of finished products, especially in the industry with continuous material supply requirements, the process control of the ratio directly affects the quality of the finished product, weighing and batching system is a prerequisite for the enterprise to achieve the best economic benefits. Although the industry's different process characteristics of the dosage control requirements are different, but its high reliability, advanced, prescription, maintenance-free, scalable factory automation FA pursued by the same goal.
B. Functions of batching system
Based on the above objectives, the automatic dosage system designs and manufactures a set of fully automatic multi-species mixing and weighing three-electricity integrated dosage production line for an enterprise. The dynamic weighing scale, through the CC-Link field bus, together with PLC, HMI/IPC seamlessly form a trinity of metering and batching machine, in which the industrial control machine is connected to the factory ERP/MIS through HUB and Ethernet TCP/IP. the whole batching process is carried out strictly in accordance with the selected formula ratio and process, and there are multi-stage alarm records to complete the mixing of different raw materials to feed and logistic control, realizing the integration of management and control, and optimizing the batching process. It realizes the integration of management and control and optimizes the performance and efficiency of process control.
Third, weighing and batching system CC-Link Overview
Weighing and batching system CC-Link is Mitsubishi Electric to high-performance, low-cost, multi-vendor support for the goal of the second generation of open fieldbus launched in 1996, is control & communicationLink (control and communication link) short, in November 2000, CC-Link Association was established, specifically responsible for CC-Link in the world's The CC-Link Association was established in November 2000 and is specifically responsible for the popularization and development of CC-Link worldwide.
The open fieldbus CC-Link has outstanding advantages such as excellent performance, wide range of applications, simplicity of use and cost savings. CC-Link for metering and dosage system adopts master-slave structure with twisted pair cable as connection medium, supporting up to 64 slaves and adopting broadcast polling mode, which can reach up to 10Mbps. PLC or computer as CC-Link master, with AJ65SBT-RPT repeater, the maximum distance can reach up to 13.2 kilometers. The maximum cyclic data capacity of the network bus is 2048 points, 512 words; the maximum instantaneous data transmission is 960 bytes.CC-Link has complete RAS functions such as reservation station function, automatic refresh function, plug-and-play function, and hot standby of master station, detachment of sub-station, station on-line reply, monitoring and testing, etc. In the use of CC-Link, the hardware switch setup, wiring (3-core shielded wire) CC-Link is very convenient and easy to use for hardware switch setting, wiring (3-core shielded cable) and dosage system configuration (parameter setting is sufficient).
At present, CC-Link supports up to 360 kinds of devices, such as remote I/O, sensors, weighing controllers, regulators, solenoid valves, frequency inverters, touch panels, etc. It is supported by more than 220 manufacturers. CC-Link is also supported by more than 220 manufacturers, such as Panasonic, Yokogawa, Siemens, SMC, DIGITAL, NEC, etc. CC-Link is also the only Asian product that can compete with European and American fieldbus standards.
Fourth, the mixing system configuration
This vehicle weighing and mixing machine lower unit adopts Mitsubishi Electric's MELSEC-A2SHPLC as the main control, and with Mitsubishi GOT touch screen as the lower human-machine interface (HMI), metering control by 12 sets of weighing company's CFW quantitative feeder composition. The frequency converter is connected through CC-Link field bus to realize data acquisition and control to ensure the reliability and real-time dosage. The upper computer part selects Advantech IPC610 industrial computer as the monitoring station, with MSWindowsNT4.0forworkstation to operate the dosage and Syatech monitoring software Version5.30 as the running environment, the dosage software has rich functions of process operation, monitoring, communication, alarm, management, trend, record and man-machine dialog, and has strong diagnostic ability. The hardware and software of the speed control system is the organism of controlling the dosage, the above configuration ensures the dosage integrity, consistency, compatibility and complete set, adapts to the long-term stable operation in the industrial environment, and has the ability of electricity, magnetism and vibration anti-jamming to satisfy the safety requirements.
The mixing system structure and network configuration
1, the lower computer structure and composition
In this mixer used in the 12 CFW is mainly to complete the raw material flow control, which weighing instruments, set of regulation and calculation as one of the multifunctional weighing controller, weighing instrumentation design technology embodiment, with sufficient anti-interference performance, diversified interfaces, self-diagnostic function, self-tuning PI adjustment function and other features, and with the Mitsubishi A540 current vector type frequency converter and SEW high-performance motor It is composed of a complete electromechanical integration product, which ensures the accuracy of measurement and control (?3‰ precision) and guarantees the constant ratio of instantaneous flow between 12 CFWs.
The lower computer selects CC-Link fieldbus control mode, with Mitsubishi MELSEC-APLC a total of two CC-Link dual-machine redundancy structure, with advanced, high-speed, reliable, large-capacity features, of which PLC1 is the main control, PLC2 for the backup redundancy, when the communication failure occurs, it can be practiced between the main and backup PLC non-perturbative switching. Since the 12 CFWs are distributed in a decentralized way, the CC-Link bus is chosen to connect the weighing controller directly with the PLC. The lower human-machine interface (HMI) is Mitsubishi Electric LCD touch screen GOT to ensure that the process data are correctly and timely in the upper PC monitoring station and the touch screen to get a double response and display, even if the upper failure or failure, it does not affect the whole process control. Although the monitoring screen of the touch screen is not as rich as the upper HMI, it basically covers the monitoring and operation of the whole dosage.
The quantitative feeder (CFW) is connected to the CC-Link fieldbus as a remote device slave.
The PLC control software is written in symbolic ladder diagram, and gives full consideration to the resources of the batching system, reduces the cycle scanning time, and improves the real-time controllability. PLC1 is the CC-Link master, and the master module controls the slave's operation and the data refreshment, because A2SHPLC supports the CC-Link instruction, which makes it easier to make the network configuration and the data processing, and the data exchanges between master and slave are automatically linked and updated in the running program. In the running program, the data exchange between master and slave is automatically linked and updated, and the master CPU only needs to exchange the device information with the slave through the RDGET and RDPUT statements. The CC-Link instruction can replace the FROM/TO instruction to handle the data access without caring about the address of the buffer memory.
Modbus communication protocol (RS485 mode) is selected for communication between upper and lower computer, the network structure is master-slave structure, the communication medium is twisted pair, which is widely used in industrial control field and is the de facto industrial network standard. The measurement supports 21 function codes and can communicate with different products of its many manufacturers in the factory. Modbus protocol used in this system is encapsulated in RTU format, can be higher baud rate to transmit information.
2、Monitoring system details
Monitoring system is based on the system V5.3032 bit industrial control software for the development and operation of the platform, is based on the WindowsNT platform for distributed control of SCADA software, to provide users with great application flexibility and mixed dosage system prescriptive, in the field of industrial automation has a wide range of applications, is one of the outstanding automation software.
The weighing system has a built-in Cicode real-time multitasking SCADA program language, and by using the rich function library provided by weighing and measuring, complex applications can be developed flexibly, which is one of the features of the system superior to its SCADA software. The monitoring system adopts a tree structure, with a variety of screen call means, in order to facilitate the operation of the use. The screen is divided into menu homepage, dosage overview monitoring, equipment monitoring, recipe management, trend group record, alarm group record, report, operation log, debugging maintenance, help and other screens. In order to ensure the safe and reliable operation of the dosage, the monitor provides three kinds of privileges: operator, administrator and engineer to ensure the safety mechanism of the dosage. In the development of this monitoring system, combining the actual process conditions and making full use of the specialties of dosage, it mainly accomplishes the functions of recipe setting, process selection and switching, process interlocking, process starting, sequence stopping, fault stopping, process alarming, flow rate and dosage control, and cumulative statistics.
The automatic mixing system adopts a C/S structure, in the form of an input/output server (I/Oserver) connected to the factory ERP/MIS via an Ethernet link (TCP/IP protocol). The dosing system provides a common method of realizing Windows-based data exchange between applications and I/Os based on DDE/NetDDE, OPC, ODBC/SQL, COM/DCOM, CTAPI, and so on. The dosage system provides common methods such as DDE/NetDDE, OPC, ODBC/SQL, COM/DCOM, CTAPI, etc. to exchange data between Windows-based applications and I/O. The historical data in this dosage system is accessed by ODBC/SQL to the database server MicrosoftSQLServer 7.0, and for the real-time data exchange, considering the instability and limitation of DDE and OPC, the CTAPI interface provided by the dosage system is chosen, which is suitable for a variety of data exchanges, and it is more flexible in use, avoids the redundancy of code in the application programs, and improves the memory utilization, and it is more flexible in use. The DLL function provides external application (VB, VC, etc.) interface, so that the user application can directly operate the Tag variables of the dosage system and support remote operation through TCP/IP. VB calls the DLL function according to the principle of first declaration and then call, and the use of the DLL function is similar to the application of VB's own function, which is very simple. It allows users to monitor real-time data and query historical data through any workstation on the internal corporate network.
V. Conclusion
To summarize, the dosing system composed of open mode fieldbus CC-link based quantitative feeder CFW with PLCPC and industrial control software has the characteristics of advanced, open mode, short implementation cycle, low cost (including investment, maintenance, upgrading and other costs), etc. It can be seamlessly combined with different types of products from different companies and based on the integration of network platform technology to The need for safety, transparency and economy is realized. Among them, fieldbus and industrial control software are the mainstream and hotspot of automation development in the next few years, and it is believed that they will be used more and more in various industries.