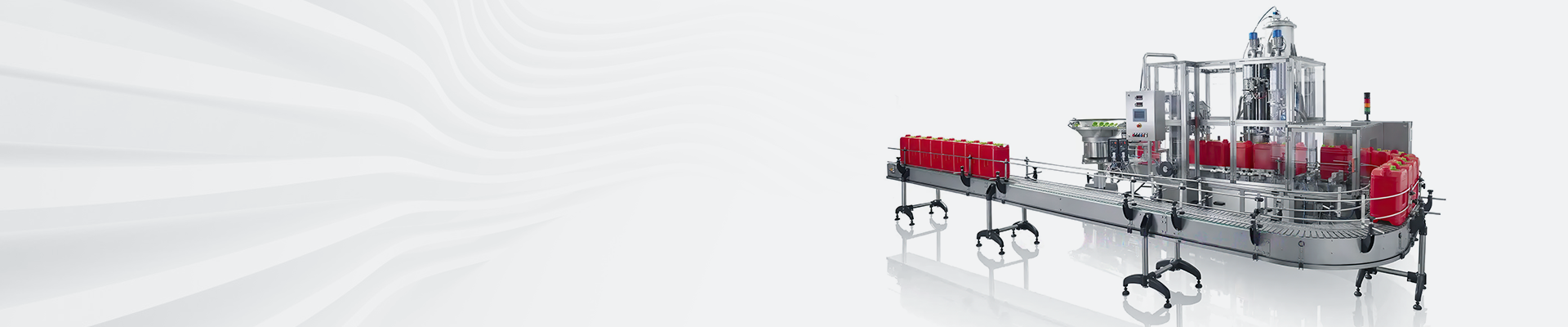
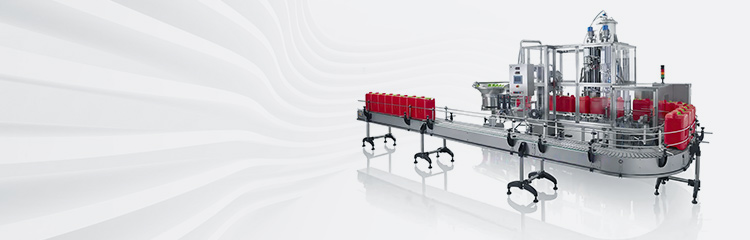

Summary:The batching system adopts the speed-adjustable belt scale metering control method to set the feeding cycle, achieving deviation-free control.In order to achieve remote control, Newton 7000 series remote data modules and industrial computers were selected.
In the dosage system of polyurethane production process, a large number of electronic belt scales are used to measure and control the amount of material discharged. Due to the variety of material composition and shape, polyurethane production site environment and other reasons, the belt scale metering control system has nonlinearity, inertia, hysteresis and randomness and other shortcomings, in the actual control application, it is difficult to establish its accurate mathematical model, with the traditional PID control method can not be a good solution to these problems. And the debugging control theory based on language rule model is an effective way and method to solve the above problems. The overall control of the batching system is carried out by adopting industrial control machine and Newton 7000 series module, on the basis of which, the debugging control strategy is introduced to control the various proportioning components, and the control effect has been proved to be very satisfactory in practice. The quality of polyurethane production provides a reliable guarantee, with obvious economic benefits.
1 Mixing system metering and control methods
The key to ensure the quality of the dosing control system is that the materials are dosed strictly according to the ratio, and the proportion of each material comes from the weighing volume of the belt scale, whether the measurement of the belt scale is accurate or not has become a key factor affecting the quality of polyurethane.
The common measurement method is flow calculation, i.e., integrating the product of weighing module signal and belt running speed, which has a large calculation workload, complicated flow control, poor stability, and the calibration of the belt scale is very troublesome, which requires the calibration of large materials in kind, and the error is large.
On the basis of repeated experimental research, a quasi-static direct weighing method, set point A for the lower material point, point B for the material point, from point A to point B of the running time for the belt cycle T (generally about 10s, for known quantities and pre-set), the material flow of the integral time of T, the load cell signal directly corresponds to the weight of the material in each weighing scale, the advantages of this method is simple and convenient operation, and calibration This method has the advantage of simple and convenient operation, and the calibration is only static calibration by hanging the code, instead of the complicated dynamic flow calibration of the actual large materials (from several tons to tens of tons).
Frequency conversion feeding system adopts speed control belt scale measurement and control mode to set the feeding cycle T, to realize the non-deviation control.
2 Weighing and batching mechanism into
Polyurethane plant environment is harsh (high dust, noise, high temperature, high electromagnetic interference, etc.), in order to realize the long-distance control, selected the Newton 7000 series of remote data modules and industrial computers to complete. Newton 7000 series module using RS485 mode of communication, the system can be linked only with a twisted pair of wires, which has a high communication rate, high sampling resolution, intelligent, optoelectronic isolation, strong anti-jamming and dual-watchdog design, so that the system has high reliability, data high-speed I / O possible, software development is also relatively easy. And the host uses RS232 communication port to connect with the network, basically any computer with RS232 can use this network, equipment interchangeability is good, the difficulty and workload of maintenance personnel is also very small.
3 debugging dosage
Quantitative batching system in the process of error-free control, if the deviation is not corrected (compensation), will lead to imbalance in the ratio, a large number of waste materials, resulting in losses. In order to ensure that the mixing and dosage system error-free and good dynamic indicators, the system will be the error of the integral and differential quantities as the input of the debugging controller. The output of the commissioning controller is the correction of the control value, the direct control quantity calculated from the given, the correction quantity is converted by D/A output to control the discharger. The input variables of the dosage debugging controller are deviation integral and deviation differential, and the output variables, its corresponding language variables, are established on the basis of the manual operation experience to establish the debugging control rules stored in the knowledge base, and the control rules are provided for the reasoning machine during the debugging inference.
As the controlled object can only receive a precise digital control volume, can not receive debugging control volume, must be clarified (signal filtering conditioning) interface, the debugging volume is converted into a precise volume, the precise volume multiplied by the scale factor, and then through the D / A conversion output down the material controller. The debugging judgment method in this system adopts the weighted average method:
4 debugging dosage test
Measurement of the dosage system using Matlab in the fuzzy toolbox and Simulink toolbox on the dosage debugging control system for experimental research, dosage debugging generator simulation to generate the downstream deviation, in this case the simulation generates sinusoidal fluctuations in the error.
The value of the affiliation function of each element in the debugging domain is adjusted, taking into account the randomness of the fluctuations in the amount of material discharged, and in order to obtain good steady-state and dynamic indicators, the resolution at element 0 is taken to be low, and the resolution at element 6 is taken to be high. Using Matlab/Toolboxs/Fuzzylogic/FIS to calculate the control volume lookup table, after repeated adjustment of the quantization factor and scale factor, the underfeeding debugging control test curve can be obtained. From the test results, it can be seen that: using the debugging control mode, the system can quickly compensate for the deviation generated by the previous control cycle. After practical application, it also verifies that the system is characterized by small overshooting amount and strong robustness. For the polyurethane production line metering dosage, a quasi-static metering method is proposed, and the debugging control strategy is adopted to achieve good control results. Since the automatic dosing system for polyurethane production line researched in this paper has been put into operation in the raw material and clinker production lines of several small and medium-sized polyurethane factories, it has greatly improved the quality of polyurethane production, increased the output and reduced the energy consumption, and at the same time, it has also reduced the labor intensity of the workers, and improved the automation level of the polyurethane production and the level of production management. The system has obvious economic and social benefits, as well as high value of popularization and application.