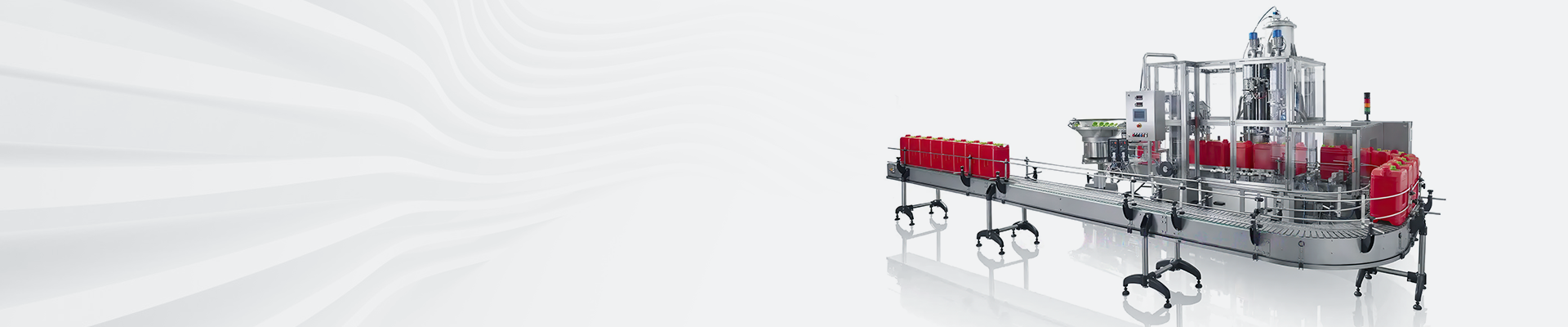
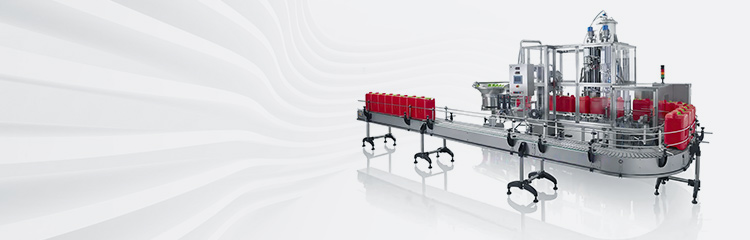
摘要:配料系统采用调速皮带秤计量控制方式设定下料周期,实现了无偏差控制。为实现远距离控制,选用了牛顿7000系列远端数据模块和工业计算机来完成。
在聚氨酯生产过程配料系统中大量采用电子皮带秤来计量和控制物料下料量。由于物料成分及形状多种多样、聚氨酯生产现场环境恶劣等原因,皮带秤计量控制系统具有非线性、惯性、滞后性和随机性等缺点,在实际控制应用中,很难建立其精确的数学模型,用传统的PID控制方法不能很好地解决这些问题。而以语言规则模型为基础的调试控制理论却是解决上述问题的有效途径和方法。采用工控机和牛顿7000系列模块对配料系统进行整体控制,在此基础上,引入调试控制策略对各种配比成分进行控制,实践证明控制效果非常理想。对聚氨酯生产的质量提供了可靠保证,具有明显的经济效益。
1混合系统计量和控制方法
配料控制系统确保质量的关键是物料严格按配比配料,而各物料的配比量来自皮带秤的称料量,皮带秤的计量是否准确就成了影响聚氨酯质量的关键因素。
常见的计量方式为流量计算,即对称重模块信号和皮带运行速度的乘积进行积分,这种方式计算工作量大、流量控制复杂、稳定性差,并且皮带秤的标定很麻烦,需要大物料的实物标定,且误差大。
在反复试验研究基础上,采用了一种准静态直接称重法,设A点为下料点,B点为出料点,从A点到B点的运行时间为皮带的周期T(一般10s左右,为已知量并且预先设置),物料流量的积分时间为T,称重传感器信号直接对应每一秤物料的重量,这种方法的优点是运算简单方便,而且标定时只需挂码静态标定,而非繁琐复杂的实际大物料(几吨至几十吨)动态流量标定。
变频投料系统采用调速皮带秤计量控制方式设定下料周期T,实现了无偏差控制。
2称量配料机构成
聚氨酯厂环境恶劣(高粉尘、噪音、高温、高电磁干扰等),为实现远距离控制,选用了牛顿7000系列远端数据模块和工业计算机来完成。牛顿7000系列模块采用RS485方式通讯,系统只需用一条双绞线即可联结,其具有的高通信速率、高采样分辨率、智能化、光电隔离、强抗干扰和双看门狗设计,使系统可靠性高,数据高速I/O成为可能,软件开发也比较容易。而且主机使用RS232通讯口与网络连接,基本上任何一台有RS232的计算机都可使用此网络,设备互换性好,维护人员的工作难度和工作量也很小。
3调试配料
定量配料系统在无误差控制过程中,如果偏差没有纠正(补偿),将导致配比失衡,出现大量的废料,造成损失。为保证搅拌配料系统的无误差及良好的动态指标,系统中将误差的积分量和微分量作为调试控制器的输入。调试控制器的输出为控制值的修正量,由给定计算出的直接控制量,修正量经D/A转换输出控制下料器。配料调试控制器的输入变量为偏差积分和偏差微分,输出变量,其相应的语言变量,在手动操作经验基础上建立调试控制规则存放于知识库中,在调试推理时为推理机提供控制规则。
由于被控对象只能接收一个精确的数字控制量,无法接收调试控制量,必须经过清晰化(信号的滤波调理)接口,将调试量转换成精确量,精确量乘以比例因子,再经过D/A转换输出下料控制器。本系统中调试判决方式采用加权平均法:
4调试配料试验
计量配料系统利用Matlab中的fuzzy工具箱和Simulink工具箱对该配料调试控制系统进行试验研究,配料调试发生器模拟产生下料偏差,本例中模拟产生正弦波动的误差。
调整调试论域中每个元素的隶属函数的值,考虑到下料量波动的随机性,为得到良好的稳态和动态指标,元素0处的分辨率取低,元素6处分辨率取高。利用Matlab/Toolboxs/Fuzzylogic/FIS计算出控制量查询表,经过反复调整量化因子和比例因子,可以得到下料调试控制试验曲线。从试验结果可以看出:采用调试控制方式,系统能快速补偿上一控制周期所产生的偏差。经过实际应用,也验证系统超调量小、鲁棒性强的特点。针对聚氨酯生产线中计量配料,提出一种准静态计量方式,采用调试控制策略,取得良好的控制效果。本文研究的聚氨酯生产线自动配料系统在数家中、小聚氨酯厂生料、熟料生产线上投运以来,大大提高了聚氨酯生产质量,增加了产量,降低能耗,同时还减轻了工人劳动强度,提高了聚氨酯生产的自动化水平和生产管理水平。系统具有明显的经济效益和社会效益,以及较高的推广应用价值。