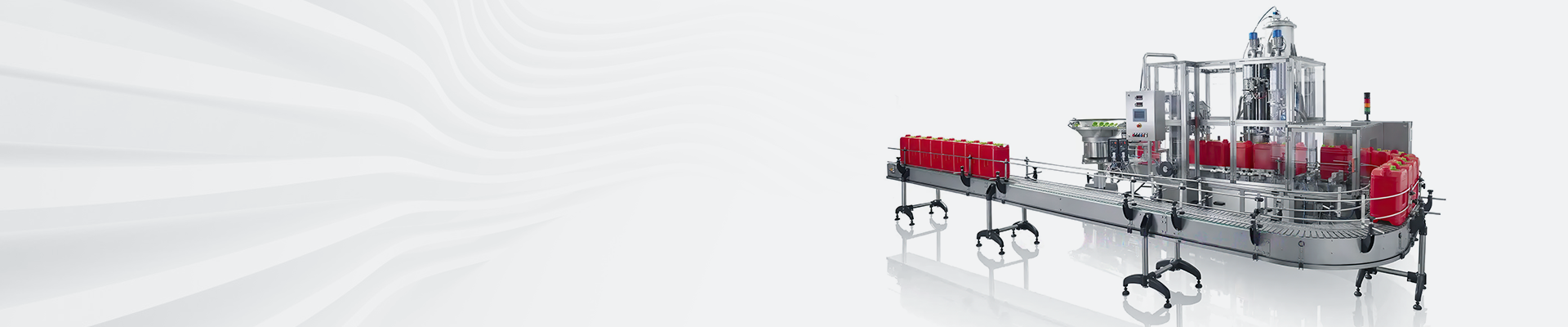
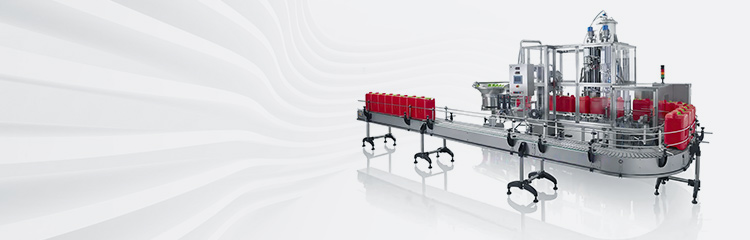

Summary:The weight signal of the weighing module of the on-site weighing hopper obtained by the batching system is directly sent to the S7-315DPCPU storage area through the backplane bus of the PLC. The host computer and the weighing module can easily exchange data through bus communication.
At present, domestic refractory manufacturers in the batching process, most of the use of weighing instruments with PLC programmable controllers to achieve automatic weighing and control functions. Weighing instrument and PLC control system need to transmit a large number of real-time data and control interlock, communication and control circuit wiring is more complex, weighing and batching control signal is prone to hysteresis, weighing and batching maintenance is larger.
The production management system is usually developed by VB or VC programming, which is more complicated. Manufacturers of the dosage process and demand for change, but also increased the system development and maintenance costs.
Second, the requirements of refractory batching
A foreign company in China to establish a refractory factory, the refractory products produced by the factory are mainly for export, part of the products for domestic use. The refractory material batching system is divided into two categories: indeterminate refractory material and CCN refractory material. Indefinite refractories are divided into acid-neutral refractories and alkaline refractories, and CCN refractories are divided into AG and ZG.
Indeterminate refractories are widely used in smelting blast furnaces, etc. Among them, acid-neutral refractories are composed of about 35 kinds of raw materials according to different weight ratios. Alkaline refractories are composed of about 14 kinds of raw materials in different weight ratios. Indeterminate
CCN refractories are mainly used in the production of continuous casting three big parts, of which AG consists of about 22 kinds of raw materials according to different weight ratios. zg consists of about 10 kinds of raw materials according to different weight ratios. the structure of CCN batching system is shown in Fig. 2:
The number of user formulas is relatively large compared to the number of materials to be dosed, reaching hundreds of types. At the same time, the quality control link in the production process has a strict testing procedure within the refractory dosage system, once the weight value of a certain material exceeds the percentage allowed for dosage qualification, a fault-tolerant procedure is initiated to replenish the material. If the replenishment also fails to meet the requirements, a batch of materials will all automatically enter the scrap bin, resulting in the loss of raw materials. Therefore, the user puts forward high requirements on the stability and reliability of the system.
Due to the confidentiality of the refractory formula, the user has put forward extremely strict requirements on the high confidentiality of the formula in the production process. In the preliminary technical exchanges, the user especially emphasized to avoid understanding the composition of the formula through the type of material, the weight data of the weighing instrument, the ratio and other aspects.
Some imported raw materials are of high value, for example, the price of finished product made of 100Kg of CCN can be tens of thousands of RMB. In order to improve production efficiency and reduce production costs, the weighing control system is required to have a high degree of accuracy.
SIWAREXFTA weighing and batching system
Siemens PLC has many users in China, and its reliability and stability are recognized by users. Considering the high precision of weighing and batching and the reliability of the control system as well as the confidentiality of the refractory formula and other requirements, Siemens PLC controller and SIWAREXFTA weighing module are selected in the weighing and batching system.
1.SIWAREXFTA weighing extension module
SIWAREXFTA weighing module, as an extension module of high precision weighing function in Siemens S7PLC, can be directly integrated in Siemens S7-300 PLC system, unified hardware and communication with PLC, with weighing accuracy as high as 0.05% and index value as high as 3×6000 d. When replacing the FTA weighing module, there is no need to re-calibrate hopper scale. With precise and fast digital output for loading/unloading control (response time <1ms), it can be applied to most of the high precision weighing control applications.
2. Dosing Configuration
The whole production process is divided into 4 relatively independent weighing systems. Introducing the acid-neutral weighing system, which has 40 weighing bins, using 7 SIWAREXFTA weighing modules integrated into a single S7-315-2DPCPU, which is connected to the upper computer system within the system via ProfibusDP bus.
Each bin is supported by three load cells, which are connected to the FTA module through a junction box. The upper computer system downloads the formula to the weighing module through Ethernet, and the weighing module controls the feeding and discharging process of each weighing bin according to the preset value of the formula, and monitors the operation of each equipment on site in real time, providing abundant alarm and diagnostic information, and forming a record of historical data for the efficiency of the plant operation and the analysis of accidents.
3.Batching characteristics
The batching control system is based on the electronic weighing of the original sensor combined with the Philips PR1713 weighing instrument, with the S7-300 PLC produced by Siemens as the control core and equipped with the industrial control computer of Taiwan Advantech, and with the PROFIBUS field bus communication of Siemens combined with the existing peripheral equipment to complete the automatic control of the whole process of batching, conveying, and mixing, which is from the outlet of the silo to the outlet of the mixing machine. The whole process of mixing is automatically controlled.
The dosage machine displays and monitors the alarms and interlocks of the whole system, and accomplishes the recipe management, production data management, equipment operation status management, and man-machine dialog for commanding the production to meet the production requirements for the dosage of the mixture. Automatic and manual recipe control of the mixture; automatic control of subsequent equipment startup and shutdown; pre-diagnosis of possible failures; automatic monitoring of the working condition of the equipment, when the need for technical maintenance, to remind the operator in advance; automatic generation of daily, weekly, monthly and yearly reports, record the total consumption of raw materials and so on. The automatic establishment technology not only shortens the development cycle of the project, but also saves a lot of manpower; according to the conventional practice, if there is no automatic establishment technology of the project, the development cycle of this system will be greatly lengthened. As the software report using the extended HTML language compilation, not only suitable for storage, printing, but also supports the report of the online publication, in line with the requirements of the network era, for the dosage retains the future expansion of the interface; dosage contains more than 150 kinds of process control and data processing algorithms, it is a kind of control function is very powerful software, suitable for solving the application of the occasion containing a complex control program requirements, at the same time The dosage HMI development environment provides a rich set of graphic tools, support for AVI video files and unique animation technology.
As the weighing and feeding machine is equipped with more kinds of materials, and each screw feeder has multi-stage feeding speed control, the screw feeding port is equipped with pneumatic valves to control the precise feeding, and some of the discharging devices adopt multi-stage vibrating feeders and micro scales, etc., and the whole system has about 2,000 I/O points. In the system of automatic dosage, in order to control the influence of silo pressure change on the dosage accuracy, the dosage and the above silo automatic dosage system have the corresponding interlocking control relationship. Siemens SIWAREXFTA weighing module will weighing function directly integrated into the S7-300PLC, plus FTA module itself integrated 16 switching I/O points and a 4-20mA analog output function, can easily realize this more complex weighing and dosage applications.
1) Transmission of weighing data
The signals from the load cell on site are fed directly into the PLC system instead of the 4-20mA signals from the normal weighing instrument, avoiding the errors and time delays caused by signal conversion. The real-time data of weighing control is high, the speed of updating weighing data is faster, and the control accuracy is higher.
2) Communication ability
SIWAREXFTA has a unified communication interface with Siemens SIMATIC, and the weight signals of the hoppers obtained by the 19 SIWAREXFTA weighing modules are sent directly to the S7-315DPCPU storage area through the PLC backplane bus. The host computer and the weighing modules can easily exchange data by means of bus communication. Since the weighing system and the control system are on a unified hardware and software platform, this type of data exchange transmits a larger amount of data, at a faster speed and with good real-time performance.
3) Easy maintenance
When programming with the SIWAREXFTA weighing module, using one of the FB41 programs and routines provided by Siemens, it is possible to read the various weighing process values directly in the CPU memory of the S7-315, which can be easily programmed and set up according to the requirements of the process interlock.
Each SIWAREXFTA module is interchangeable. Since all the setup and calibration parameters are present in the S7-300 CPU, replacing the FTA module eliminates the need to re-calibrate the weighing hopper. all the FTA bin setup and calibration parameters in the CPU can also be backed up on a MMC card or a computer for quick data recovery in case of system 4) failure.
For on-site commissioning and calibration, Siemens provides a dedicated SIWATOOLFTA program based on the Windows operating system. This enables technicians to easily set up and commission scales without knowledge of PLC programming.
6) Confidentiality of recipes
All production process recipes are stored in the PLC with a code number and a protection password. The modification and maintenance of the recipe is managed by a person. The operator only needs to select the formula number and confirm, the weighing and batching system automatically executes the batching production process according to the formula and the feeding time sequence.
Conclusion
The refractory factory was put into production at the end of 2006, the system has been running well, the weighing accuracy of SIWAREXFTA weighing and batching system is better than OIML Ⅲ, the control accuracy of weighing and batching can reach ±3 ‰, the control accuracy of a small amount of special materials and micro-scale can reach ±5 ‰, which fully meets the user's production requirements.