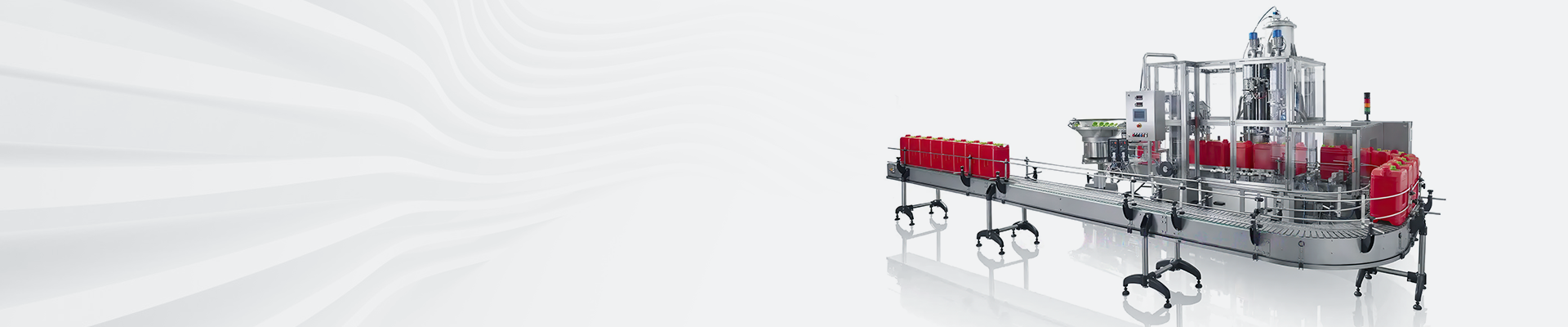
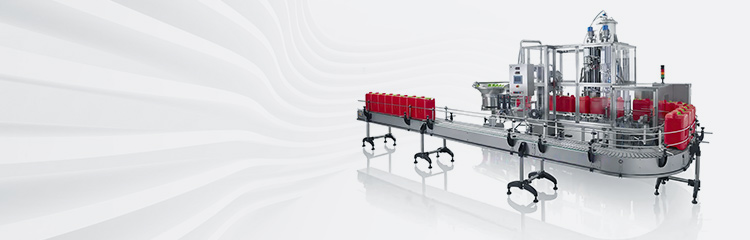

Summary:When the liquid filling machine lifts the piston, the material is sucked into the piston cylinder from the upper oil tank by valve control, and then capping, carton sealing, palletizing and corresponding conveyor belts are performed. The servo motor performs positioning supplemented by automatic control and automatic adjustment systems. .
Automatic filling machine PROFTIBUS-DP network is a PROFIBUS system consisting of three masters and seven slaves, three masters constitute a token logic ring, when a master gets a token message, the master can be executed within a certain period of time the work of the master. During this period of time, you can communicate with all the slaves according to the master-slave communication relationship table, or you can communicate with all the masters according to the master communication relationship table.The programming interface and data viewing interface in TEP7 provide both offline and online views. The offline view shows the contents of the PO locally stored items and the online view shows the actual contents in the CPU. When the PC is connected to the PLC through the programming cable, an online connection can be established in STEP7.
The Liquid Filling Machine collects data sent in the form of digital quantities from field devices, and realizes monitoring and control functions by operating on real-time data. A real-time database is provided to help monitor the production process. The equipment screen with real-time updated data display also provides a large screen showing the entire operation process, making it easy for you to observe the entire production process. The data displayed includes operation mode, weight, totalized quantity, set point, deviation and other similar data.
The weighing and filling machine monitors all kinds of filling equipments of the whole production line, and you can directly observe the operation status of all the production equipments related to the weighing system on the control CRT. The screen is equipped with animation indication function for the motors and other moving equipments, and it realizes the drawing of historical curves, which allows you to dynamically add/delete curves on-line, infinitely zoom in/out of the curve charts, dynamically compare curves, and print curves, etc. The history curve drawing is realized. Process parameters such as temperature, pressure, flow, etc. are recorded. In the lower PLC program fault alarm, the operator interface can be seen in the total fault alarm becomes red and flashing, the buzzer in the hardware circuit produces an alarm bell. Generate an alarm automatically switch to the fault analysis interface, directly see the cause of the alarm.
Liquid filling scales on the weight of the barrel identity data collection for the host computer database for barrel identity and regulation identification, based on the EPC passive chip inductance coil and other components, through the external LC circuit to receive R signals from the read-write, through the chip's internal power supply circuit processing to provide power for the chip, through the chip's internal damping load, the data in the on-chip EEPROM is read into the read-write and special way to interrupt the RF field, so that the read-write can read the data in the chip and the data in the chip are read into the read-write, and the read-write is interrupted in a special way. The data in the on-chip EEPROM is read into the reader-writer, and the RF field is interrupted in a special way, so that the reader-writer can write the data into the on-chip EEPROM. The reader-writer data is uploaded to the recording server. The appropriate part of the barrel is pasted with an electronic label, when the barrel is put on the weighing platform, the RF reader will be aligned with the electronic label part, start the reader to read the ID code of the electronic label, and then take out the ID number of the bottle from the reader and upload it to the microcontroller, which will then upload the data to the upper PC to enter into the database of gas cylinder information. the ID number will be queried and compared in the database, and at the same time, a code will be returned to the microcontroller. On one hand, the microcontroller returns a signal to the reader to close the reader, on the other hand, the microcontroller carries out the relevant control operation of gas filling according to the program settings.
The automatic filling machine has high utilization rate and the production is flexible and can adapt to the production changes. When the market demand or design changes, there is no need to change the system hardware structure, the equipment has the flexibility to produce different products. Versatility with CNC fast conversion design is easier to realize in the small packaging production line. Various types of packaging replacement is relatively fast, the market demand triggered the development of multifunctional filling machine. Fast conversion is still basically two ways, some parts do not need to use tools to achieve fast changeover, such as filling the star wheel and guide plate; the other such as filling cylinder lifting, labeling machine, cartoner and palletizer adjusted by the PLC control of a number of servo motors running to adjust to the desired position. Whether an automatic filling production line should have the function of fast conversion, easy to realize the more economical fast plug conversion. Bottles with large changes in the external dimensions of the bottle, it is necessary to have another consideration. For example, a frequency conversion speed to use the diameter of 50mm and diameter 150mm two types of bottles, the general small specification