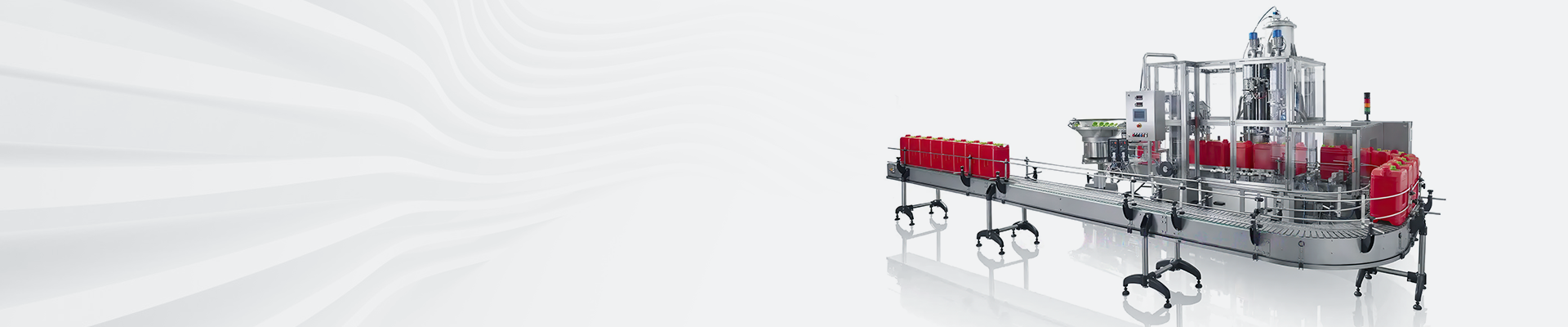
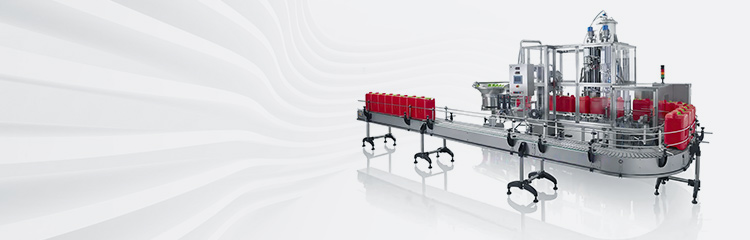

Summary:In the wireless solution, the liquid filling machine uses infrared applications of AS-I and PROFIBUS, valve position and glass bottle positioning sensors for coding and positioning, and fills according to the set filling capacity. When the set value is reached, the filling valve is closed. Enter the bottle conveying chain at the bottle outlet to complete the filling tasks of each station.
I. Introduction
With the continuous development of science and technology, wireless technology has been widely used in many fields. In the field of liquid filling machine, wireless technology is also changing the filling of the way of working, improve efficiency, improve equipment performance. This paper will focus on the application of wireless technology in liquid filling machines, including remote monitoring, real-time data recording, fault diagnosis, real-time adjustment of control parameters and mobile device management. With the development of network and technology in the direction of more and more broadband, the mobile communications industry will move towards a truly mobile information age. On the other hand, with the rapid development of integrated circuit technology, the processing capability of mobile terminal has already possessed a powerful processing capability, and the mobile terminal is changing from a simple talking tool to a comprehensive information processing platform, entering the stage of intelligent development, with an open operating system platform, supporting flexible development, installation and operation of application programs; with a PC-level processing capability, supporting the migration of desktop mainstream Internet applications to mobile; with a high-speed Internet application, supporting flexible development, installation and operation of application programs. With PC-level processing capability, it can support the migration of mainstream desktop Internet applications; with high-speed data network access capability and rich human-computer interaction interface, it also adds a broader development space for mobile terminals.
Second, remote monitoring
PLC wireless intelligent filling system and its application, the filling machine includes a mobile terminal, a wireless information transmission module and a PLC controller, the mobile terminal is wirelessly connected to the PLC controller through the wireless information transmission module, and the PLC controller is connected to the signal of the controlled equipment, and the mobile terminal includes an equipment operation mode selection module and an equipment operation mode setting module, the equipment operation mode selection module is used to select the operation mode of the The mobile terminal includes a device operation mode selection module and a device operation mode setting module, the device operation mode selection module is used to select the operation mode of the device, the device operation mode setting module is used to set the operating condition of the device in the operation mode of the name of the mechanism; the PLC controller is set with a device operation mode program module, and the device operation is controlled by the operation program. Utilizing very popular mobile terminal equipment, the wireless intelligent control of PLC is realized through Bluetooth or WIFI wireless information transmission technology, so as to achieve intelligent control and management of the equipment; the operation status of the liquid filling machine can be remotely monitored by using PLC wireless technology. Through the wireless network connection, equipment manufacturers or managers can monitor the equipment in real time at any time and any place. This not only includes the operating status of the equipment, such as temperature, pressure, speed, etc., but also can monitor the production process and product quality, such as the color of the liquid, viscosity, flow, etc.. If the equipment malfunctions or the production process is abnormal, the monitoring system will immediately issue an alarm so that the management personnel can take action quickly.
Third, real-time data recording
In the filling machinery and production line, due to the large number of points in the filling system, generally use medium-sized PLC, the following for the system how to realize the remote, through the automatic filling machine with the core of the system (such as PLC, etc.) connected to the combination of 3G, 4G5G, WiFi, Ethernet and GPRS and other communications and through the proprietary security channel to achieve the connection with the server, to achieve the remote monitoring of the equipment and the management and control. management and control of equipment. And through the platform's powerful data analysis capabilities, analyze a variety of data from the controller, combined with the early warning value set by the customer to achieve the fault warning and diagnostic functions of the equipment, complete the remote control system program level online diagnosis, download and on-site video viewing, data collection and other functions, to provide minute-level maintenance and diagnostic response for the equipment, and according to the customer's requirements for the operation of the warning Security. Wireless technology makes real-time data recording possible. By installing various sensors and data collectors on the automatic filling machine, it is possible to obtain real-time data of the equipment, such as temperature, pressure, liquid level, etc. These data can be transmitted to the wireless network. These data can be transmitted to the central control system or cloud database via wireless network for analysis and processing. By analyzing this data, we can better understand the performance of the equipment and the quality of the product, so as to improve and optimize it.
IV. Troubleshooting
Wireless technology can help with troubleshooting. When equipment failure occurs, the wireless system can immediately transmit fault information to the central control system or equipment manufacturer. In this way, maintenance personnel can arrive at the scene in the shortest possible time for repair, reducing downtime and production losses. In addition, by analyzing the equipment data, we can also predict possible problems and take measures in advance to avoid failures.
V. Real-time adjustment of control parameters
Weighing and filling machine through the screen real-time display of the current filling quality, filling the number of barrels and other on-site work status, through the wireless PLC in the upper computer communication at the same time to carry out the corresponding operation, through the interface for the filling mode selection and start, stop and other button operation. It is possible to change the filling quality, the number of barrels and manually remove the tare (i.e., the quality of the filled bottles) when different filling barrels are used. In order to realize the above monitoring requirements, the monitoring interface simulates the dynamic filling process by adopting Haniwa effect and fast flow attribute settings; it realizes manual/automatic selection, starting, stopping, emergency stopping and manually opening the pump solenoid valve by adding standard buttons; and it realizes the real-time display of the filling quality settings, the setting of the number of barrels and the display of the number of barrels, etc. by setting up the display output attribute of the labels, and it also realizes the monitoring of the running status of the filling system by setting up the monitoring screen. Filling system operation status monitoring. Wireless technology makes it possible to adjust control parameters in real time. In the traditional equipment control, you need to manually adjust the control parameters, which is not only time-consuming and laborious, but also may lead to errors due to human factors. Using wireless technology, the control parameters can be transmitted to the equipment control system through a wireless network to realize remote automation control. This will not only improve production efficiency, but also improve product quality.
Six, mobile equipment management
Based on wireless filling equipment management system mainly includes three parts: server system, filling system, real-time monitoring system. Server system includes application service and database service, system data is stored on the server, the whole system application is deployed on the server, and end users use PC terminals to access Web services through the network. The filling system is mainly composed of weighing system, control system, filling mechanism, transfer mechanism and so on. The filling system adopts the weighing module to process the weighing data by the control system and adjust the opening and closing of the filling mechanism in order to make the filling reach the weight required by the weighing. Wireless PLC is used to collect all kinds of data on site and transmit them to the central control room for centralized monitoring and management through high-speed network, and the host of the central control room also transmits the control commands to the PLC measurement and control terminals through high-speed network to implement the decentralized management of each unit. Wireless technology makes it possible to manage mobile devices. Remote management of equipment can be realized through wireless network connection. This includes not only basic operations such as switching on/off and monitoring of the operating status of the equipment, but also planning and management of the maintenance and upkeep of the equipment. In addition, through the mobile device management system, it is also possible to optimize the location management and frequency of use management of the equipment.
VII. Conclusion
The application of wireless technology on liquid filling machines is changing the way we work. Through the application of remote monitoring, real-time data recording, fault diagnosis, real-time adjustment of control parameters and mobile equipment management, comprehensive automation and intelligent management of equipment can be realized. This can not only improve production efficiency and reduce production costs, but also improve product quality and equipment performance. In the future, with the continuous development of wireless technology, there is reason to believe that the application of wireless technology in the liquid filling machine will be more extensive and in-depth.