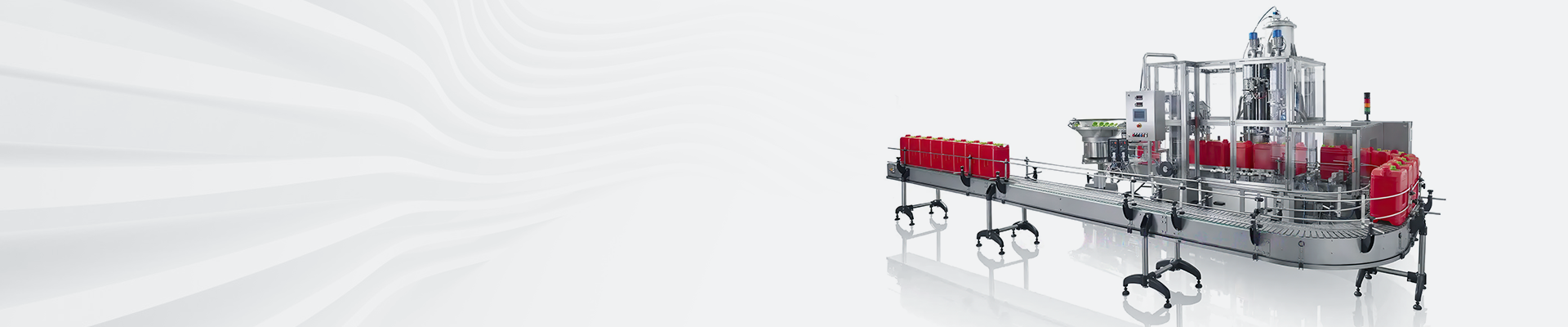
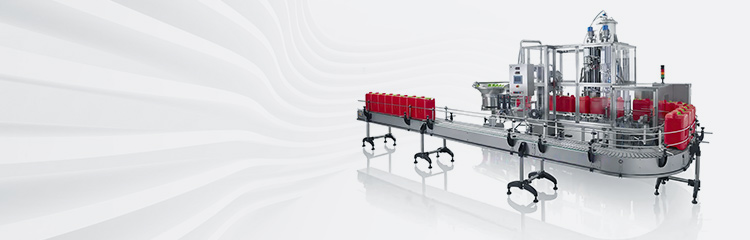

Summary:Liquid filling machine manipulators are defined according to ISO8373 as: the position can be fixed or moved, can realize automatic control, can be programmed repeatedly, and has a variety of multiple rectangular coordinate manipulators and other equipment to work in strict synchronization and coordination.
Definition and main features of the filling robot
Filling robot according to ISO8373 defined as: position can be fixed or mobile, can realize automatic control, repeatable programming, multi-functional multi-purpose, end operator position to be programmable in three or more degrees of freedom within the industrial automation equipment. Here the degree of freedom means the axes that can be moved or rotated. Cartesian coordinate manipulators are based on linear axes of motion, and each axis of motion usually corresponds to the X-axis, Y-axis, and Z-axis in a Cartesian coordinate system. In most cases, the angle between the linear motion axes of a Cartesian Coordinate Automatic Filling Machine Robot is a right angle.
A Cartesian Coordinate Filling Machine Robot consists of a number of linear motion units, drive motors, control systems and end operators. For different applications, can be easily and quickly combined into different dimensions, a variety of strokes and different load capacity of wall-mounted, cantilevered, gantry or inverted and other forms of right-angle coordinate explosion-proof filling machine manipulator, from the simple two-dimensional manipulator to the complexity of the five-dimensional manipulator there are hundreds of structural forms of successful application cases. From food production to automotive assembly and other industries in the automated production line, there are a variety of multiple Cartesian Coordinate Manipulator and other equipment to work in strict synchronization and coordination, it can be said that Cartesian Coordinate Manipulator is capable of almost all industrial automation tasks. The following are its main features:
1 any combination into a variety of structural styles, load capacity and size of the robot.
2 using multiple linear motion unit cascade and rack and pinion drive, can form dozens of meters of large stroke liquid filling machine manipulator.
3 using more than one linear motion unit level connection and each with multiple slider structure when its load capacity can be increased to several tons.
4 Its maximum operating speed can reach 8 meters per second, acceleration can reach 4 meters per second.
5 Repeat positioning accuracy can reach 0.01mm ~ 0.05mm.
6 With RTCP function of five-axis or more than five-axis CNC system can complete the work of very complex trajectory.
Germany VC vision system introduction
Explosion-proof filling machine is to make the machine human eye and brain part of the function, can automatically carry out geometric shape measurement, printing quality deficiency identification and product appearance quality identification and other work. Weighing automatic filling machine system is usually used in the fully automated, efficient and reliable and non-contact mass production process of inspection and identification work. Common vision systems generally include: light source, lens, CCD camera, image acquisition card, image processing software, monitor, communication/input/output unit and so on. And many smart cameras is a general image processing system, the lens, image sensors, high-speed DSP, memory, commonly used image processing software, communication port and / input and output ports, etc., integrated in a cigarette box size box, the user can be programmed arbitrarily, can replace the PC-based image processing system. Intelligent camera has a color intelligent camera and black and white intelligent camera, wired array and face array intelligent camera, this paper only introduces a German VC company face array black and white CCD intelligent camera.
Filling work first CCD smart camera will be ingested target is converted to gray-scale image signal, first amplify the signal, and then digitized into digital images. Digital image to a two-dimensional matrix to store up, such as VisionComponentsGmbH intelligent camera VC2028 of each digital image is 640 * 480 two-dimensional matrix. Each element of the matrix is called a pixel, and its value is usually from 0 to 255, with pixel values from 0 to 255 corresponding to the darkest and brightest parts of the target. The image processing software is to extract the characteristics of the target in the image according to the information of pixel distribution and brightness change in the image, such as: the number of holes, area, shape, length, shape width and position, etc., and also brightness change, etc., and then compare and match with the stored template, and finally give the size, angle, offset, number, pass/fail, and have/have not. Result.
Users can write their own application programs in C or VC on the PC, and then download them to the smart camera, which runs the program to complete specific tasks. You can also use the image processing software that comes with VC.
Filling robot numerical control system
Filling robot control system using German motion control technology company (Movtec) of the three-axis motion control card DEC4T and motion control software Editasc. DEC4T motion control card is based on the PC, dedicated to the control of three stepper motors and digital servo motors motion control card. EdiTasc is not only a variety of control cards supporting the MOVTEC company's general-purpose CNC software, it is also a highly open EdiTasc is not only the general numerical control software for MOVTEC's various control cards, but also a highly open development platform, which can directly control various industrial automation equipments or conveniently develop user-specific pages and control systems. 36 digital inputs and outputs are provided with DEC4T to serve as limit switches, to control the CCD intelligent camera and to start the detection instruments.
Editasc can be programmed in Mtasc language or G-code. Mtasc language is a special language for Editasc, which has some features as below:
Arbitrary definition of variables and arrays of various lengths and types;
many mathematical functions
many loops
Multiple conditionals
allowing any level of extension and nesting.
Calling subroutines and calling subroutines in other languages.
Extremely convenient I/O port operation.
In the process of program input and editing can be executed in any line or several lines of the program, can be convenient to verify the program and the rationality of the data.
Several typical applications
1 Product labeling inspection
In almost all of the modern mass production process, the text printed on the product box, symbols, labels on the product, etc. require beautifully printed, without any defects and errors. However, in practice, the following problems will occur, such as part of the character leakage, part of the character is incomplete, confusion between different characters, such as: 5 and 6; 6 and 9 printed mixed, the character position is not right, the character font is not right or inconsistent. To solve the above problems must be selected an excellent image processing system, these words and symbols for 100% reliable inspection, in order to ensure that 100% pass rate, to achieve the real "zero defects". The text and symbols to be inspected and recognized can be generated by the following ways: printing, coding, thermal transfer and laser engraving. This increases the difficulty of inspection and identification.
In this paper, the CCD camera selection of German VisionComponents intelligent camera VC2038. Its configuration is as follows: CCD chip is Sony1/2 "640 * 480 points, 25 images per second, the memory configuration is 16MBDRAM, 2MBFlashEprom, 8bit overlay, 8bit overlay. 8bit overlay, CPU is TMS320C62XX, speed is 1200MIPS (1200 million instructions per second).VC2038 through its own RS232 port can be transmitted to the PC position data.VC2038 also comes with 4-way digital input and 4-way digital output. Corresponding lenses are selected according to the field of view range and height.
The inspected products are discharged in a single row on the conveyor belt, the filling robot first stops the conveyor belt and moves the inspection head to the top of the first product, and the identification system starts to automatically detect and identify the first product. Explosion-proof liquid filling machine robot and then move the detection head to the second product above, and then the identification system began to automatically detect the second product, and so in turn to identify the last product in the row. Then start the conveyor belt to move the second row of products to the detection system directly below, and start the automatic inspection and identification of the line of products.
Similar applications can also be used in a variety of product appearance inspection, packaging inspection, trademark inspection and other applications.
2 print quality inspection
The product being inspected is the text on the transparent plastic. The robot first stops the conveyor belt, and moving the detection head at a constant speed, the recognition system in several specific positions to automatically detect and recognize the printed text and symbols. Plastic and then start a certain length, liquid filling machine manipulator reverse movement, the detection system to start the line of automatic inspection and identification of products.
Measuring and filling machine robot is a single-axis robot of Germany BAGRA company, due to the small load and moving speed requirements are not high, it is selected model LM-P404R-AT5, the effective stroke according to the requirements of the task is selected as 1500 mm, the drive motor is a stepping motor of the BAGRA company VRDM3910LWB, the control system of the automatic filling machine robot selection of BAGRA company's special industrial control machine TLCC. The TLCC controls the TLC611 stepper motor driver via CAN bus. The image processing system uses the inspection system VE4000OCV/2 from VisionExperts, Germany.
The filling system consists of an intelligent CCD camera VC2038 and a patented recognition software, which can detect all kinds of symbols, such as: printed symbols, spray code symbols, thermal transfer, laser engraving, etc. The system can be used to detect all kinds of symbols. It can 100% guarantee to find all the following problems: whole or part of the character missed printing, incomplete characters, confusion between different characters, such as 5 and 6, 6 and 9 printed mixed, the character position is not right, the font of the character is not right or inconsistent. The system recognizes a wide range of symbols and works well when the contrast between the symbol to be recognized in the image and the background varies somewhat, such as when there is a problem with the lighting system, or even when there is some kind of regular texture in the background of the image. The system is also very flexible and can detect only 10 products a minute or 100,000 products an hour; it can detect 300 characters at the same time or a collection of symbols containing 10 fonts at the same time. The inspected products can be rotated to realize real-time dynamic detection in motion, E4000OCV/2 system automatically gives the detection data, there are self-test and external signals to start the formula, the detected symbols can be scaled down or zoomed in to give the symbols of the position data.
Not only plastic detection so, other aspects such as printed matter, wood, PS boards and other aspects of the detection of similar methods.
3 Workpiece identification and positioning and gripping
With the improvement of automation production capacity, modern factories often need to sorting occasions, then there is a great need to work with the vision system of the automatic filling machine robot to achieve this work. This is an example of positioning and gripping different batches of products in a warehouse. Before the start of the machine, the operator according to specific needs, through the computer will need to handle the batch of products transferred to the vision system, when the weighing automatic filling machine manipulator drives the vision system to reach the top of the product, the vision system through the acquisition of the image to identify, usually identifies the object for the bar code, when the product is confirmed to need to handle the product, then the vision system and then through the acquisition of the image to accurately locate the coordinates to transmit to the metering and filling machine robot. The coordinate value is transmitted to the weighing and filling machine robot, and the weighing and filling machine robot then moves to the specified position for gripping and handling. If the product is not detected as a product that needs to be handled, then the corresponding signal is transmitted to the weighing and filling machine robot, and the explosion-proof automatic filling machine robot moves to the next workpiece position for the next inspection.
The system of weighing and filling machine also uses the German VisionComponents intelligent camera VC2038, vision liquid filling machine robot using Germany BAGRA Cartesian Coordinate Liquid Filling Machine robot, the control system used for the German MOVTEC motion control card, so as to ensure that the vision system and Cartesian Coordinate Liquid Filling Machine in a computer control and cooperation. Robot control and cooperation.
At present, similar systems have been applied in many automated assembly lines, are very good results.
4 vision system guided by the measurement of explosion-proof filling machine
Currently weighing and filling machine robot has been applied to various fields, the following we introduce the use of explosion-proof filling machine robot in the quantitative filling machine. In some factories need to fill a large number of liquid products to facilitate transportation, so naturally increase the demand for automatic filling machine for the visual guidance of the right-angle coordinate vision filling machine robot in the filling machine. Variable frequency filling machine manipulator aspects of the selection of Germany Bagera gantry type three-dimensional Cartesian coordinates speed control explosion-proof filling machine manipulator, vision aspects of the selection of Germany VisionComponents intelligent camera VC4038E.
The system is used for the location determination of the barrel mouth by the method of BLOB region analysis. As each barrel mouth is directly above a white point and black hole with the iron barrel itself color distinction is obvious, then the visual system uses the method of area analysis to process the collected image, obtain the white point and the black hole position, and then determine the position of the barrel mouth through the conversion, and through the Ethernet port to transfer to the right-angle coordinates of the frequency conversion liquid filling machine manipulator. After obtaining this coordinate, the speed-regulated liquid filling machine manipulator directly drives the oil injection pipe to the top of the barrel mouth, then inserts it, injects the oil, and repeats the execution of the above actions when it is finished.
The system successfully solved the factory oil filling is difficult, time-consuming, laborious and other difficulties, greatly improving the efficiency of the work, so that within a few months it will recover the cost of the equipment. This type of application can be extended to other products or other shapes of filling container applications. In this visual liquid filling machine manipulator movement axis to be with metal protective belt, the drive motor used is explosion-proof motor.
Conclusion and outlook
In this paper, we have introduced the Cartesian Coordinate Temperature Controlled Liquid Filling Machine Manipulator of BAGRA Germany and the intelligent camera of VisionComponents Germany. Germany VisionComponents company's intelligent camera assembled in the Bagera company's Cartesian Coordinate self-control filling machine robot has been successfully used by many users in the positioning of workpieces, sorting and handling. With the rapid development of high-volume automated production, many products to be detected in many aspects of production and accurate positioning, this kind of Cartesian coordinates under the liquid filling machine manipulator and image processing system will have a more extensive market prospects and development potential!