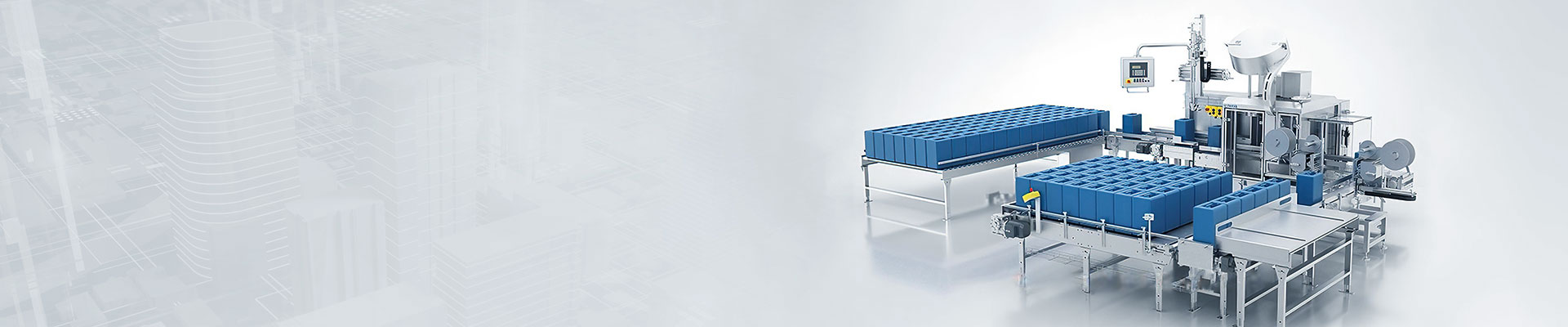
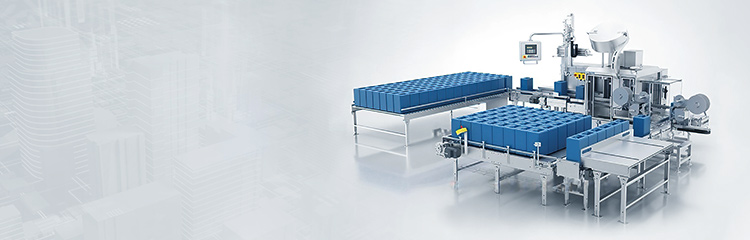
The grease filling machine integrates the functions of conveying, measuring, filling, recording, monitoring and charging liquid. It is mainly used for the selection and setting of filling formula, monitoring of filling process, processing of alarm signal, and retrieval of dosage data. Realize the full automation and intelligence of filling by a certain proportion, the upper computer sends the formula filling weight instruction, adopts the industrial mechanism with communication board, which can provide RS422 communication port and RS232 communication port, and the communication port is connected with the upper computer respectively. The communication protocol adopts query scanning method.

The automatic Filling machine integrates the functions of conveying, measuring, filling, recording, monitoring and charging liquid. It is mainly used for the selection and setting of filling formula, monitoring of filling process, processing of alarm signal, and retrieval of dosing data. Realize the full automation and intelligence of filling by a certain proportion, the upper computer sends the formula filling weight instruction, adopts the industrial mechanism with communication board, which can provide RS422 communication port and RS232 communication port, the communication port is connected with the upper computer respectively. The communication protocol adopts query scanning method.
Liquid filling machine carries out all kinds of initialization and forms the recipe according to the production task, the recipe includes the name, quantity, output, standard ratio, standard weight of each component, etc., and then sends the parameters to the weighing instrument and programmable controller, and according to a certain time sequence to control, the weighing instrument and the start of the filling gun, the upper computer reads the weight signal of the liquid filling scale and sums up, and calculates the actual ratio according to the summed up value of each component The upper computer reads the weight signal of liquid filling scale and sums it up, calculates the actual proportion according to the summed up value of each component, and compares the actual proportion with the standard to correct the feeding quantity of each regulator, so as to make the system work under the optimal proportioning state.
Automatic filling scale filling data and monitoring information centralized processing, so that its daily work, such as sending and receiving, transfer and other operational procedures, standardization, institutionalization of each step of the operation of the law can be relied upon and evidence to eliminate management loopholes. Daily data reporting, auditing and summarizing timely and accurate filling information. With alarm display, alarm management and event query, printing: real-time data collection, archiving, management and trend chart display; production statistics report generation and printing.
Basic parameters:
Maximum weighing capacity: 30kg.
Minimum sensing capacity: 0.1kg.
Filling error: ±0.1-0.2kg.
Filling speed: 20L about 1500-1800 barrels/hour.
Control: 2-speed control.
Filling method: Insertion type, liquid level up.
Gun head line: Teflon gun head, valve + Teflon hose.
Structure material: liquid host SUS304 stainless steel, conveying palletizing carbon steel anticorrosion paint.
Weighing platform size: 400 x 800mm (304 stainless steel power raceway).
Empty drum raceway: 400mm×2500mm (304 stainless steel power raceway) with another 1200mm slope unpowered roller.
Heavy drum raceway: 400mm x 2500mm (304 stainless steel power raceway, 2 sets).
Separate barrel device: for 20L barrels, carbon steel anticorrosive paint structure, 304 stainless steel raceway.
Palletizing equipment: pan-transfer type, suitable for pallets 1200×1200×140mm, including supplying pallets, palletizing, and lower pallet conveying.
Pipe pressure: 0.2-0.6MPa (related to material properties).
Material interface: 4 DN40 flange connectors, interface standards can be provided according to the user.
Air Connection: User supplied 12mm air hose connector for quick coupling connection.
Power supply used: AC220/50Hz (user supplied to one side of the machine).
Using air source: 0.4-0.8Mpa (provided by the user to the side of the machine).
Use temperature: -10℃-50℃.
Base condition: Horizontal solid concrete floor, concrete thickness should be more than 10cm.
Optional models: standard and explosion-proof filling scales.