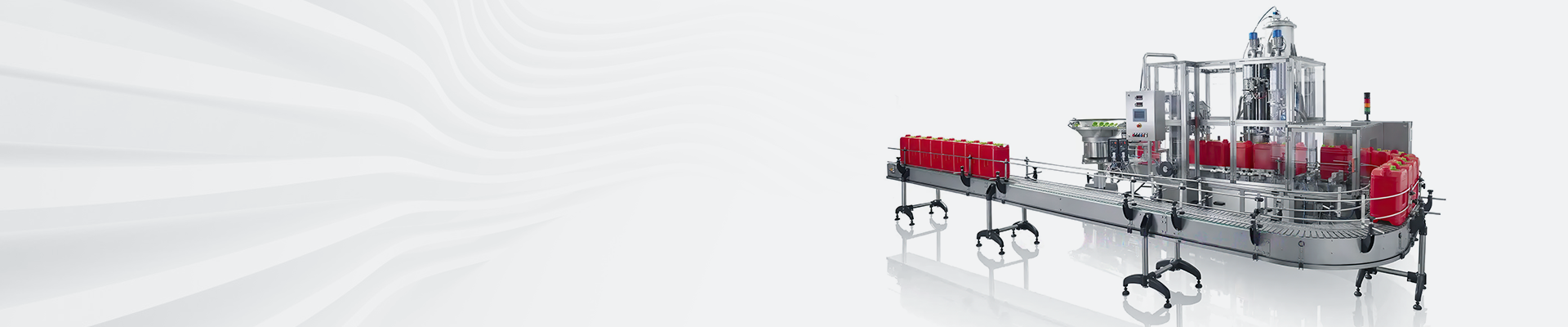
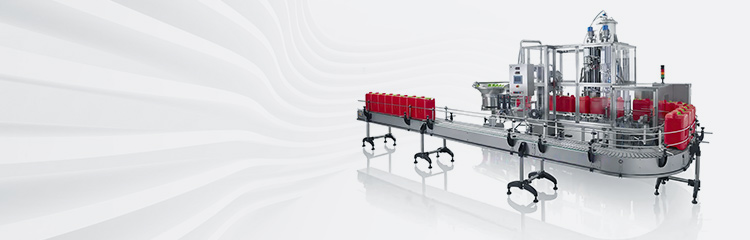
摘要:液体灌装机将活塞提升时物料由阀门控制从上部油罐吸人活塞缸内,而后封盖、封箱、码垛以及相应的输送带,伺服电机执行定位辅以自动控制和自动调整系统组成。
液体灌装机是由灌装、封盖、封箱、码垛、称重设备以及相应的输送带,辅以自动控制和自动调整系统组成。 自动灌装机当四立升桶到达进料输送带时,由螺旋进桶器将桶分离并送人到旋转油罐注油嘴下的固定秤平台上,定量灌装是将活塞缸对称配置圆的旋转油罐的周围,每一活塞通过连杆与一轴乘相连,并按倾斜圆周轨迹滑动。倾斜圆周运动的前180度使活塞上升,后180度使活塞下降。当活塞提升时,物料由阀门控制从上部油罐吸人活塞缸内。当连接活塞缸与注油嘴的阀门打开时,物料注入下方桶内。
自动灌装机的PROFTIBUS-DP网络是一个由3个主站、7个从站构成的PROFIBUS系统,3个主站之间构成令牌逻辑环,当某主站得到令牌报文后,该主站可在一定时间内执行主站工作。在这段时间内可依照主-从通讯关系表与所有从站通信也可依照上,主通讯关系表与所有主站通信。TEP7中编程界面、数据查看界面提供了离线和在线两种视图。离线视图显示的PO本地存储的项目内容,在线视图显示CPU中的实际内容,当PC通过编程电缆与PLC连接后,就可以在STEP7中建立在线连接。
液体灌装机从现场设备采集以数字量的形式发送的数据,通过对实时数据的操作实现监视和控制功能。提供一个帮助监控生产过程的实时数据库。带有实时更新数据显示的设备画面,同时提供一个大的画面显示了整个运行流程,使你易于观察整个生产工艺流程。显示的数据包括运行方式、重量、累计量、设定点、偏差和其它类似的数据。
称重灌装机对整个生产线的各种灌装设备进行监控,在控制CRT上可以直接观察到所有与称重系统相关的生产设备的运行状况,画面里对于电机等运动的设备都设置了动画指示功能,实现了历史曲线的绘制,可以在线动态增加/删除曲线、曲线图表的无级缩放、曲线的动态比较、曲线的打印等。工艺参数如温度、压力、流量等进行记录。在下位机的PLC程序中故障报警,操作界面都可以看到总故障报警变为红色并不断闪烁,硬件电路里的蜂鸣器产生报警铃声。产生报警自动切换到故障分析界面,直接看到报警原因。
液体灌装秤对桶身份数据的重量采集,供上位机数据库进行桶身份和规规识别,基于EPC无源芯片电感线圈等组成,通过外接的LC回路接收来自读写器的R信号,经过芯片内部的电源电路处理为芯片提供电源,通过芯片内部的阻尼负载,片内EEPROM中的数据被读入读写器,并以特殊的方式中断RF场,使读写器可将数据写人片内EEPROM中。读写器数据上传录人服务器。桶的适当部位粘贴有电子标签,当桶放上称台后,将 RF读卡器对准电子标签部位,启动读卡器读取电子标签ID代码,然后从读卡器取出瓶身ID号,上传到单片机,单片机再将该数据上传到上位PC机进入气瓶信息数据库。ID号在数据库中进行查询比较,同时返回一个代码给单片机。单片机一方面返回一个信号给读卡器使读卡器关闭,另一方面单片机根据程序设置进行灌气的相关控制操作。
自动填充机利用率高,生产具有柔性,可以适应生产变化。当市场需求或设计发生变化时,不需要系统硬件结构的变化,设备具有生产不同产品的柔性。具备数控快速转换的多功能性设计更容易在小型包装生产线上实现。各类包装更新换代比较快,市场需求触发了多功能灌装机的开发。快速转换基本还是两种方式,一些部件无需使用工具实现快速换装,比如灌装的星轮和导板;另一种如灌装缸的升降,贴标机、装箱机和码垛机的调整由PLC控制若干伺服电机的运转调整到需要的位置。一条自动灌装生产线是否应具有快速转换的功能,容易实现比较经济性的快塞转换。瓶型的外形尺寸变化较大,则需另有考虑。比如一台变频变速要使用直径50mm和直径150mm两种瓶型,一般小规格瓶型灌装速度快、瓶间距小、设备转速高;大规格瓶型灌装速度慢、瓶间距大、设备转速低,因为设备的转速要按照小瓶型设计,设备的瓶间距(通常解释为设备的模数)要按照大瓶型设计,设备的经济性惟恐要大打折扣。高生产能力的理瓶设备则更不能容忍瓶型变化较大的设计。对于贴标、装箱、码垛设备,灌装的转换主要靠调整实现,一个新定位尺寸的实现由伺服电机执行,其准确性不容置疑。但位置实现后定位的稳定性和可靠性取决于定位器的刚性,自动灌装生产线更要具备监测、运行和故障诊断的显示系统,进行调速灌装生产线运行的精确设计,才能使整条生产线的各种设备运转始终处于动态平衡之中,确保设备的效率和可靠性。