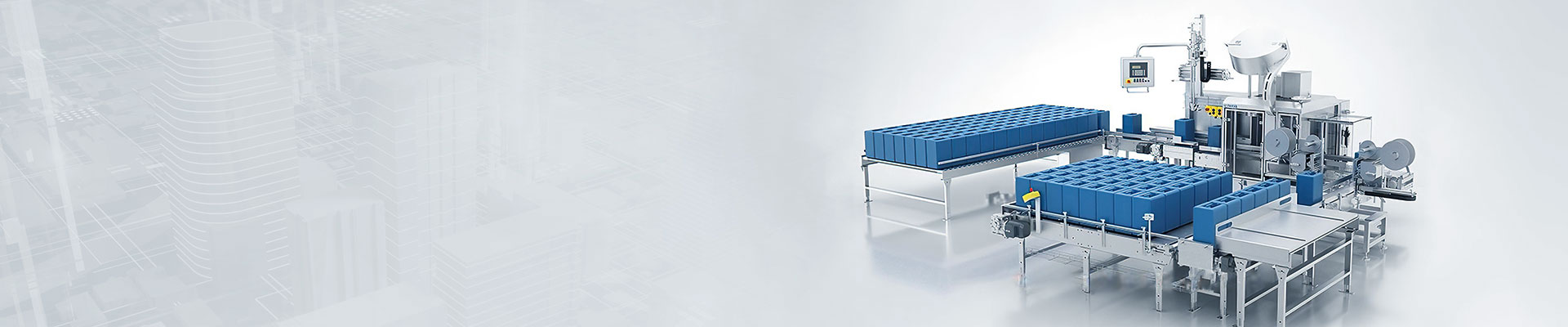
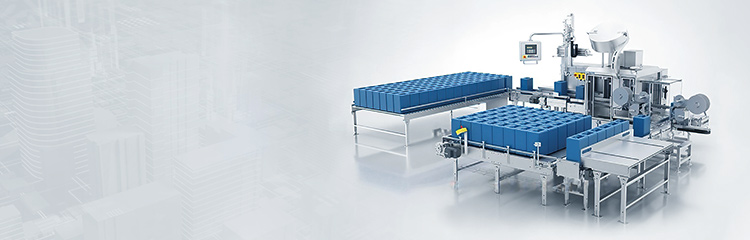
Automatic batching machine through PC+PLC monitoring, the use of weighing measurement or flow measurement, can be accurate measurement of the ingredients, the use of PLC to monitor the entire feed and batching process, and complete the system fault display and alarm function, through the frequency converter transmission signal to complete the speed of the screw conveyor.

Automatic Dosage system is one of the most critical production links in industrial production, and the quality of dosage will directly affect the production quality of products. Automatic batching machine process is a multi-input and output process, each batching production line orderly, coordinated cooperation, accurate control of material level and quantity. The whole batching production process, in accordance with the proportion of the main material and auxiliary materials to match, through the spiral scale, accurate measurement of the material conveyed by the screw conveyor. The PLC monitors the whole feeding and dosing process, and completes the function of displaying and alarming the system faults, and transmits signals to the frequency converter to complete the speed of the screw conveyor.
The feeding system mainly consists of silo, weighing silo, intermediate silo, mixing silo, silo wall vibrator, feeding vibrator, discharging vibrator, as well as screw conveyor, mixer and other parts. The motor completes the control of each vibrator and mixer; the solenoid valve completes the control of the intermediate bin door and the discharge door of the mixing bin. The weighing frame is suspended by two Weighing modules, when the material on the screw passes above the weighing frame, the weight of the material is pressed on the weighing module by the roller, and the output signal of the weighing module is proportional to the weight of the material. The output signal of the weighing module is proportional to the weight of the material, which is converted to the average weight of the material per unit length of the spiral (kg/m). At the same time, the speed module measures the running speed of the spiral at that time (m/s), thus calculating the instantaneous flow rate of the material on the spiral at that time (kg/s). It will be added up to constitute the total material conveying capacity.
When the automatic dosage system is energized, the motor drives the screw to carry out the action, and the microprocessor carries out the control of the motor speed. The dosage is dropped from the hopper to the drop zone, transferred to the weighing zone by the screw, and the screw weighs the material on the screw. The load cell outputs a voltage signal according to the material pressure, which is amplified and outputs a metering level signal, which is proportional to the weight of the material. Then the signal will be sent to the upper computer interface, and converted into a flow signal, the flow value in the current upper computer for display, and at the same time sent to the PLC, the PLC will be set with the upper computer for comparison with the dosage of the given value for calculation. The PLC will compare and calculate with the dosage value set by the upper computer. The control quantity will be transmitted to the frequency converter, and the output value of the frequency converter will be changed to complete the control of the rotational speed. Adjust the dosing amount to be the same as the set value to complete the dosage process.