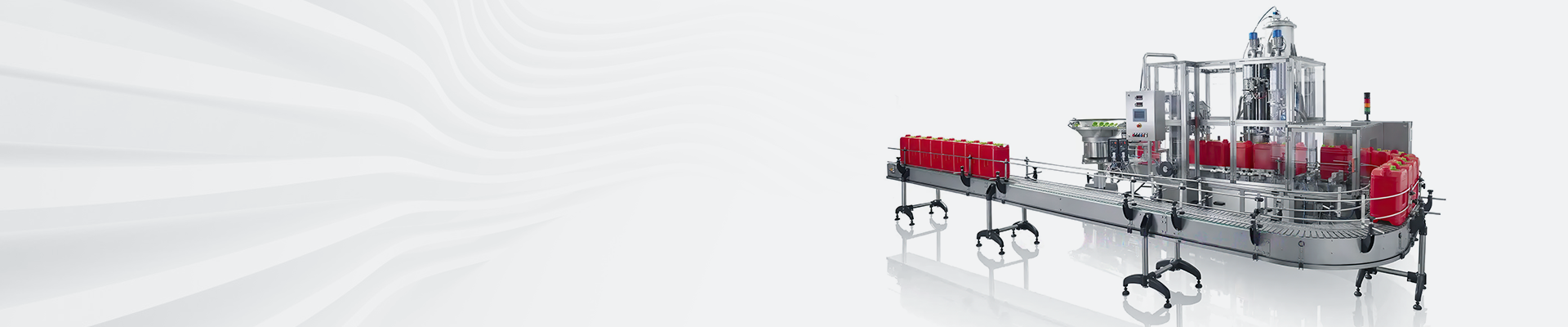
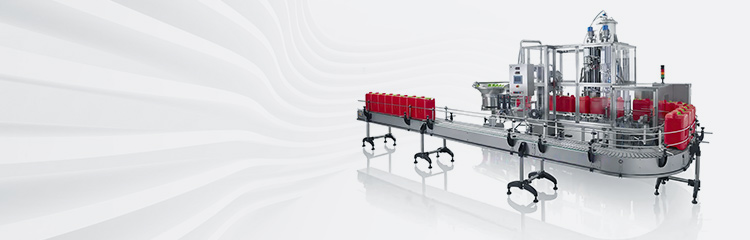

Summary:The batching system adopts advanced SIEMENS PLC, industrial control computer and PANTHER electronic weighing equipment.Its main components include the power part, the control part, the feeding and discharging part and the weighing part, etc. It is a fully automatic computer control system designed for float glass production.
1. Silo part design:
The batching plant uses rows of silos to store materials, there are 8 powder silos and 1 crushed glass silo, there is an activation funnel at the exit of the powder silo (crushed glass and limestone with a screw gate), and the exit of the activation funnel of the silo is connected to the inlet of the feeder through a soft connection, and the system will decide to activate the startup of the activation funnel based on the flow of materials in the silo to ensure the normal supply of materials.
2. Feeding part
Feeding part includes activation hopper and feeding equipment (electromagnetic vibrating feeder or screw conveyor, choose different specifications according to the actual range of materials).
Manganese feeding group crusher.
3. Weighing part design
The weighing part adopts load cell, and the weighing hopper is equipped with dust removing port and connected with the guide chute of the collecting belt to prevent the leakage of dust. The weighing system adopts the "reduction method". The discharge adopts electromagnetic vibrating feeder. Discharging should have the function of time-sharing operation, so that the material is evenly spread into the sandwich state. Manganese and coal powder are mixed into the premixer first, and the premixer is discharged at the same time with other materials. The broken glass is evenly spread on the mixed material.
Static accuracy: National Ⅲ scale standard (certified by the measurement department)
Dynamic accuracy: more than 95% of the single material error ≤ 3 d
4. Material mixing control
The material is put into the mixing machine through the intermediate composite scale with the material belt to complete the mixing operation of the material. Mixed material from the mixer discharged into the silo through the flow chute to the mixer belt machine sent to the kiln head silo, mixer model T75L.
5. Sandstone online water measurement
Selection of online water measurement technology, the mixer water system should be connected to the online water measurement, according to the set value of the automatic adjustment of the amount of water, water measurement device should not be radioactive contamination.
6. Weighing and batching system
The system should have the functions of full-automatic, semi-automatic and manual. The system is controlled from the outlet of the silo until the qualified mix is delivered to the kiln head silo.
The control of the batching, mixing and conveying sections is all from the batching control room, which has analog display and industrial TV to monitor the whole process.
The control room should have the ammeter of the mixing machine, weighing batching machine, mixing feeder and other equipments, the system equipment should have the chain function.
The weighing and batching system (computer data processing system) adopts the form of upper computer + programmable controller, and should have the following functions:
The weighing control system shall have power-down protection function;
The upper computer manages the system to collect data automatically;
The system shall have self-diagnosis function;
The system has self-diagnostic function. It has the function of automatic correction of overshooting amount and point-action replenishment;
Management and transmission of formulas and set values;
Automatic control of the mixer to add water;
Alarm for overshooting and fault printing;
Friendly man-machine interface, multiple use rights multiple password restrictions;
Display, print the current formula and production report;
Displaying, printing and storing the single and total consumption of all kinds of materials on shift, day and month;
7. Working conditions of dosage control system
1、Water pressure: 0.3MPa, water temperature: 85℃.
2、Steam pressure: 0.3MPa
3、Compressed air pressure: 0.5Mpa
4、Power supply: three-phase 380V; single-phase 220V50HZ
Principle of dosing realization
Feeding system in the process of equipment selection and implementation of the following principles:
Generic: in the selection process, fully consider the convenience of spare parts purchase, in the case of meeting the design requirements as far as possible to choose common equipment standard: in the selection and programming in the use of standard methods to get the system equipment manufacturers as far as possible in the future may provide upgrading support Reliability: as far as possible to increase the anomaly detection, and at the same time, consider the non-critical equipment failure of the system's fault-tolerance to improve the reliability of the system; for For critical equipment, use redundancy methods to minimize downtime.
Ingredient Control Hardware Profile
Superior Control Methods
It can be selected as full-automatic control mode, semi-automatic control mode and manual control mode.
Full-automatic control mode: In this mode, the computer acts as the upper computer, PLC acts as a station, the system starts and stops controlled by the computer, the formula data is written by the computer, the computer transmits the data to the PLC to start the batching equipment, feed and discharge the materials automatically, weigh and calibrate the various raw materials, add water and steam for mixing, convey the belt into the warehouse, and monitor the batching process and the related data to process, tabulate and print out the report form. Semi-automatic control mode.
Semi-automatic control mode: PLC can work independently without computer, the recipe list is inputted by SIMATIC2OP7 touch screen, PLC will automatically complete the process of starting the batching equipment, automatic feeding and discharging, weighing and checking of all kinds of raw materials, adding water and steam mixing, and transferring the belt into the warehouse, and the report cannot be printed in this way.
Manual control mode: The operation desk is equipped with a manual mode switch, which can be selected through the selector switch.
Manual mode: there is a switch for manual mode in the operation console, you can choose manual mode by selecting the switch, start and stop all kinds of equipments by manual buttons, start the dosage equipments, feed and discharge the materials manually, add water and vapor mixing manually, and transfer into the warehouse by belt.
The batching control system is a three-level redundant control system, the system is separated by modules, interconnected, but also can be naturally separated, the computer automatic mode is to be used frequently, the operator only need to press the start or stop button, the system will automatically start all kinds of equipment, automatically send a batch of well-mixed materials to the kiln head silo, and with data management functions.
Reliable power section
The power part includes 4 control cabinets, respectively D1~4 cabinets; D1 cabinet is the general power switch cabinet; D2 cabinet is the feeding and discharging electromagnetic vibrating feeder driving cabinet, equipped with AC power regulator to stabilize the input power supply and reduce the impact of electromagnetic vibrating feeder on the upper power supply; D3 cabinet is the control cabinet for the dust removing fan, dosing conveyor, mixing conveyor and pre-mixing machine, dolomite, soda ash, reamer, and water pump; D4 cabinet is the control cabinet for the mixer, mixing conveyor and pre-mixing machine; D4 cabinet is the control cabinet for the mixer and mixing machine. Cabinet D4 is the mixer control cabinet (soft start).
For computer, PLC, weighing instrumentation and other equipment, one UPS is set to ensure the power quality of computer, PLC and instrumentation.
Advanced control section
The control part includes T1~4 cabinets: T1~2 cabinets are for eight kinds of raw materials feeding and discharging control and weighing display; T3 cabinets are for SIMATICOP7 and water measuring instrument installation cabinets; T4 cabinets are for analog disk, PLC and its peripheral relay circuits.
PLC using SIEMENS (Siemens) SIMATICS7-300, CPU315, is suitable for medium and large-scale programmable control system, it has a high-speed, robust, strong communication capabilities, human-machine interface operation is good.
SIMATICS7-300 through its MPI (Multi-Point Interface) can be connected with the programmer or PC, operator panel SIMATICOP27, data exchange, operator control and monitoring functions. In the computer can be stored in each batch, each shift, daily, monthly dosage situation and alarm information. Shift, daily and monthly unit and total consumption of various materials can be stored, displayed or printed.
SIMATICS7-300 is connected to each weighing and water measuring instrument through its PROFIBUS-DP to form a network for data transmission.
SIMATICS7-300 controls various devices through its I/O interface and its peripheral relay matrix, realizing automatic control of dosage line.
SIMATICS7-300 is equipped with SIMATICOP27 good man-machine interface, through which the operator can set the material formula, dry mixing, water and steam time setting, alarm confirmation, etc. without using a computer, which is easy to operate.
The analog panel displays the dosage flow, the position and working status of each field equipment in the automatic control process of the whole dosage control system with high-brightness LEDs, which is clear and understandable at a glance. The operation console is equipped with automatic mode, control room manual mode and on-site manual mode for starting and stopping all kinds of equipments, which is convenient for starting and overhauling the equipments.
Reliable feeding and discharging section
The dosing control system platform is equipped with nine kinds of raw material dosing devices, which are sandstone powder, feldspar, dolomite, soda ash, manganese, carbon powder, limestone, water and crushed glass.
Silica sand and soda ash silo bottom is installed with VBA series hopper activator, which has a good gate closure, its periodic vibration, can effectively eliminate all kinds of silo arching, clogging and sticking silo phenomenon. In the vibration process, the internal friction of the loose material is compensated, and the external friction on the silo wall is reduced, which improves the service life of the silo.
Dolomite and soda ash feeding adopts the reamer method, which can buffer the impact of dolomite material on the hopper and prevent the phenomenon of dolomite material "discharge", while other raw materials feeding and discharging adopt the DMA electromagnetic vibrating feeder, which can transfer the granular and powdery materials from the storage silo or hopper to the belt uniformly, continuously and quantitatively. Electromagnetic vibrating feeder is driven by silicon controlled control board to control the material flow by controlling its amplitude size. It can instantaneously change and open and close the material flow, so the feeding precision is high.
In order to ensure the smoothness of material flow when discharging, there is a K36 cyclone air vibrator installed on the weighing hopper of some raw materials: feldspar, limestone, soda ash, and intermediate silo, and the discharging time is intermittent, so that the weighing hopper shakes to eliminate the sticking material of the wall of the hopper and the fluffy material in the hopper. Feeding and discharging are equipped with manual and automatic modes.
Manganese, carbon powder and two kinds of raw materials are first discharged into the small mixer for pre-mixing, and then discharged to the dosage conveyor belt.
The discharging adopts delayed discharging mode, discharging in the dosing conveyor belt, before entering the intermediate station, all kinds of materials are stacked in layers, which is conducive to the full mixing of materials.
Precise weighing section
There are eleven weighing units in the weighing section, which are sandstone (1), sandstone (2), dolomite, limestone, feldspar, soda ash, manganese nitrate, carbon powder, water, crushed glass and total calibration of the intermediate station. Each weighing unit consists of three resistance strain load cells connected in parallel and a PANTHER indicator.
PANTHER weighing instruments have the following features:
7-digit fluorescent segment display with high brightness;
Integrated PCB structure with modular tree structure parameterization menu;
Bi-directional ProfiBus interface, weighing data transmission function; standard analog load cell input interface, capable of driving up to 8 load cells of 350 ohms; maximum display divisions of 10,000d; wide supply voltage of 85 to 364V, 100VAC, 120VAC, 230VAC;
The PANTHER is designed to comply with the relevant international standards for metrology and electrical safety, as well as for electromagnetic compatibility. The weighing method is based on the subtractive method (WIGHTOUT) of weighing, with single-speed feeding and two-speed discharge. "Reduction method"
Also known as the secondary weighing method, the first single-speed feeding operation, the feeding value should be greater than the actual formula value, all scales after the end of the feeding operation, the oscilloscope is cleared for the discharge operation, discharge is divided into two processes, fast discharge and slow discharge, fast discharge shortens the weighing cycle, while slow discharge ensures the weighing accuracy. Weighing part of the intermediate station, that is, all the raw materials together for a weighing, before entering the mixer to carry out the last inspection, check the weighing and the value and the intermediate station weighing value, in order to avoid the wrong material into the warehouse.
Advanced water measurement equipment
For the fluctuation of water content of sandstone, the water measuring device adopts advanced capacitance water meter imported from Germany, which has good stability, high accuracy, safe and non-radiation radiation, water measuring range of 0~15%, water measuring accuracy of 0.1%. According to the sandstone of different origins can be pre-stored more than 100 corrections to the water measurement curve, in order to achieve accurate measurement, and to facilitate the user to change the material.
Superior water filling method
The water filling method is the water weighing filling method.
According to the required moisture value of the mix and the measured moisture value of each raw material, the water weight to be added is calculated, and the water is injected into the weighing hopper through the fast and slow water feeding valve to weigh and measure, and the water feeding valve is closed when the requirement is reached. This way of adding water is accurate.
Raw material dosage software function introduction
1、Weighing management
Formula editing. Provide formula data of feeding value, moisture content, discharge value, slow discharge (feeding) value, allowable error, suspension amount of editing and saving.
Recipe download. Provide recipe data download to the controller
Recipe printing. According to user requirements, provide recipe printing parameter settings. Provide dry mixing time of mixer, wet mixing time of mixer, discharging time of mixer, discharging time of intermediate silo, pre-mixing mixing time, pre-mixing discharging time, feeding exceeding time, discharging exceeding time, vaporizing time, and editing, saving and downloading of the water introduced by the vaporizing.
Water measurement equipment setting. Provide editing, saving and downloading of water measuring equipment, water fluctuation upper and lower limits, and water default value.
Automatic correction of overshooting amount and point-to-point replenishment function. Based on the suspension amount set by the operator, the system corrects the actual suspension amount by calculating the actual suspension amount, and adopts the point-action replenishment for the suspension amount that is set too small, which ensures the weighing accuracy. Automatic compensation for water addition to the mixer. According to the change of the measured water content of sandstone, the system will automatically adjust the setting value of the water added to the mixer.
2、Monitoring of batching
Provide monitoring of gross weight and weighing of each scale.
Provide monitoring of the working status of the mixer and premixer and the related door opening and closing status.
Monitoring the working status of belt, iron remover and dust collector.
Monitoring the feeding and discharging status of various materials.
Provide dry mixing, wet mixing, adding water, adding steam and discharging status monitoring of the mixer.
Use industrial cameras to monitor the materials on the conveyor belt in real time.
3、Alarm monitoring
The system provides the following alarms:
Feeding (discharging) material over the difference
Instrument fails to switch net weight and gross weight in time
Communication failure of dosage meter
Failure of communication between computer and controller
4、Real-time printing
The system provides optional real-time printing function, which can be set by the user. If the user selects the real-time printing function, the actual dosage data of each batch will be printed after the dosage is completed. Alarm data is also printed automatically when the system detects an alarm.
The alarm data is also printed automatically after the system detects each alarm.
5、Historical data management
As the system adopts the standard database and Microsoft ActiveX technology, it is easy to realize the management of historical data, and the system provides the following historical data management functions:
Historical alarm query: historical data can be queried and printed according to any time period input by the user.
Historical dosage data query. The historical data can be queried and printed according to any time period entered by the user.
Data export. According to any time period input by the user, the historical data can be exported. The system supports Office system Excel and Access format export, archiving. Data deletion. According to any time period entered by the user, the historical data can be deleted.
6、system rights management
The system supports multi-level permissions, can be added by the system administrator, delete the operator, and specify the operator's rights. When using the system, you must first log in to the system to prevent unauthorized users from using it.
7、System redundancy
The system uses SIMATICS7-300 as the logic control unit and OP27 and industrial computer as the operation terminal. This structure design of the system can ensure that in the event of failure of the upper computer, the OP27 can be used to input the formula and monitor the dosage status to ensure normal dosage. In case of normal operation of the host computer, the OP27 can be used to check the working status of the host computer.