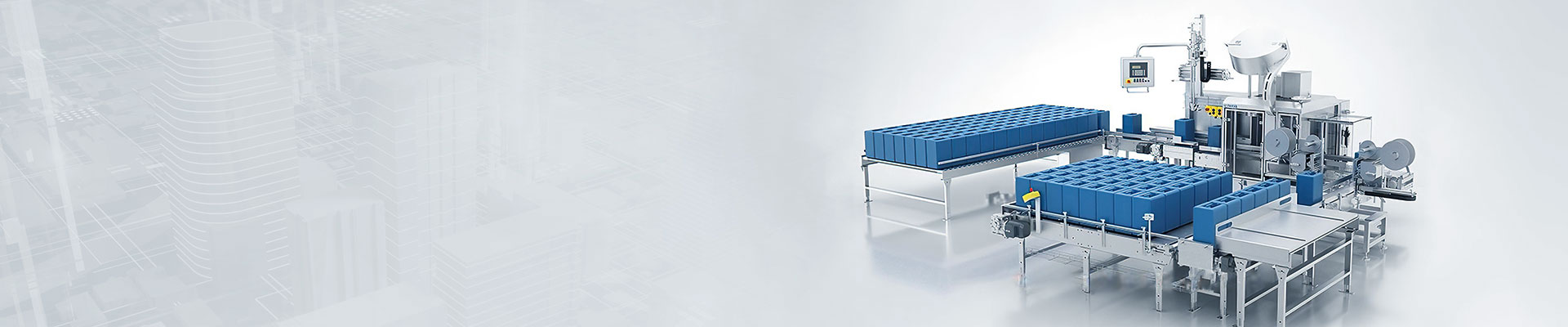
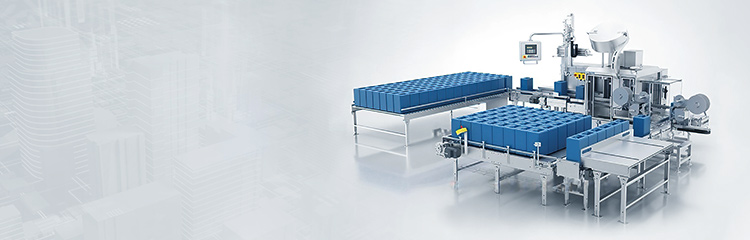
The automatic batching system is composed of multiple weighing devices, which can control multiple feeding and mixing devices at the same time, thus greatly reducing the cost of the system. It has the mechanism of mutual monitoring between the computer and the controller and various alarm mechanisms. The center of the controller adopts high-performance software to feed back the abnormal situation to the system in time and give an alarm in time to prompt it.

The automatic Batching system consists of conveying and feeding equipment, storage equipment, automatic Weighing system, dust removal system and PLC electrical control system. Batching system is an indispensable automation equipment in ensuring the stability of industrial production and product quality, eliminating the traditional manual work, improving the precision of formula weighing, realizing the automatic feeding of a wide range of material varieties, accurate batching of batch production. The automatic weighing and batching system has been applied in various fields such as lithium, resistant materials, building materials, cement, ceramics, iron and steel, non-ferrous metals, glass, petrochemicals, machinery, boilers, light industry, electric power, military industry and etc. The automatic weighing and batching system is suitable for the continuous batching of materials with no continuous batching, and the automatic weighing and batching system is suitable for the continuous batching of materials with no continuous batching.
Feeding system is suitable for the site without continuous batching requirements, these sites do not require high time for batching, can be batch batching, batch allows the existence of a certain time interval, such as blast furnace slot feeding before and after the two batches of time interval of 3 ~ 5min, each batch of material from a variety of materials, the ratio of materials accounted for according to the requirements of the process over a period of time is relatively fixed, the proportion of composition of a single material is not stringent, as long as the proportion of composition of materials in the more batches can be used in the As long as the proportion of materials in a larger number of batches can meet the process requirements, it is sufficient.
As the material measuring, conveying, adding and other aspects of the time can be overlapped, in the control process can be used in parallel to save time and improve the feeding speed. Various materials are stored in different silos, silo feeding is generally used in the form of electric vibration feeding, screw feeding or gated feeding. Measuring silo and equipped with pressure or pull type load cell for force and power conversion, the signal is amplified by the secondary instrumentation and processed into the PLC or DCS, etc. to complete the measurement. In some of the application occasions with wide time requirements, a measuring trolley can be used for uniform measurement, measuring trolley running along the track, positioned in turn to the bin under the proportional material dosage, the dosage of various materials using the method of calculation of the difference between the reduction. There is also a single fixed measuring bin way, the bins in a ring-like distribution around a measuring bin, the measurement of the material also uses the subtraction method, the material from the chute or conveyor in order to proportionally add to the measuring bin. After the dosing and measuring of the material after the collection, generally form a layer or segment distribution, through the conveying equipment (such as belts or trolleys) to the receiving port, into the next process, that is, to complete a batch of material dosing.