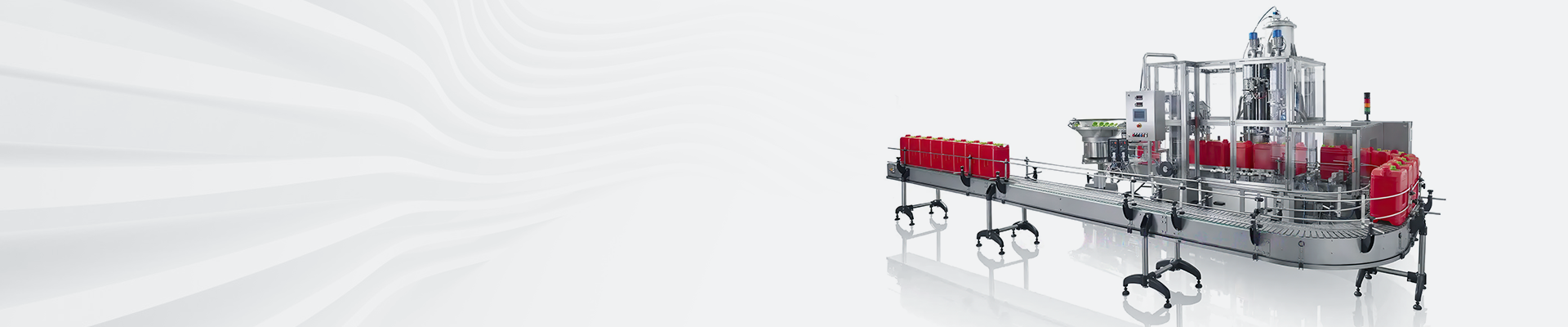
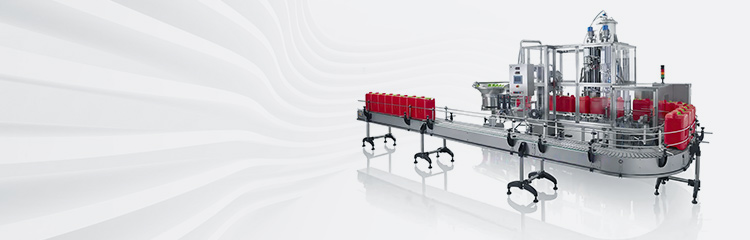

Summary:The liquid filling machine drives the empty barrel to the weighing pan under the filling machine through a chain to detect it and start filling. After filling, it enters the capping area, where the inner cap is placed, the inner cap is sealed, and the outer cap is pressed. Finally, the liquid filling machine passes Those who pass the capping test will proceed to the next step, otherwise they will enter the bucket picking area.
Liquid filling machine using SIMATIC software integration to realize the ease of use of PLC programming configuration and integration with the host group configuration system provides a powerful software platform, PROFIBUS-DP for high-speed data transmission at the field level, the master station periodically reads the input information from the slave station and periodically sends the output information to the slave station, the bus cycle time must be shorter than the master (PLC) The bus cycle time must be shorter than the master (PLC) program cycle time.
The Autofiller is a software for designing, configuring, programming and troubleshooting SIMATIC with dry. Users can write programs and configure hardware in STEP7, and download user programs and hardware configuration information to CPU or upload from CPU to PC. When the program download and debugging are completed, the PLC system can perform various automatic tasks. The performance of the control system already depends not only on the PLC CPU, but also by the PLC is located in the extended environment (i.e., network environment). The PROFIBUS network established for the control system's packaging line is a control network applied to SIMATIC at the unit level and at the field level, applying mixed-media transmission technology as well as token and master-slave logical topologies, which can be transmitted over twisted-pair cables or optical fibers at the same time.
The PROFTIBUS-DP network of the automatic filling system is a PROFIBUS system consisting of three masters and seven slaves, and the three masters form a token logic ring between them, so that when a certain master gets a token telegram, the master can execute the master's work within a certain period of time. During this period of time, you can communicate with all the slaves according to the master-slave communication relationship table, or you can communicate with all the masters according to the master communication relationship table.The programming interface and data viewing interface in TEP7 provide both offline and online views. The offline view shows the contents of the PO locally stored items and the online view shows the actual contents in the CPU. When the PC is connected to the PLC through the programming cable, an online connection can be established in STEP7.
The automatic filling machine consists of filling, capping, sealing, palletizing, weighing equipment and corresponding conveyor belts, supplemented by automatic control and automatic adjustment systems. When the four-liter barrel arrives at the feeding conveyor belt, the barrel is separated by the screw feeder and fed to the fixed scale platform under the oil injection nozzle of the rotating tank. Quantitative filling is performed by symmetrically configuring the piston cylinders round the perimeter of the rotating tank, with each piston connected to an axle ride by means of a connecting rod and sliding according to an inclined circumferential trajectory. Inclined circular motion of the first 180 degrees to make the piston rise, after 180 degrees to make the piston fall. When the piston is raised, the material is sucked into the piston cylinder from the upper oil tank controlled by the valve. When the valve connecting the piston cylinder and the oil injection nozzle is opened, the material is injected into the barrel below. Automatic filling machine selected bulk metering verification is based on the total flow of time and unit time to be clear, metering verification precision can be manipulated by the PLC to be clear, according to the industrial touch screen-touch display to detect the operation of the situation, can be changed online operation of the main parameters. PLC control with easy to write the program, the work of the stability of the characteristics of the use of easy, in the industrial production of machinery automation industry is widely used. The touch panel is a program controller terminal device (PT) that integrates a display and a sensor switch, and is a new generation of excellent industrial touch panel products. Designed specifically for the use of PLC program touch screen set of servers, input and output devices in one, adapted to the extreme industrial production.
The weighing and filling machine has both switching control and analog frequency conversion speed control. It can run automatically and continuously, and each movement point can be operated manually, so there are many input points corresponding to various operations and output points of action status information to be displayed. These I / O signals, if the electrical buttons, indicator light display, will greatly increase the hardware module and electrical wiring, the corresponding failure rate will increase. Quantitative filling machine using a combination of PLC and touch screen program. Touch screen screen is designed with special configuration software, and then downloaded to the touch screen through the computer's RS-232C serial communication port. PLC and touch screen communication through the serial interface, connectivity is simple.
Filling system is designed with a total of 13 digital input points, including: 10 cylinder motion sensors, 2 liquid level sensors, 1 photoelectric switch. Digital output points 35, of which: 24 filling head solenoid valve control, cylinder movement solenoid valve control 10, liquid storage tank solenoid valve control 1.
Frequency control system requires 1 analog input point and 1 analog output point. The speed measuring motor measures the rotational speed of the motor, the voltage value signal is connected to the analog input point, after comparing with the given value and PID operation, the result of the operation is output from the analog output point, which is used as the control signal of the frequency converter to realize the frequency conversion speed regulation. The main control unit adopts PLC product CPU224, plus two digital expansion modules EM223 and one analog expansion module EM235, and the touch screen adopts Taiwan-made PWS3260. The frequency conversion speed control system requires one analog input point and one analog output point. The speed measuring motor measures the rotational speed of the motor, and the voltage value signal is connected to the analog input point, after comparing with the given value and PID operation, the result of the operation is output from the analog output point, which is used as the control signal of the frequency converter to realize the frequency conversion speed regulation. The control program of the weighing and filling machine is prepared in the form of menu. The automatic functions include: run, pause, end, reset and so on. Manual functions include: advance, retreat, start, stop, etc. of all moving parts. The alternating button function in ADP3 configuration software is utilized for programming. When the button is pressed and lifted, the corresponding intermediate relay of the PLC is set, so that the PLC can realize the in/out control of a certain moving part. Initial value setting: set the parameters such as rotational speed and counting value according to the user's demand, and monitor the upper limit of the parameters, and give a prompt once it is out of bounds. Operation monitoring: monitor the state of each device of the system, such as the abnormal state of the inverter, motor, etc., timely power off to protect, and give alarms and prompts.