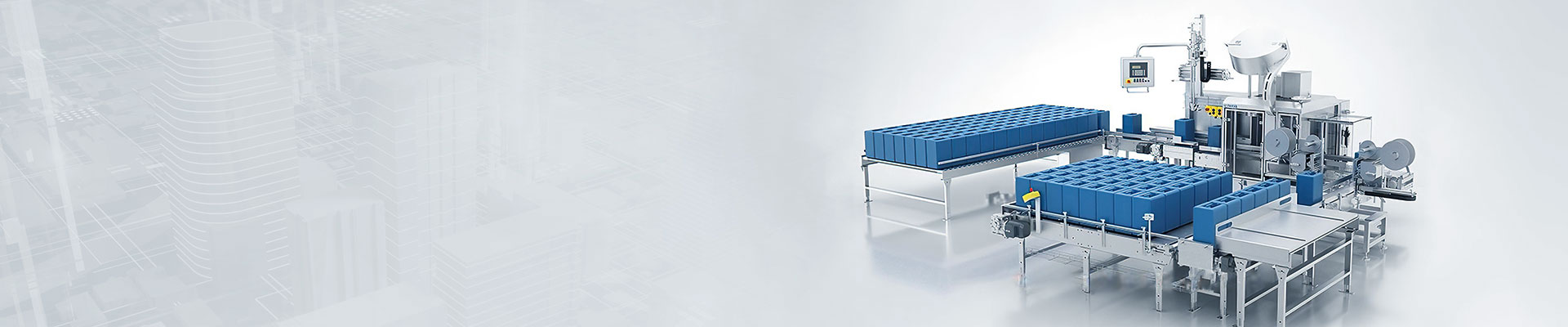
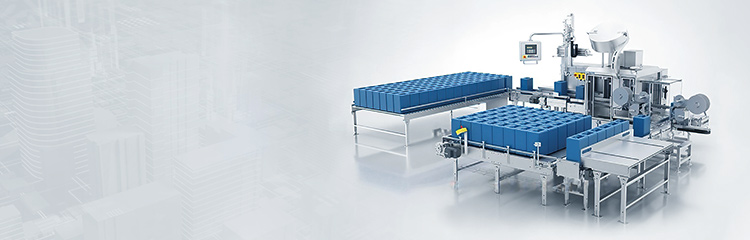
Automatic filling scale adopts filling nozzle positioning through CPM system or scanner, automatic de-plugging/plugging/moving nozzle/sealing station-filling head design, each barrel filling completion will display prompts, cumulative weight and number of times, the use of high-precision sensors and a new generation of digital control system, the filling accuracy to play a reliable guarantee. With debugging function switch, no filling during debugging, easy to operate. Automatic bottle spotting function, and can be connected to the computer to facilitate the query of filling volume at any time.

Liquid Filling machine production process PLC is the use of computer technology for centralized monitoring of the production process, filling, management and decentralized control of a new type of control technology. Can be supervised through the operating station of the entire production process, the whole process of tens to hundreds of monitoring points, centralized monitoring and surveillance control, real-time recording of production process parameters, resulting in the production process management reports, product quality management reports, production process history reports, such as consulting and printing, so as to make the production of stable product quality and product quality level, not only to ensure that the production of automatic filling machine safety and reliability. Reliability, but also to make the original production process operation process supervision into the computerized filling machine management mode.
The automatic filling machine collects and controls the data on the site, and the filling equipment is at the site control layer, which realizes collecting and controlling all kinds of signals on the site, and its main functions are as follows: communicating with the upper computer system, collecting and transmitting the information of the filling machine; collecting the analog input signals of the liquid level and frequency of frequency converter on the line; collecting the switching status signals of the pumps, solenoid valves, photoelectric switches, proximity switches, electric actuators, etc., and sending signals to control all kinds of valves according to the operation requirements; communicating with the weighing and filling machine to make the weighing and filling device control the servo motor to realize the precise control of the tank capacity; finally realizing the automatic control of the system. Real-time acquisition of pumps, solenoid valves, photoelectric switches, proximity switches, electric actuators and other switching signals, and according to the operational requirements of the output signal control of various valves on and off; and then communicate with the weighing and filling machine, so that the weighing and filling device to control the servomotor to achieve accurate control of the canned capacity; and ultimately to achieve automatic control of the system.
Technical Parameters
Maximum weighing capacity: 300kg
Quantitative range: 100kg~300kg
Graduated value: 100g
Canning accuracy: OIMLR61 x (0.2)
Canning speed: 10~20 cans/hour
Power supply: AC220V50Hz
Using air pressure: 0.5MPa
Control mode: 2-speed control
Conveying method: the tank adopts manual conveying method valve material: SUS-304 (optional: SUS-316)