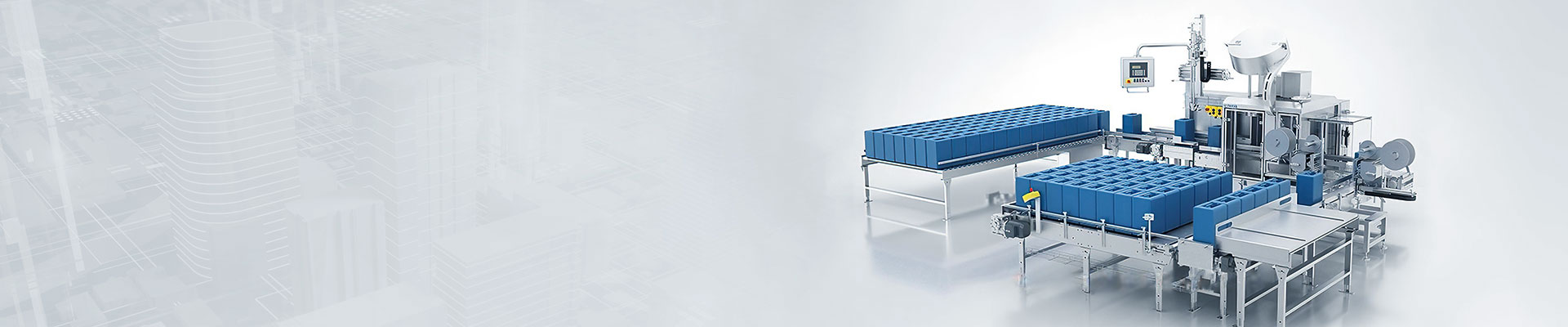
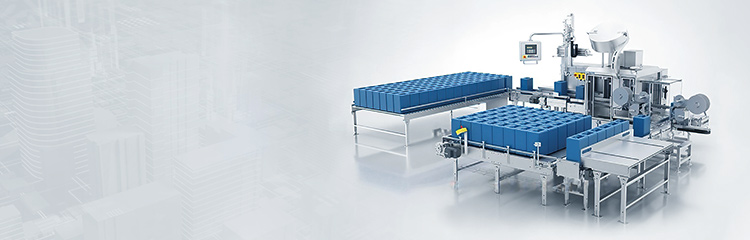
The automatic batching equipment is connected to the field weighing instrument through the bus, the control field equipment, the frequency converter of the weighing feeder, etc., which has a high degree of intelligence and fast processing speed. In the process of batching production, the main material and auxiliary materials are matched in a certain proportion to complete the measurement of the transported material. It is mainly responsible for real-time control of conveying and weighing process, fault detection, display and alarm, and adjustment of spiral speed by output signal to inverter.

Feeding system is a kind of control system used for automatic color mixing and dosing, which is composed of computer with dosing algorithm software. The application of this system can not only save a lot of labor and improve the production efficiency of the enterprise, but also bring great benefits to the production of the enterprise.
Weighing control system consists of weighing module and weighing instrument and communication cable, Windows operation, programming software and configuration software control using PID regulation of measurement deviation and frequency conversion speed control, frequency control in the hardware settings, parameter settings and software design process. Multi-output each batching and conveying production line strictly coordinated control, timely and accurate monitoring and regulation of material level weight. Connecting on-site weighing instrument, controlling on-site equipment and weighing Feeder frequency converter through bus, with higher degree of intelligence and fast processing speed. In the process of batching production process, the main material and auxiliary materials will be matched according to a certain proportion to complete the measurement of the conveyed materials. It mainly undertakes real-time control of the conveying and weighing process, and completes the role of fault detection, display and alarm, and at the same time outputs signals to the frequency converter to adjust the screw speed.
In the incoming storage tank batching, the material is mixed according to a certain ratio, and is sent directly into the mixing bin by the screw machine alone. Under the silo for the discharge screw machine, the screw machine speed adjustable, so as to regulate the amount of incoming feed, that is, to adjust the amount of material under the material. The weighing signal from the feeder is used by the automatic quality control system to adjust the speed of the discharge auger, thus automatically adjusting the amount of incoming feed and the ratio between the several feed amounts.
Dosing is accomplished by combining the following control requirements:
1 material flow requirements: interlocking between the various color mixing tanks, starting order against the material flow direction, the starting of the horizontal storage tanks have a certain time interval. The stopping sequence is in the direction of material flow, and there is a certain time interval between each other. When stopping, the time interval between the front and rear two color mixing tanks is determined by the running speed of a concentrate tank and the length of dosage.
2 Normal operation, the incoming material is mixed material powder, at this time the dosage is running, the spiral reversal.
3 When need to adjust the material dosage, if the extraction tank dosage running, storage tank running, raw materials into storage.