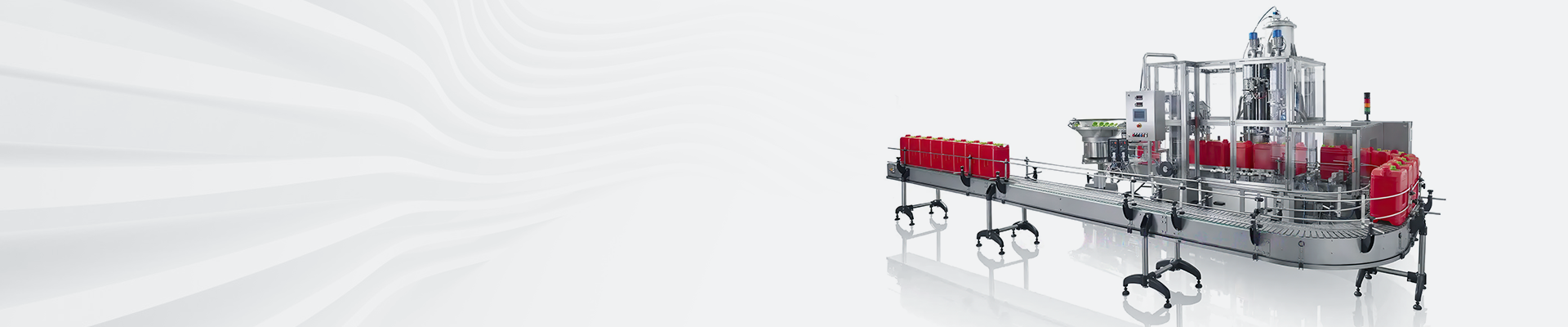
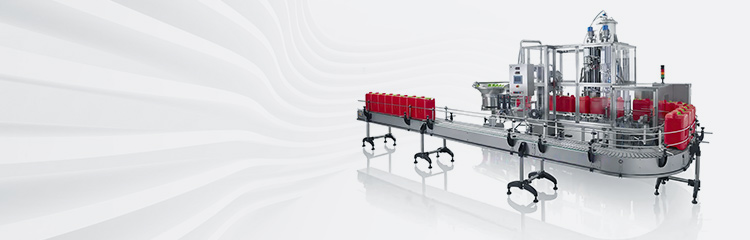

Summary:The DCS automatic batching system is based on the centralized management, decentralized control model, and the idea of digital and information-based environmental protection engineering. The MTBE device focuses on the construction of integrated management and control.
I. Overview of MTBE
With the development of high-performance gasoline engines, refineries have been given the task of producing high-octane gasoline. To improve the octane number of gasoline, firstly, we should try to improve the octane number of the base component gasoline, and secondly, we should blend in the appropriate amount of high-octane components. High octane components are mainly alkylated oil, stacked oil, isomerized oil and methyl tertiary butyl ether (MTBE for short), etc. MTBE has a boiling point of 55 degrees, relative density of 0.746, molecular weight of 88, properties similar to gasoline, and hydrocarbons are completely miscible with the gasoline physicochemical properties do not have a negative impact on its own high octane number, has a good resistance to explosion. Properties and uses of methyl tertiary butyl ether.
Methyl tert-butyl ether (MTBE), structural formula CH3-O-C(CH3)3. It is a colorless, transparent, volatile liquid. Toxic. Molecular weight 88.1. motor method octane number 101, research method octane number 117. boiling point at atmospheric pressure is 55.2 ℃, density at 25 ℃ is 735.5kg/m3. slightly soluble in water, solubility in water 6.9% (V/V). Ether can be dissolved in strong acid; ether and air contact to generate peroxide decomposition occurs after a strong explosion, the concentration in the air up to 1.6 ~ 8.4% explosion.
Process introduction
Methyl tertiary butyl ether (abbreviated as MTBE) is obtained by the synthesis reaction between methanol and isobutene in C4 fraction under the action of acid catalyst, this reaction is reversible exothermic reaction, the lower the reaction temperature is, the larger the equilibrium constant is, and the higher the conversion rate is; the reaction is completed in the liquid phase condition, and the speed is very fast.
This project belongs to the two-stage deepening conversion process (THC). The process is that the raw material (C4 fraction) is mixed with methanol into a one-stage reactor, and the product of the reaction goes into an azeotropic fractionation column. MTBE from the bottom of the tower is sent out of the plant as a product, and the methanol and C4 fraction azeotropes from the top of the tower are supplemented with methanol and enter the second stage reactor to continue the reaction. The second stage of the reaction product into the C4 fractionation tower, C4 fraction and methanol azeotropic discharge from the top of the tower, into the methanol water extraction tower; tower bottom out of the second stage of the reaction product (MTBE + methanol) can be sent out of the device with the bottom of the azeotropic fractionation tower out of the MTBE, or return to a section of the reactor to carry out the reaction again.C4 fraction, methanol mixture in the methanol water extraction tower to get separated, the C4 fraction is sent out of the device; methanol aqueous solution into methanol to continue to react. The C4 fraction is sent out of the unit; the methanol aqueous solution enters the methanol recovery tower. The separated methanol is sent back to the reactor for recycling.
Third, the operating conditions
Factors affecting the conversion rate and selectivity of the reaction are the reaction temperature and the molar ratio of methanol to isobutene.
1. Reaction temperature: at a certain isobutylene concentration and alcohol-ene ratio, the reaction temperature not only affects the conversion of isobutylene, but also affects the selectivity of MTBE, catalyst life and reaction rate. At low temperatures, the reaction rate is slow and the reaction conversion is controlled by kinetics. As the reaction temperature increases, the equilibrium conversion decreases, the reaction rate increases and the time required to reach equilibrium is shortened, so at high temperatures, the reaction conversion is controlled by thermodynamics. In order to increase the equilibrium conversion, prolong the life of the catalyst, reduce the side reactions and improve the selectivity, a lower reaction temperature should be used. The appropriate temperature is 50 to 80°C. Increasing the reaction temperature can increase the reaction rate, but the amount of dimethyl ether generated also increases with the increase of reaction temperature. Moreover, the catalyst will be burned when the reaction temperature exceeds 140°C. According to the characteristics of exothermic reaction, the conversion rate of isobutene is higher when the reaction temperature is low. Therefore, when the device is equipped with two reactors, one is often operated at a higher temperature to increase the reaction rate, and the other is operated at a lower temperature to ensure that the required high conversion rate.
2. Alcohol to alkene ratio: methanol and isobutylene molar ratio increases, can reduce the generation of isobutylene dimer and trimer, so the selectivity increases. In addition, the molar ratio of methanol and isobutene rises, the equilibrium conversion rate of isobutene also increases, so it is beneficial to improve the molar ratio of methanol and isobutene. However, a high molar ratio of methanol to isobutene will increase the concentration of methanol in the reaction product, thereby increasing the operating cost of the separation and recovery system. Therefore, on balance, a ratio of methanol to isobutene of 1.1 to l.2:1 is more appropriate.
3. Reaction pressure: the reaction pressure must keep the material in the liquid phase reaction, generally 0.8 ~ 1.4MPa.
4. Purity of raw materials: strong acid cation exchange resin catalyst in the H + will be replaced by metal ions and deactivate the catalyst, so the raw materials required to enter the reactor in the metal cation content is less than 1mg/kg; such as raw materials in the alkaline material will also neutralize the catalyst sulfonate, so this type of impurities should also be removed; C4 fraction in the water content must be limited to the general 300-500mg/kg. Because water and isobutylene side reaction to generate minbutanol.
The amount of isobutene content in the C4 fraction of raw materials varies greatly depending on the source. The isobutene content in the C4 fraction of catalytic cracking is low, which is suitable for oil refining, and the downstream products can be used as alkylation raw materials; while the C4 fraction of cracking C4 fraction after extraction of butadiene extraction of the remaining C4 fraction, the isobutene content is as high as 40-60%, which can be used as a chemical industry, that is, the conversion rate is > 99.5%, in order to satisfy the downstream needs of the production of 1-butene.
Fourth, the system control realization scheme
DCS automatic dosage system is based on the mode of centralized management, decentralized control, digitalization, informationization and environmental protection engineering, MTBE plant focuses on the construction of integrated management and control, and establishes an advanced, reliable, high-efficient, safe and easy to further expand the process control, monitoring and computer scheduling and management in one body and has a good openness of monitoring and control system, to complete the monitoring and automatic control of the entire process and all production equipment, to realize the process of 1-butene production. Complete the monitoring and automatic control of the entire process and all production equipment, to achieve the goal of "unmanned on-site, fewer people on duty at the terminus". We use HPCS3000 system to monitor the production data and control the control loop of the project, which perfectly realizes the automatic monitoring of the weighing and batching system. In addition, when designing, under the premise of ensuring advanced, reliable, open and safe, we always adhere to the principle of cost control.
a) Utilizing international advanced technology and today's high-tech achievements, we build a highly reliable, efficient and highly automated feeding system.
b) The configuration of testing instrument meets the requirements of process testing, process equipment control and safe production.
c) Instrument selection based on reliability, advanced, and ensure the accuracy of the process requirements and real-time requirements, as well as easy maintenance, stable operation.
d) The weighing and feeding system is based on decentralized control and centralized scheduling for MTBE production process, which reaches the international advanced level.
e) The configuration of hardware and software of the feeding system is in line with the relevant national and international standards to ensure the reliability and openness of the product to meet the needs of product expansion.
f) The complete set of batching equipment utilizes the special control equipment provided by the manufacturer, and realizes the data communication with the monitoring system through the communication port. The communication network adopts open communication protocol and statute in line with international standards, which is convenient for system expansion and upgrading.
1 dosage hardware preparation
1) The whole set of HPCS3000 system is configured with 3 operator stations, 1 of which is also an engineer station, 1 pair of redundant on-site automatic dosage system and I/O modules. The network, power supply and important I/O modules redundant configuration.
2) The engineer station (part-time operator station) completes the configuration modification and loading, including: database, graphics, control algorithms, report configuration, parameter configuration, operator station, on-site automatic dosage system and process I/O module configuration configuration, data loading.
3) The operator station carries out the monitoring and management of the production site, including: process flow chart display, report printing, control operation, historical trend display, alarm management, etc.
4)Field batching machine, also called I/O station, is an important station for the system to realize data acquisition and process control, which mainly completes the functions of data acquisition, engineering unit transformation, control and interlocking algorithm, control output, and transmitting data and diagnostic results to the supercomputer through the system network, and so on.
5) The on-site feeder consists of four parts: DPU, intelligent I/O unit, power supply unit and special cabinet. On the DPU and intelligent I/O unit, real-time control software and I/O unit operation software are cured respectively.
6)The distributed structure is adopted inside the site, and connected with the system network is the DPU of the on-site automatic dosage system with redundant configuration.The DPU realizes the connection with each intelligent IO unit through the control network.
7) The system adopts I/O module DPU to form a ready-made automatic batching system, adopting MODBUS field bus technology, constituting an advanced and reliable DCS distributed mixer. the I/O module and the base form a field module unit,. The field confusion machine is mainly composed of I/O module, chassis and power switching box.
8) System network structure: weighing and batching system network is divided into two levels from top to bottom, control network and system network, control network realizes the communication between on-site automatic batching system and process I/O module; system network realizes the interconnection between engineers' station, operators' station and on-site automatic batching system.
9) The system network adopts double redundant structure with high reliability, which can ensure that the system communication will not be affected in case of any network failure.
10)The system network is composed of 100M industrial Ethernet, which is used for the connection of engineer station, operation station and on-site automatic batching system, and completes the data downloading of on-site automatic batching system and communication automatic batching system, and the real-time data communication between upper computer and on-site automatic batching system and communication automatic batching system.
11) Control network consists of MODBUS dosage system, used to realize the communication between on-site automatic dosage system and process I/O module, and complete the real-time input and output data transmission.Modbus is specially designed for the communication between automatic weighing and dosage system and decentralized I/O at equipment level. It can meet the high-speed transmission, but also has the characteristics of simple and practical, economical and so on.
2 process and control requirements:
MTBE production process: isobutylene and methanol mixed under pressure, into the reaction tower after the first reaction, and then fractionation (completed in the same tower) to generate methyl tertiary butyl ether (a gasoline additive to improve gasoline grade), referred to as MTBE.
The 30,000 tons/year MTBE plant contains 22 PID control loops, including three cascade control loops and one ratio control loop;
Cascade loop 1: TI2238 at the bottom of the recovery tower is the outer loop, and E210 steam flow FIC2212 is the inner loop;
String stage loop 2: C4 raw material tank level LICA2201 as the outer loop, C4 from the tank area from the flow FIC2201 as the inner loop. String stage loop 3: Recovery tower level LICA2208 as the outer loop, extraction water flow FIC2210 as the inner loop.
C4 butene material flow FT-2203 and methanol flow FT-2204 implementation of the ratio of the molar amount of control, in which the methanol flow ratio is slightly higher than the C4 butene material, the ratio can be modified.
V. Main process control
1. etherification unit
1.1, alcohol-ene ratio is a key indicator of the operation, if the alcohol-ene ratio is too low or methanol interruption, will cause the reactor bed temperature is higher than the target control range, and even burn the catalyst, so we must do a careful adjustment to ensure that the alcohol wash ratio is stable at 1.03 ± 0.1. If you find that the methanol is interrupted, immediately stop pumping residual carbon four to the reactor feed to avoid the accident of burning the catalyst; at the same time, instrumentation measurement and analysis should be accurate; and the meter should be accurate. Meanwhile, the instrument measurement and analysis should be accurate;
1.2、Dehydration of etherification catalyst should be clean, otherwise it will produce a large number of by-products and prolong the time of product qualification, so the time of methanol soaking should be sufficient in order to get rid of the water in etherification catalyst cleanly;
1.3. In the initial stage of feeding, the control of bed temperature is difficult, and the main control means are as follows:
Pay close attention to the catalyst bed temperature and the trend of temperature increase, and relieve pressure to the flare gas discharge system in time; the feeding amount should be small to reduce the heat release; adjust the alcohol-ene ratio, and rather have some excess methanol at the initial stage of feeding; and set up the external circulation as soon as possible;
2.Reaction distillation unit
2.1, the dehydration of etherification catalyst should be clean, otherwise it will produce a large number of by-products and prolong the time of product qualification, so the time of methanol soaking should be sufficient in order to get rid of the water in the etherification catalyst cleanly;
2.2, adjust the alcohol-ene ratio, in the early feeding would rather methanol excess some;
2.3, tower heating, to strictly control the rate of heating, heating too fast will cause dry tower or liquid flooding, prolonging the product qualified time;
2.4, in the initial feeding of methanol excess, in order to reduce the impact of methanol on the operation of the reactive distillation tower, under the premise of maintaining the liquid level of the reactive distillation tower, the unqualified MTBE discharged to the self-contained tank area of the unqualified product tank;
2.5. In the process of the operation of the reactive distillation tower, it is necessary to maintain the stability of the operating pressure as much as possible, and reduce the fluctuation of the tower pressure, otherwise MTBE is easy to flash to the top of the tower, which prolongs the time for the qualified products to be extracted from the top of the tower of the reactive distillation tower A;
3. Methanol recovery unit
3.1 material to water ratio of methanol recovery unit is an important indicator, material to water ratio of high and low both affect the quality of carbon tetra after washing, but also affects the operation of the recovery tower. Material to water ratio is high, extracted carbon tetra in the methanol is easy to exceed the standard; material to water ratio is low, so that the methanol concentration in the extraction water is low, which will lead to the top of the recovery tower tower extracted methanol products are not qualified or in order to achieve the same quality of the recovered methanol so that the operating costs increase (i.e., increase the reflux ratio). Therefore, to maintain the material to water ratio of 5 to 6, and between the methanol concentration of 7 to 10% (by weight), usually maintained at 8% (by weight)
3.2, to maintain the water washing operation pressure is stable. Operating pressure against, so that the extraction of residual carbon tetra in the methanol and water exceeds the standard; operating pressure is high, it will affect the safety of the equipment or safety valve jump. Can be from the following aspects to maintain the water washing tower operating pressure:
(1) Carbon tetra feed after ether should be stable;
2) Tower pressure regulation is sensitive;
3) Stabilizing the water feed;
4) Stabilize the interface;
5) Stabilize the feed water temperature.
3.3, the operation of the recovery tower: first of all, to maintain the operating pressure of the tower, reduce tower pressure fluctuations, otherwise easy to flash the water to the top of the tower, so that the recovery of methanol is not qualified; the second is to stabilize the interface of the washing tower and the amount of recycled water to reduce the amount of carbon 4 into the recovery tower.
Sixth, HPCS system introduction
HPCS-3000, 4000 + decentralized automatic dosage system is based on many years of research at home and abroad on a variety of DCS product technology, brings together many years of experience in power generation, paper, chemical and other production process control of the latest new generation of DCS products; weighing and dosage system is a blend of computers, networks, databases, information technology and automated control technology as a whole of industrial information technology series of products.
Batching system system of open structure, modular design technology, reasonable hardware and software configuration and easy to expand the characteristics of the system, can be widely used in the decentralized control of power plants, power plant scheduling and management information systems, substation monitoring, power grid automation, iron and steel enterprises, blast furnace monitoring, process automation in the chemical industry and paper mill process automation.